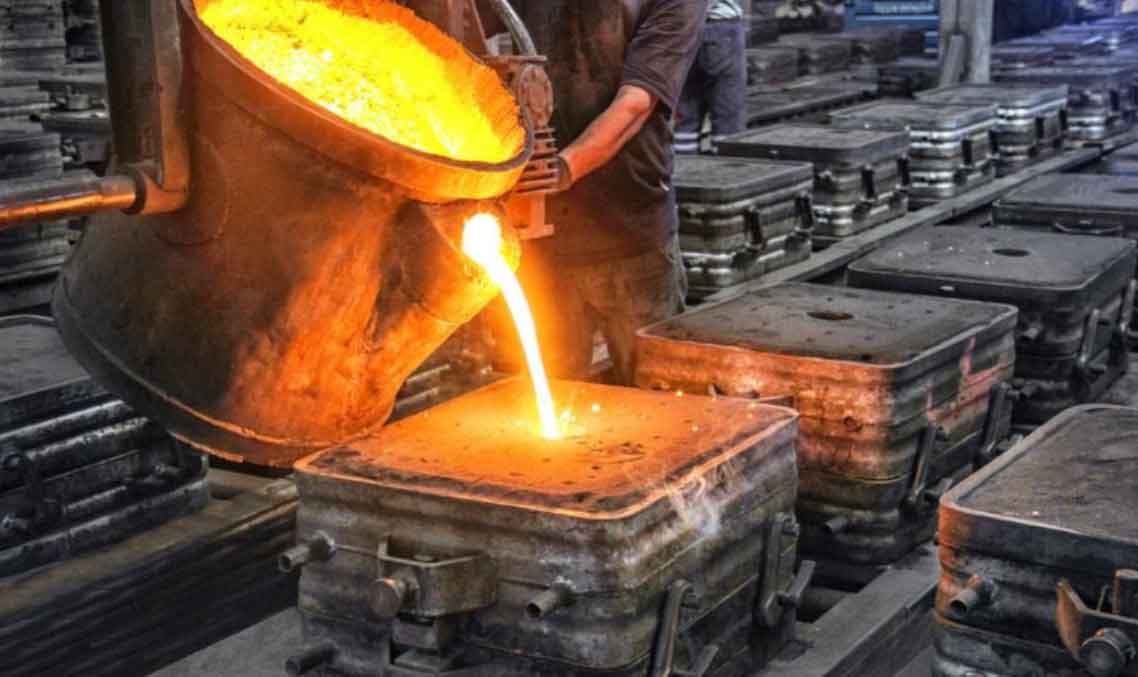
Sand casting manufacturing, like any other production process, can present its share of challenges. Overcoming these challenges requires a combination of expertise, process optimization, and a proactive approach. Here are some common challenges in sand casting manufacturing and how to overcome them:
1. Casting Defects:
- Defects like porosity, shrinkage, inclusions, and surface imperfections can occur during the casting process. To overcome this challenge, manufacturers should use advanced casting simulation software to optimize gating and risering designs. Regular inspection and testing during production help identify and rectify defects early.
2. Inconsistent Material Properties:
- Variations in material properties, such as mechanical strength, can lead to inconsistency in the final castings. Manufacturers must carefully control the melting and pouring processes, ensuring the metal is at the correct temperature and composition.
3. Dimensional Accuracy:
- Achieving precise dimensional accuracy in complex castings can be challenging. Manufacturers should use high-quality molds and patterns and implement stringent process controls to ensure dimensional stability.
4. Mold and Core Degradation:
- Sand molds and cores can degrade over time, leading to mold shift and defects. Using high-quality refractory materials, controlling moisture levels, and storing molds properly can help mitigate this issue.
5. Environmental Impact:
- Sand casting can generate waste sand and emissions, leading to environmental concerns. Implementing sustainable practices, recycling sand, and using energy-efficient equipment can reduce the environmental impact.
6. Labor Intensiveness:
- Sand casting can involve manual labor, which can be physically demanding and time-consuming. Automation and robotics can help alleviate this challenge, improving productivity and reducing the reliance on manual labor.
7. Lead Times:
- Traditional sand casting methods may have longer lead times due to mold preparation and cooling times. Adopting rapid prototyping technologies and streamlining processes can help reduce lead times.
8. Complex Geometries:
- Casting complex geometries can result in uneven material flow and defects. Proper mold design and gating system optimization, along with advanced casting simulation, can help tackle this challenge.
9. Tooling Costs:
- The initial investment in tooling and patterns can be significant. Manufacturers should work with customers to optimize designs, select cost-effective materials, and amortize tooling costs over the production volume.
10. Post-Casting Processing:
- Finishing and post-casting processes can add to the overall manufacturing time and costs. Using automation for cleaning, finishing, and machining can streamline these processes.
11. Material Availability:
- Availability and cost of specific materials can impact casting choices. Working with suppliers and exploring material alternatives can help overcome material availability challenges.
12. Quality Assurance and Traceability:
- Implementing robust quality control systems and establishing traceability for materials and processes are essential for ensuring consistent and high-quality castings.
By proactively addressing these challenges and continuously optimizing the sand casting process, manufacturers can improve product quality, efficiency, and customer satisfaction. Collaboration between foundries and customers can also lead to better designs and cost-effective solutions to overcome specific challenges unique to each project.