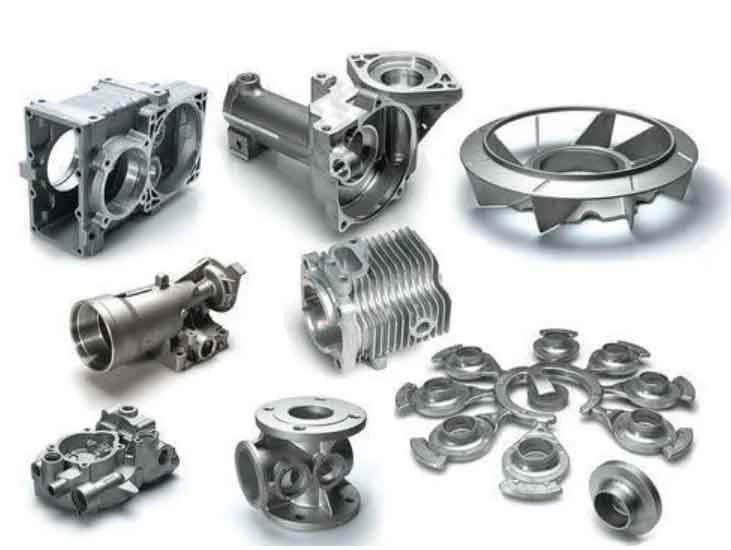
Welding grey cast iron components can be challenging due to the material’s brittle nature, susceptibility to cracking, and potential for heat-affected zone (HAZ) issues. The presence of graphite flakes in the microstructure makes grey cast iron more prone to cracking during welding. However, with careful preparation and the use of appropriate welding techniques, successful welding of grey cast iron components can be achieved. Here are some challenges and solutions in welding grey cast iron:
- Preheating and Post-Weld Heat Treatment (PWHT):
- Challenge: Grey cast iron’s brittleness can lead to cracking if the welding process generates significant thermal stresses.
- Solution: Preheating the component before welding can help reduce thermal gradients and minimize the risk of cracking. Additionally, applying a PWHT after welding can help relieve residual stresses and improve the weld’s ductility.
- Welding Techniques:
- Challenge: Traditional welding processes, such as conventional arc welding, can introduce excessive heat, leading to cracking and distortion in grey cast iron.
- Solution: Low-heat welding processes, such as gas tungsten arc welding (GTAW/TIG) and gas metal arc welding (GMAW/MIG), are often preferred for welding grey cast iron. These processes provide better control over the heat input, reducing the risk of cracking.
- Pre-Weld Preparation:
- Challenge: Proper preparation of the joint and the surrounding area is crucial to avoid impurities and contamination that can lead to poor weld quality and cracking.
- Solution: Clean the surfaces to be welded thoroughly, remove any surface impurities or oils, and ensure a precise fit-up to minimize gaps.
- Welding Filler Material:
- Challenge: Choosing the right welding filler material is essential to match the material properties and reduce cracking risks.
- Solution: Nickel-based welding filler materials, such as Ni-Fe or Ni-Cu alloys, are commonly used for welding grey cast iron. These fillers offer a better match in thermal expansion and lower brittleness, reducing the risk of cracking.
- Controlled Cooling Rate:
- Challenge: Rapid cooling after welding can lead to increased brittleness and cracking in the HAZ.
- Solution: Employing heat blankets or insulation to control the cooling rate can help prevent rapid cooling and reduce the risk of cracking.
- Avoiding Excessive Weld Size:
- Challenge: Large weld sizes can lead to increased residual stresses and brittleness in the weld area.
- Solution: Aim to keep the weld size to a minimum while ensuring adequate strength and integrity for the intended application.
- Post-Weld Inspection:
- Challenge: It is essential to inspect the weld thoroughly to identify any defects or potential issues.
- Solution: Utilize non-destructive testing methods, such as ultrasonic testing or radiographic examination, to check for defects and ensure the weld’s quality.
Due to the challenges associated with welding grey cast iron, it is advisable to consult with welding experts or metallurgical engineers with experience in working with grey cast iron components. Proper preparation, the selection of suitable welding techniques and filler materials, and careful control of the welding process are key to successfully welding grey cast iron components while ensuring their integrity and performance.