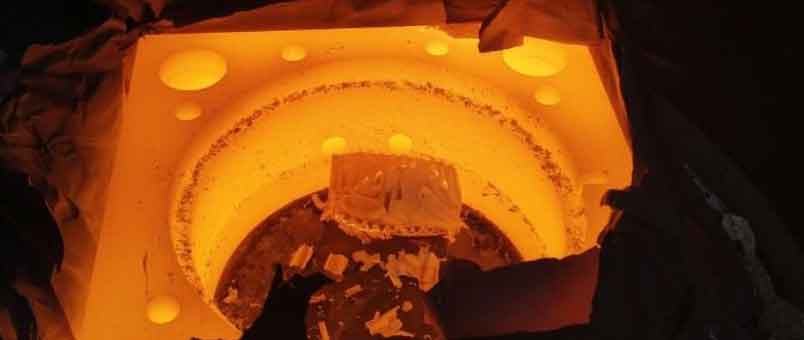
Heat treatment is a critical process used to alter the properties of metals and achieve desired material characteristics. However, heat treatment can also lead to various defects if not performed correctly. Understanding the causes, effects, and prevention strategies for common heat treatment defects is crucial for ensuring the quality and performance of heat-treated components. This article highlights some of the common heat treatment defects, their causes, effects, and preventive measures.
- Decarburization:
- Cause: Decarburization occurs when the carbon content at the surface of a metal component is reduced during the heat treatment process. It can be caused by inadequate furnace atmosphere control or excessive exposure to oxygen.
- Effects: Decarburization leads to a reduction in surface hardness, strength, and wear resistance of the component, negatively affecting its performance.
- Prevention: Use a controlled atmosphere or a protective coating to minimize exposure to oxygen during heat treatment. Optimize furnace atmosphere and temperature control to prevent excessive decarburization.
- Distortion:
- Cause: Distortion occurs due to non-uniform heating and cooling rates during the heat treatment process. Uneven temperature distribution, improper fixturing, or inadequate quenching methods can contribute to distortion.
- Effects: Distortion results in dimensional inaccuracies and can lead to improper fitment of components, affecting functionality and assembly.
- Prevention: Optimize fixturing and design to promote uniform heating and cooling. Employ appropriate quenching methods, such as controlled cooling rates or the use of quenching media, to minimize distortion. Consider stress-relieving techniques after heat treatment to alleviate residual stresses.
- Grain Growth:
- Cause: Grain growth is the enlargement of metal grains during heat treatment, typically due to prolonged exposure to high temperatures. It can occur when the material is heated above its critical temperature for an extended period or during improper cooling.
- Effects: Grain growth can result in reduced mechanical properties, such as strength and toughness, as well as decreased dimensional stability.
- Prevention: Control the heating and cooling rates to minimize the time spent at high temperatures. Employ suitable quenching methods, such as oil or water quenching, to rapidly cool the material and prevent excessive grain growth. Consider the use of grain growth inhibitors or alloying elements to control grain growth.
- Quench Cracking:
- Cause: Quench cracking occurs when rapid cooling during the quenching process induces high thermal stresses in the material. It is typically caused by improper quenching methods, inadequate material selection, or poor part design.
- Effects: Quench cracking leads to the formation of cracks, which can compromise the structural integrity and functionality of the component.
- Prevention: Select appropriate quenching media and methods based on the material and component geometry. Preheat the material to reduce temperature differentials during quenching. Consider the use of tempering or stress-relieving processes to relieve residual stresses that contribute to quench cracking.
- Surface Oxidation:
- Cause: Surface oxidation occurs when the material is exposed to oxygen or oxidizing atmospheres during heat treatment. It can be caused by inadequate atmosphere control, improper cleaning, or excessive exposure to air.
- Effects: Surface oxidation results in the formation of oxide layers, which can lead to poor surface finish, reduced corrosion resistance, and impaired mechanical properties.
- Prevention: Utilize controlled atmospheres, such as inert gases or reducing atmospheres, to minimize oxidation during heat treatment. Ensure thorough cleaning of the material surface before heat treatment to remove contaminants. Implement proper packaging and handling techniques to protect the material from exposure to air.
- Soft Spots:
- Cause: Soft spots are localized areas of reduced hardness or inadequate heat treatment. They can occur due to inconsistent heating or insufficient soaking time during the heat treatment process.
- Effects: Soft spots compromise the mechanical properties and performance of the component, leading to potential failure under load or wear conditions.
- Prevention: Ensure uniform heating and consistent soaking time throughout the material. Monitor and control the temperature within the specified range to achieve the desired hardness. Perform hardness testing and quality inspections to identify and rectify any soft spots.
Understanding the causes, effects, and prevention strategies for common heat treatment defects is essential for maintaining the quality and performance of heat-treated components. By implementing proper heat treatment techniques, optimizing process parameters, and ensuring adequate quality control measures, manufacturers can minimize defects and achieve desired material properties. Additionally, continuous monitoring, process improvement, and adherence to industry standards and best practices contribute to the overall quality and reliability of heat-treated components.