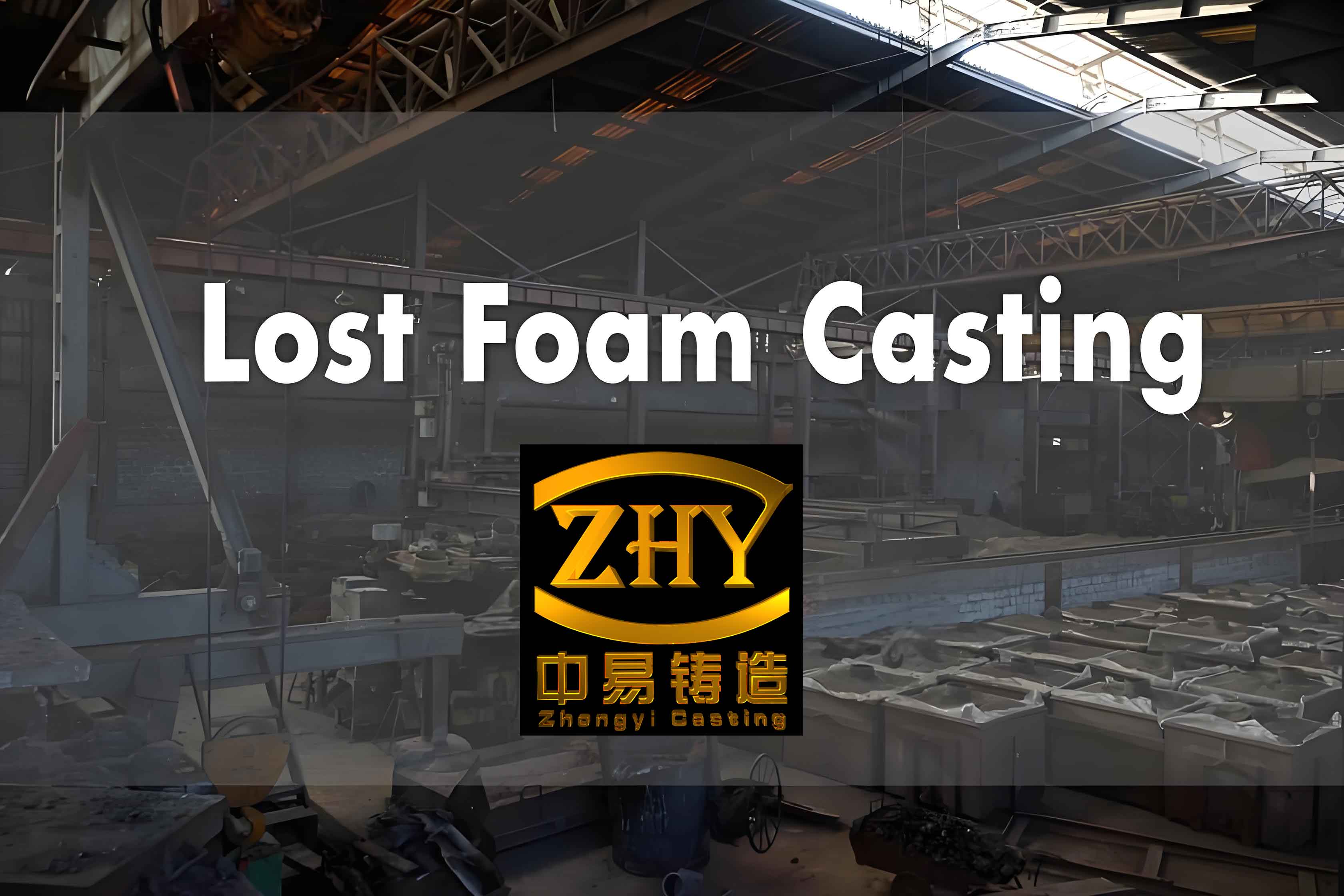
Lost foam casting, also known as negative pressure full mold casting, has been developed to a considerable scale since its invention by Americans in 1956 and has been successfully applied in industrial production by the 1980s. From the production of single-piece and small-batch large parts to the mass production of small parts on an assembly line, from the production of simple non-machined parts to that of complex machined parts, the industrial production in countries such as the United States, Italy, Germany, and Japan is more representative. By the 1990s, the use of lost foam casting methods for automotive castings had gradually developed, and up to now, there are more than 3,000 manufacturers in China using the lost foam casting process, but most of them are small-scale single-piece or small-batch casting production. At present, the lost foam casting technology in China is still in the stage of technological maturity, and the characteristics and laws of casting still need to be deeply understood, especially the theoretical research on the filling characteristics of molten metal, the properties of the coating, and the pyrolysis characteristics of the pattern has not been fully mastered, resulting in some casting defects in the castings, such as carbon increase, sand inclusion, sand sticking, deformation of the castings, and collapse of the box during pouring, and the difficulty in removing the coating after pouring. Since 2009, I have been committed to the research and development of the lost foam casting process for carbon steel castings. This article will analyze casting defects such as carbon increase, porosity, slag inclusion, backspray, and negative pressure cutting that are prone to occur during the trial production process, and provide some guidance for the better application of this process in the production of steel castings.
1.Common Casting Defects and Preventive Measures
1.1 Carbon Increase Defect
Carbon increase is one of the common casting defects in the lost foam casting process of steel castings. The foam pattern material is mainly composed of carbon and hydrogen, which decomposes sharply under high-temperature molten steel, producing hydrogen and free carbon. Since the affinity of hydrogen for oxygen is stronger than that of carbon, the hydrogen decomposed at high temperature first combines with the oxygen in the gap of the pattern to form water vapor and is discharged, while a large amount of free carbon decomposed remains in the mold and infiltrates the surface of the molten steel, resulting in carburization of the casting surface, that is, carbon increase. According to relevant literature and experiments, it is found that carbon increase has a certain regularity, that is, carbon increase mainly occurs on the surface of the casting, and the core hardly increases carbon, and there is no carbon increase near the inner gate, and the farther away from the inner gate, the more serious the carbon increase. In view of the mechanism of carbon increase, the following measures can be taken to basically control the carbon content of the casting within the process requirements:
(1) Select high-quality foam plastics
The quality of foam plastics directly affects the gasification speed of the pattern and the morphology of the pyrolysis products during the pouring process. High-quality foam plastics have low carbon content and high molecular weight, and the pattern density is lower under the same foam strength. The selection of raw bead particles with less gas generation and low carbon content and molded foams with low bulk density and light weight is the first choice for the production of steel castings by lost foam, and it is also the most effective way to solve the problem of carbon increase in steel castings at present.
(2) Choose a reasonable pouring process
The design of the pouring process for lost foam casting should be able to accelerate the gasification of the mold material, reduce and stagger the contact and reaction time between the liquid and solid phases in the decomposition products and the molten steel, and reduce or avoid the carburization of the steel castings. It mainly includes controlling the pouring temperature and pouring speed, good coating permeability and dry sand mold permeability, appropriate negative pressure of the mold wall, and the use of anti-carburization coatings, etc.
(3) Utilize the characteristic that the farther away from the inner gate, the more serious the carbon increase, set a riser at the farthest end from the inner gate or at the highest point of the casting, so that the steel water with serious carbon increase pollution entering the mold cavity first enters the riser, and the casting body obtains purer molten steel.
(4) “Burn first and then pour”, that is, burn the foam plastic in the cavity to form a cavity, and then pour the molten metal.
Casting Defect | Cause | Preventive Measure |
---|---|---|
Carbon Increase | Decomposition of foam pattern material, resulting in the presence of free carbon that infiltrates the surface of the molten steel. | Select high-quality foam plastics with low carbon content and molecular weight. Choose a reasonable pouring process, including controlling the pouring temperature, pouring speed, coating permeability, and mold permeability. Set a riser at the farthest end from the inner gate or at the highest point of the casting. “Burn first and then pour” to remove the foam plastic in the cavity. |
1.2 Porosity Defect
According to the causes, the porosity generated in the lost foam casting of steel castings is divided into the following four categories:
(1) Porosity caused by the entrapment of the pyrolysis products of the foam pattern in the molten metal
During the pouring and filling process, turbulence occurs, or during the gasification process, part of the pattern is surrounded and pyrolyzed by the molten metal, and the generated gas cannot be discharged from the molten metal, resulting in porosity. This kind of porosity is large and numerous, and the inner surface has carbon black.
Preventive measure: Improve the process to make the molten steel fill the mold smoothly without turbulence; reasonably increase the pouring temperature and increase the negative pressure (if porosity is caused by turbulence, reduce the negative pressure); improve the permeability of the coating and the molding sand.
(2) Porosity caused by poor drying of the foam pattern and coating
When the foam pattern coating is not dried sufficiently and the foaming agent content is too high, a large amount of gas will be generated during pouring, causing porosity.
Preventive measure: Fully dry the foam pattern (operate according to the molding process characteristics of the mold material foaming); the coating must be completely dried, and the addition amount of the foaming agent must be strictly controlled.
(3) Porosity caused by excessive use of pattern binders
The binder of the pattern has a large gas generation amount, and excessive use and slow gasification can easily cause the gas to be entrained into the molten steel and form porosity.
Preventive measure: Select a low-gas-generating model binder, and use as little adhesive as possible while ensuring a firm bond.
(4) Porosity caused by the entrapment of air during pouring
When the sprue is not filled during pouring, air is easily entrained, and if these gases cannot be discharged in time, porosity is easily caused.
Preventive measure: Design a reasonable pouring system to ensure that the molten metal flows smoothly during filling without entraining air; when using a closed pouring system, ensure that there is a certain amount of molten metal in the pouring cup to ensure that the sprue is in a filled state; use a hollow sprue mold to reduce the gas generation amount, which is conducive to preventing the generation of porosity.
(5) Porosity caused by the quality problem of molten steel smelting
During the smelting process of carbon steel, gas is contained, and pre-deoxidation treatment and final deoxidation treatment are required. If the deoxidation is not sufficient, oxygen will remain in the molten steel, forming porosity.
Preventive measure: During the smelting process, strictly follow the smelting process, perform deoxidation treatment before pouring, and purify the molten steel.
Casting Defect | Cause | Preventive Measure |
---|---|---|
Porosity | Entrapment of pyrolysis products of the foam pattern, poor drying of the foam pattern and coating, excessive use of pattern binders, entrapment of air during pouring, and quality problem of molten steel smelting. | Improve the process to make the molten steel fill the mold smoothly without turbulence. Increase the pouring temperature and negative pressure appropriately. Fully dry the foam pattern and the coating, and strictly control the addition amount of the foaming agent. Select a low-gas-generating model binder and use as little adhesive as possible. Design a reasonable pouring system to ensure that the molten metal flows smoothly during filling without entraining air. Perform deoxidation treatment before pouring to purify the molten steel. |
1.3 Slag Inclusion Defect
The slag inclusion defect refers to the casting defect formed by the entry of dry sand grains, coatings, and other inclusions into the casting during the pouring process, which is a relatively common casting defect in the production of lost foam castings. On the machined surface of the casting, white or gray-black inclusion spots can be seen, distributed individually or in patches. The white ones are quartz sand particles, and the gray-black ones are slag, coating, residues after pyrolysis of the foam model, and other inclusions.
After the lost foam casting is cooled and removed from the box, it can be determined whether there is sand ingress or slag inclusion defect based on the surface condition of the casting and the pouring system. In production practice, if the pouring cup, sprue, runner, ingate, and the surface or connection of the gate, as well as the surface of the casting, have serious sand sticking or crack-like sand sticking, then all parts from the pouring cup, sprue, runner, ingate to the casting may cause sand ingress. Among them, the unsealed sprue is the main reason for the sand ingress or slag inclusion defect. In addition, process parameters such as the net pressure head of the pouring system, the pouring temperature, the negative pressure, the particle size of the dry sand, the transportation process of the pattern, and the operation of boxing are all important reasons for the slag inclusion and sand ingress defects of the castings.
The slag inclusion defect is a major problem in lost foam casting production and is a systematic project. Only by taking systematic measures and careful operation in these links can the slag inclusion defect of the castings be reduced and basically eliminated to obtain high-quality castings.
Casting Defect | Cause | Preventive Measure |
---|---|---|
Slag Inclusion | Entry of dry sand grains, coatings, and other inclusions into the casting during the pouring process. | Select a coating with good comprehensive performance, including high strength, high refractoriness, good thermal shock resistance, coating ability, suspension, and non-flowability. Standardize the boxing operation to ensure that the coating layer of the pattern group does not fall off, crack, or have cracks before pouring. Reasonably set the pouring pressure head, temperature, and time, and choose an appropriate pouring temperature and a pouring system with a suitable capacity to reduce the pouring height. Reasonably determine the negative pressure, and for steel castings, the appropriate negative pressure is generally between -0.030 and -0.045 MPa. Set up slag retaining, skimming, and slag collecting risers in the pouring system design. Adopt steel water purification technology to purify the molten steel from the whole process of smelting, overheating, deoxidation, until pouring into the mold. |
1.4 Backspray
During the pouring process, due to the excessive gas generated by the thermal decomposition of the gas mold and the inability to be discharged in time, the pressure in the casting cavity rises sharply, which easily causes flame or molten metal spray, resulting in the ζ₯εΊ of the casting. The preventive measures are:
(1) Control the density of the EPS pattern within 0.015 – 0.020 g/cm3, ensure the pattern is dry, and the coating is also dry to reduce the moisture content and gas generation amount.
(2) Select a coating with good permeability and adjust the coating thickness (appropriate within 1.0 – 2.0 mm) to facilitate the timely escape of the gas generated by the pattern pyrolysis.
(3) Control the permeability and particle size of the dry sand; the design of the sand box should be scientific, reasonable, and applicable. Control the negative pressure (vacuum pump suction) to ensure that the pattern gasifies under vacuum and hypoxia conditions with little combustion and reduced gas generation amount.
(4) Control the pouring temperature and pouring speed, use the heat of the molten steel to ensure the gasification of the pattern, and control the pouring speed when a large amount of gas is generated by the pattern to avoid too fast pouring speed, which can promote the burst of pyrolysis gas.
(5) Design a reasonable pouring system to ensure that the molten metal fills the mold smoothly, balancedly, and quickly, and the gas generated by the pattern pyrolysis escapes out of the mold and is sucked and discharged.
Casting Defect | Cause | Preventive Measure |
---|---|---|
Backspray | Excessive gas generated by the thermal decomposition of the gas mold and the inability to be discharged in time, causing a sharp rise in the pressure in the casting cavity. | Control the density and moisture content of the EPS pattern. Select a coating with good permeability and adjust the coating thickness. Control the permeability and particle size of the dry sand, and the negative pressure. Control the pouring temperature and pouring speed, and design a reasonable pouring system. |
1.5 Negative Pressure Cutting
The main reason: In the vacuum state of the sand box, due to the damage of the mold during the pouring process, the outside air is sucked into the mold; the strong airflow penetration process has a cutting force on the un-solidified molten metal, forming a cutting phenomenon, which we call the “negative pressure cutting” phenomenon. The main reasons for this phenomenon are:
The negative pressure during pouring is too high, the coating thickness is too thin or damaged, and the pressure holding time after pouring is too long. Determine the process parameters according to the factors such as the structure, size, and quality of different castings. Generally, the negative pressure in the sand box during pouring is at an appropriate negative pressure of -0.020 – -0.035 MPa, the coating thickness is ensured to be 1.0 – 2.0 mm, the pouring height of the ladle should be reduced as much as possible during pouring, and the nozzle of the ladle should be as close to the pouring cup as possible, and the pressure holding time after pouring is controlled within 3 – 7 minutes.
Casting Defect | Cause | Preventive Measure |
---|---|---|
Negative Pressure Cutting | Damage to the mold during pouring, causing outside air to be sucked into the mold, and the strong airflow has a cutting force on the un-solidified molten metal. | Control the negative pressure during pouring, ensure the coating thickness is appropriate, and avoid damage to the coating. Reduce the pouring height of the ladle and keep the nozzle close to the pouring cup. Control the pressure holding time after pouring within 3 – 7 minutes. |
2. Conclusion
Lost foam casting of steel castings has great development space in China’s lost foam casting industry. As long as effective production operation control methods are adopted for production operation control management, the melting process of the castings is strictly controlled, the process conditions for reducing and eliminating carbon increase during pouring are controlled, combined with the actual production conditions, the training of skilled technicians is strengthened, the overall level of the team is improved, and every process in the process is strictly controlled, completely qualified steel castings can be produced.