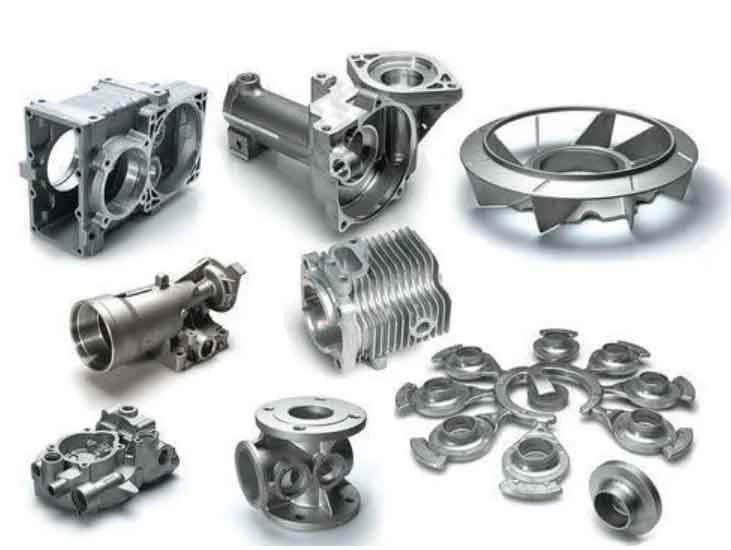
Grey cast iron foundries face several challenges in their quest to advance the casting process. These challenges often revolve around improving efficiency, sustainability, and product quality. However, innovations and advancements in technology have enabled foundries to overcome many of these challenges and enhance the grey cast iron casting process. Here are some of the key challenges and innovations in grey cast iron foundries:
Challenges:
- Energy Consumption: The foundry process requires substantial energy for melting, molding, and casting operations. High energy consumption can lead to increased production costs and environmental impact.
- Environmental Impact: Traditional foundry processes can generate significant emissions and waste, contributing to environmental concerns.
- Recycling and Waste Management: Effective recycling and waste management of scrap materials, sand, and other by-products are critical for sustainable foundry operations.
- Quality Control: Ensuring consistent quality in castings can be challenging due to variations in the casting process and material properties.
- Productivity and Lead Time: Meeting production demands and reducing lead times while maintaining quality can be a complex balancing act.
- Health and Safety: Foundries must prioritize the health and safety of workers due to potential hazards associated with molten metal and the casting process.
Innovations:
- Digitalization and Simulation: The use of computer-aided design (CAD) and simulation software allows foundries to optimize casting processes, predict defects, and improve efficiency before actual production.
- Robotics and Automation: Automation of certain foundry tasks, such as pouring and material handling, enhances productivity, reduces manual labor, and improves safety.
- Energy-Efficient Furnaces: Advancements in furnace technology, such as induction melting and energy-efficient burners, help reduce energy consumption in the melting process.
- Sustainable Materials and Additives: Foundries are exploring the use of sustainable materials and additives that improve sand reclamation, reduce waste, and enhance the overall environmental performance of the casting process.
- Process Monitoring and Control: Real-time monitoring and data analysis enable better control over casting parameters, ensuring consistent quality and reducing scrap rates.
- Green Sand Reclamation: Improved sand reclamation processes allow foundries to recycle and reuse sand, reducing the need for new sand and minimizing waste.
- 3D Printing for Patterns and Cores: Additive manufacturing, such as 3D printing, enables the production of complex sand patterns and cores, reducing pattern-making time and costs.
- Advanced Non-Destructive Testing (NDT): Innovations in NDT techniques, such as digital radiography and ultrasonic testing, improve the detection of defects and ensure the integrity of castings.
- Lean Manufacturing and Process Optimization: Adopting lean principles and process optimization techniques can streamline production and reduce lead times.
By embracing these innovations and addressing the challenges, grey cast iron foundries can modernize their operations, improve sustainability, enhance product quality, and maintain their position as valuable contributors to various industries.