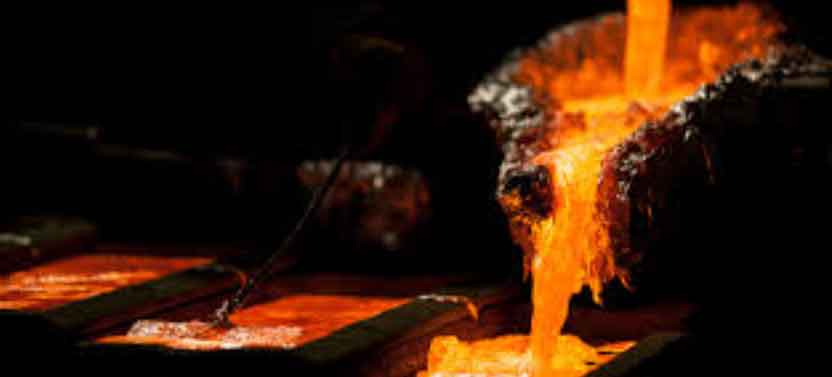
China’s casting industry has harnessed the power of technology to achieve remarkable success and become a global leader in the field. By leveraging advanced technologies, the industry has transformed its operations, enhanced product quality, improved efficiency, and gained a competitive edge in the global market. Here are some key ways in which technology has propelled China’s casting industry forward:
- Computer-Aided Design (CAD) and Simulation: CAD software has revolutionized the design phase of casting production. It enables precise and complex mold designs, streamlines the product development process, and reduces time-to-market. Simulation software allows manufacturers to simulate and optimize casting processes, predicting potential defects, and ensuring optimal casting quality.
- Advanced Casting Techniques: China’s casting industry has embraced advanced casting techniques such as investment casting, die casting, and sand casting. These techniques allow for the production of intricate and complex castings with high precision. Through the adoption of advanced equipment and machinery, manufacturers have enhanced the casting process, resulting in improved product quality and reduced scrap rates.
- Robotics and Automation: Chinese foundries have integrated robotics and automation into their manufacturing processes. Robots are employed for tasks such as mold handling, pouring, trimming, and inspection. Automation not only improves efficiency and consistency but also reduces labor costs and enhances workplace safety. Automated systems enable continuous production and provide real-time monitoring and control of casting processes.
- 3D Printing: Additive manufacturing, or 3D printing, has made significant inroads in China’s casting industry. It allows for the rapid production of prototypes, complex geometries, and customized castings with reduced lead times. 3D printing technology complements traditional casting processes, enabling manufacturers to create intricate patterns and molds with high precision and efficiency.
- Digitalization and Data Analytics: Digitalization has transformed China’s casting industry by enabling the collection, analysis, and utilization of vast amounts of data. Sensors and IoT devices are employed to monitor and optimize production parameters, machine performance, and quality control. Data analytics tools help manufacturers identify trends, detect anomalies, and make data-driven decisions to improve casting quality, optimize resource utilization, and enhance overall efficiency.
- Augmented Reality (AR) and Virtual Reality (VR): AR and VR technologies are being adopted in China’s casting industry for training, process visualization, and quality inspection. These technologies provide interactive and immersive experiences, aiding in training new operators, optimizing workflow, and identifying potential issues in the production process.
- Smart Manufacturing and Industrial Internet of Things (IIoT): The integration of smart manufacturing principles and IIoT has brought about a new era of connectivity and data exchange in China’s casting industry. IIoT-enabled devices and systems allow for real-time monitoring, predictive maintenance, and remote control of manufacturing processes. Smart manufacturing technologies optimize productivity, reduce downtime, and enhance overall operational efficiency.
- Collaborative Robotics (Cobots): Collaborative robots, or cobots, have gained popularity in China’s casting industry. These robots work alongside human operators, assisting in repetitive and physically demanding tasks. Cobots enhance productivity, improve ergonomics, and contribute to a safer working environment.
China’s casting industry has embraced technology at every stage of the manufacturing process, from design to production and quality control. The industry’s adoption of advanced technologies has not only elevated its capabilities but also enabled manufacturers to offer customized solutions, meet stringent quality requirements, and compete globally. By harnessing technology for success, China’s casting industry continues to innovate, evolve, and shape the future of the manufacturing landscape.