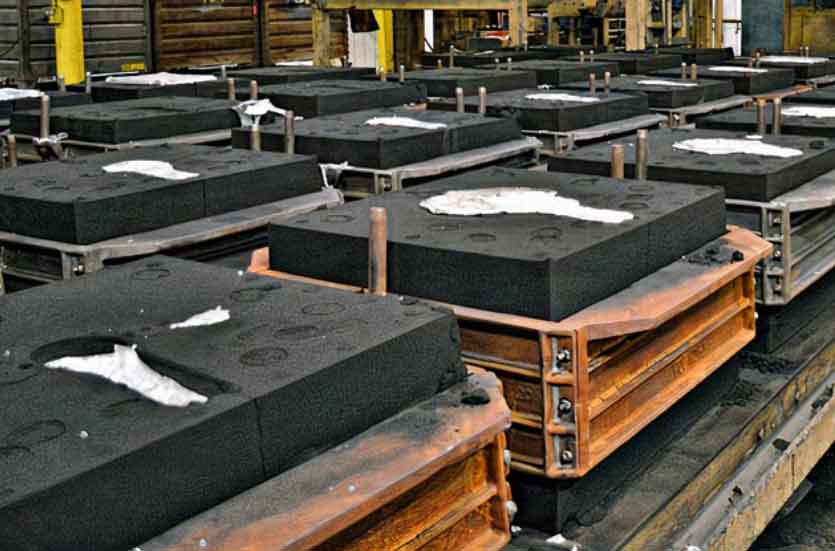
Resin sand casting plays a transformative role in turning design concepts into tangible objects. Here’s a step-by-step overview of how resin sand casting brings designs to life:
- Design Concept: The process begins with a design concept or idea for the desired metal object. This can be a product design, a prototype, or a customized component.
- Pattern Creation: The next step is to create a pattern of the object to be cast. In resin sand casting, a foam pattern is typically used. The pattern is carved, CNC machined, or 3D printed from foam material to replicate the shape and details of the final object.
- Mold Preparation: Once the pattern is ready, a mold is created around it using a mixture of sand and resin. The sand mixture is packed around the pattern, ensuring that it captures all the intricate details and features of the pattern. The mold is typically made in two or more halves to facilitate pattern removal and casting.
- Pattern Removal: After the mold has been prepared and cured, the foam pattern is removed from the mold. This leaves behind a cavity in the shape of the pattern within the sand mold.
- Metal Casting: The prepared mold is then securely closed, and molten metal is poured into the cavity. The metal fills the void left by the foam pattern, taking its shape and replicating its details. The molten metal solidifies within the mold.
- Cooling and Solidification: The casting is allowed to cool and solidify within the mold. The cooling time depends on the size and complexity of the object being cast. During this stage, the metal undergoes a phase transformation from liquid to solid, adopting the shape of the mold.
- Mold Breakout and Finishing: Once the metal has solidified, the mold is broken open, revealing the solid metal casting. The casting is removed from the mold and undergoes various finishing processes, including trimming excess material, removing any surface imperfections, and achieving the desired surface finish.
- Post-Casting Processes: Depending on the application and desired specifications, additional post-casting processes may be performed. These processes can include heat treatment, machining, surface coating, or any other necessary steps to achieve the desired final product.
- Quality Control: Throughout the process, quality control measures are implemented to ensure that the final casting meets the required standards and specifications. This includes inspections for dimensional accuracy, surface quality, and structural integrity.
- Final Product: The result is a finished metal object that closely resembles the original design concept. The casting can now be used as a component, assembly, or final product, depending on the intended application.
Resin sand casting transforms design concepts into tangible metal objects by leveraging the mold-making capabilities and the casting process. It enables the creation of complex and detailed components, offering flexibility, customization, and the ability to produce objects in various sizes and materials. This process bridges the gap between design and reality, allowing manufacturers and designers to bring their ideas to life with precision and accuracy.