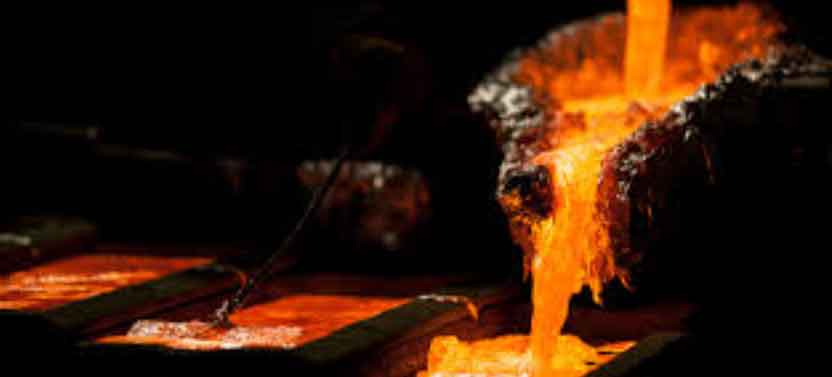
The casting industry in China has undergone a significant revolution in recent years, driven by innovations and advancements in technology, processes, and materials. Here are some key innovations and advancements that have revolutionized the industry:
- Automation and Robotics: Chinese foundries have embraced automation and robotics in various casting processes. Automated systems are used for tasks such as mold preparation, pouring, and finishing, improving efficiency, reducing labor costs, and enhancing overall production quality.
- Digitalization and Data Analytics: Digital technologies, such as computer-aided design (CAD), computer-aided manufacturing (CAM), and simulation software, have transformed the casting process. Digital tools enable precise mold design, virtual prototyping, and casting simulations, optimizing designs, reducing errors, and shortening lead times.
- 3D Printing and Additive Manufacturing: Additive manufacturing technologies, including 3D printing, have made significant advancements in the casting industry. Metal 3D printing allows for the production of complex geometries, rapid prototyping, and customized designs with reduced material waste.
- Advanced Materials and Alloys: Chinese foundries have focused on the development and application of advanced materials and alloys, such as high-strength steels, aluminum alloys, and titanium alloys. These materials offer improved properties, including strength, weight reduction, and corrosion resistance, expanding the range of casting applications.
- Process Optimization and Simulation: Chinese foundries have invested in process optimization and simulation techniques to enhance production efficiency and quality. Simulation software allows for the optimization of gating and riser systems, mold filling analysis, and solidification modeling, resulting in improved casting quality and reduced defects.
- Energy Efficiency and Environmental Sustainability: Chinese foundries have made significant efforts to improve energy efficiency and reduce environmental impact. Technologies, such as energy-efficient furnaces, waste heat recovery systems, and emission control measures, are widely adopted to minimize energy consumption and emissions.
- Quality Control and Inspection Technologies: Chinese foundries have implemented advanced inspection technologies to ensure product quality and consistency. Non-destructive testing methods, such as X-ray and ultrasonic testing, are used for defect detection, while optical and laser-based inspection systems ensure dimensional accuracy.
- Industry Collaboration and Research: Collaboration between Chinese foundries, research institutions, and industry associations has accelerated innovation in the casting industry. Joint research projects, knowledge exchange, and technology transfer initiatives have contributed to advancements in materials, processes, and casting technologies.
These innovations and advancements in the Chinese casting industry have not only improved production efficiency and product quality but have also positioned China as a global leader in the industry. Chinese foundries are now capable of producing complex components with high precision, meeting stringent quality requirements, and offering competitive solutions to various industries worldwide. Continued investment in research and development, adoption of emerging technologies, and commitment to sustainable practices will further drive the revolution in the casting industry in China.