Common casting defects can occur during the casting process and can affect the quality and functionality of the final cast component. Identifying these defects and implementing prevention strategies is essential for ensuring high-quality castings. Here are some common casting defects, along with their identification and prevention strategies:
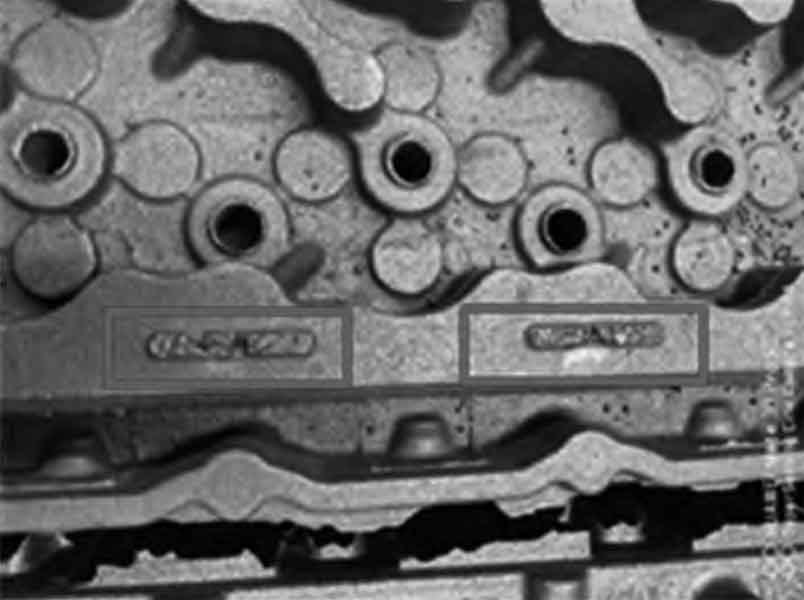
- Gas Porosity:
- Identification: Gas porosity appears as voids or gas bubbles within the casting. It can be either open (visible on the surface) or closed (internal).
- Prevention: Use proper gating and riser design to allow for proper venting and escape of gases. Maintain proper molten metal temperature and use suitable degassing techniques. Consider using mold coatings or additives to minimize gas absorption.
- Shrinkage:
- Identification: Shrinkage defects appear as cavities or voids in the casting caused by inadequate feeding of molten metal during solidification.
- Prevention: Ensure proper riser design and placement to provide a continuous supply of molten metal during solidification. Use chills or insulation materials strategically to control cooling rates and promote directional solidification.
- Cold shuts:
- Identification: Cold shuts occur when two or more molten metal streams do not fuse together properly, resulting in a visible line or seam on the casting surface.
- Prevention: Optimize gating and riser design to promote uniform filling and proper fusion of molten metal. Control pouring temperature and metal flow velocity to prevent premature solidification and ensure complete fusion.
- Misruns:
- Identification: Misruns happen when the molten metal fails to completely fill the mold cavity, resulting in an incomplete casting.
- Prevention: Design proper gating systems with adequate cross-sections and turbulence control. Ensure proper venting to avoid air entrapment. Optimize pouring parameters, such as temperature and speed, to facilitate complete filling.
- Inclusions:
- Identification: Inclusions are foreign materials, such as sand, slag, or oxides, that get trapped in the casting during pouring.
- Prevention: Use high-quality raw materials and control the quality of mold coatings and refractories. Implement effective filtering and gating systems to prevent the entry of foreign materials. Properly clean and prepare molds to minimize contamination.
- Sand-related defects (e.g., sand inclusions, sand burn-on):
- Identification: Sand-related defects can manifest as sand inclusions, rough surfaces, or burnt sand adhering to the casting surface.
- Prevention: Implement proper mold design and preparation techniques to minimize mold erosion and sand-related defects. Use appropriate mold coatings and release agents. Optimize pouring and cooling parameters to reduce the risk of sand burn-on.
- Surface defects (e.g., rough surfaces, cracks):
- Identification: Surface defects are visible imperfections on the casting surface, such as roughness, cracks, or surface tears.
- Prevention: Ensure proper mold surface finish and coating application. Optimize mold release agents and their application techniques. Control cooling rates to avoid thermal stresses and cracking.
- Dimensional inaccuracies:
- Identification: Dimensional inaccuracies can be identified by comparing the actual casting dimensions with the desired specifications.
- Prevention: Use accurate and well-maintained patterns, cores, and molds. Implement proper mold assembly techniques and control cooling rates to minimize dimensional variations. Regularly calibrate and maintain measuring instruments.
Regular inspection and monitoring of the casting process, along with continuous improvement initiatives, can help identify defects, analyze their root causes, and implement effective preventive measures. Collaborating closely with casting suppliers, conducting process audits, and investing in training programs for personnel involved in the casting process can also contribute to quality improvement.