Operating as a leading steel castings manufacturer involves a series of processes and operations aimed at producing high-quality castings efficiently. Here’s an inside look at the typical operations of a steel castings manufacturer:
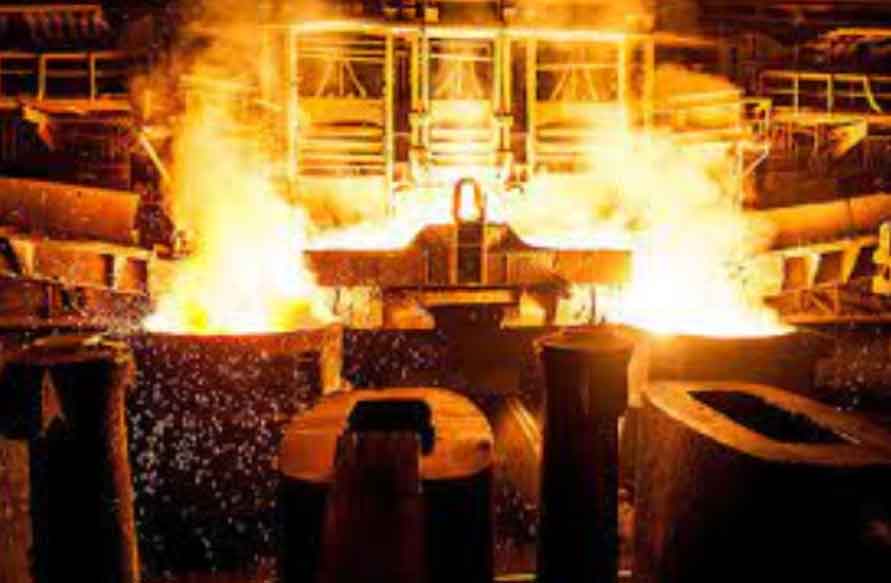
- Design and Engineering: The process starts with collaboration between the manufacturer and the customer to understand the requirements and specifications of the casting. The manufacturer’s design and engineering team uses advanced CAD software to create detailed 3D models of the casting, considering factors such as material selection, dimensional accuracy, and structural integrity.
- Pattern and Mold Making: Once the design is finalized, a pattern is created. Patterns are typically made from wood, plastic, or metal and replicate the shape of the desired casting. The pattern is used to create a mold by placing it in a casting flask and packing molding material, usually a mixture of sand and binders, around it. The mold is then hardened to form a cavity that matches the desired shape of the casting.
- Melting and Pouring: The next step is the melting of the selected metal or alloy. Furnaces, such as electric arc furnaces or induction furnaces, are used to melt the metal to its liquid state. The molten metal is then poured into the prepared mold using either gravity or vacuum-assisted pouring techniques. Care is taken to ensure proper temperature control, minimizing the risk of defects and ensuring metallurgical integrity.
- Solidification and Cooling: Once the molten metal is poured into the mold, it begins to solidify and take the shape of the cavity. Cooling rates and solidification control are critical to achieving the desired casting properties. Advanced cooling techniques, such as the use of chills or controlled cooling systems, may be employed to ensure uniform cooling and minimize the formation of internal stresses or defects.
- Shakeout and Cleaning: After the casting has cooled and solidified, the mold is removed by shaking or vibrating the flask, a process known as shakeout. The casting is then cleaned to remove any residual mold material, scale, or oxides. Various methods such as shot blasting, sandblasting, or chemical cleaning may be used depending on the requirements of the casting.
- Machining and Finishing: Once the casting is cleaned, it may undergo machining operations to achieve the final dimensions, tolerances, and surface finish. CNC machining centers or manual machining processes like milling, drilling, and turning are employed. Other finishing operations, such as grinding, polishing, or heat treatment, may also be performed to enhance the casting’s mechanical properties or surface aesthetics.
- Quality Assurance: Throughout the entire process, stringent quality control measures are implemented to ensure the casting meets the required specifications and standards. Non-destructive testing methods, such as X-ray or ultrasonic inspection, may be employed to detect any internal defects. Dimensional inspections, visual inspections, and mechanical testing are also conducted to ensure the casting’s quality and integrity.
- Packaging and Delivery: Once the casting has passed all quality checks, it is carefully packaged to protect it during transportation. The manufacturer coordinates with the customer to arrange for shipping and delivery, ensuring that the castings reach their destination safely and on time.
- Continuous Improvement and Innovation: Leading steel castings manufacturers prioritize continuous improvement and innovation in their operations. They invest in research and development to explore new materials, processes, and technologies that can enhance the quality, efficiency, and sustainability of their castings. They also maintain close relationships with customers, seeking feedback and incorporating it into their operations to better meet evolving industry demands.
By excelling in these operations, a leading steel castings manufacturer can deliver high-quality castings that meet customer requirements while maintaining efficiency and staying at the forefront of the industry.