Introduction
Blow bar is critical components in impact crushers, responsible for crushing the feed material by striking it with a high-speed impact. The efficiency and durability of a blow bar significantly impact the overall performance of a crusher. This article provides a comparative analysis of blow bar used in different crusher applications, focusing on the materials, design, wear resistance, and application suitability.
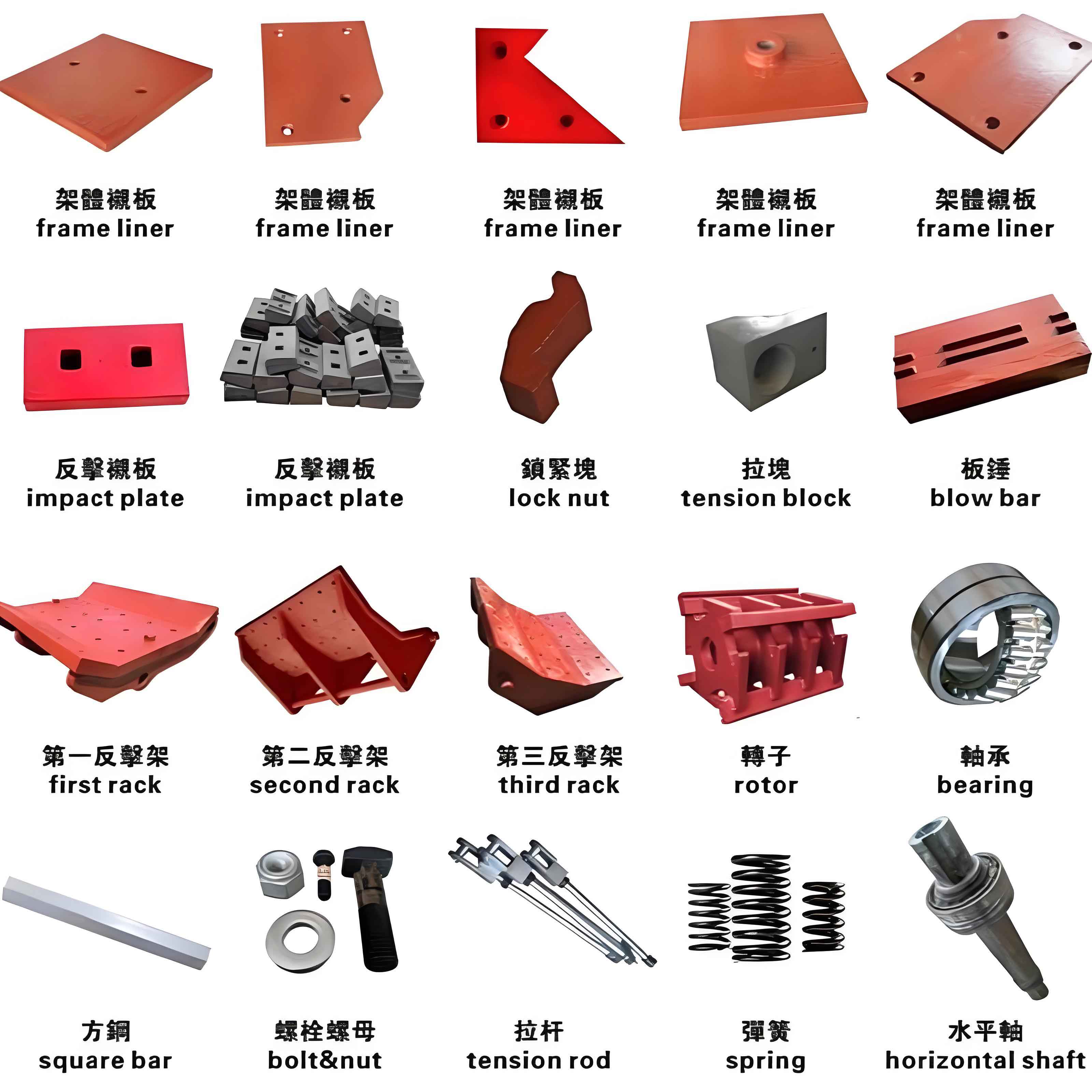
Materials Used in Blow Bar
Blow bar is manufactured from various materials, each offering distinct advantages and drawbacks. The choice of material affects the blow bar’s wear resistance, impact strength, and overall lifespan.
Common Materials for Blow Bar:
- High Manganese Steel (Mn):
- Characteristics: Excellent toughness and high wear resistance due to work hardening properties.
- Applications: Suitable for crushing abrasive materials such as granite, basalt, and quartz.
- Advantages: Long lifespan in high-impact applications.
- Disadvantages: Susceptible to rapid wear when crushing less abrasive materials.
- Martensitic Steel:
- Characteristics: Good wear resistance and impact strength, with moderate hardness.
- Applications: Ideal for recycling applications and crushing medium-hard materials like limestone.
- Advantages: Balanced wear resistance and impact toughness.
- Disadvantages: Not suitable for highly abrasive materials.
- Chrome Steel:
- Characteristics: High hardness and excellent wear resistance due to chromium content.
- Applications: Best for highly abrasive materials and high-impact applications.
- Advantages: Long-lasting in abrasive conditions.
- Disadvantages: Brittle and prone to breakage under high-impact stress.
- Ceramic Inserts:
- Characteristics: Ceramic inserts are embedded in a steel matrix to enhance wear resistance.
- Applications: Suitable for extremely abrasive applications like asphalt, concrete, and demolition debris.
- Advantages: Superior wear resistance and extended lifespan.
- Disadvantages: Higher cost and potential for breakage if not properly manufactured.
Material | Characteristics | Applications | Advantages | Disadvantages |
---|---|---|---|---|
High Manganese Steel | High toughness, work hardening | Abrasive materials (granite, basalt) | Long lifespan in high-impact applications | Rapid wear with less abrasive materials |
Martensitic Steel | Good wear resistance and impact strength | Medium-hard materials (limestone) | Balanced wear resistance and toughness | Not suitable for highly abrasive materials |
Chrome Steel | High hardness, excellent wear resistance | Highly abrasive materials | Long-lasting in abrasive conditions | Brittle, prone to breakage under high impact |
Ceramic Inserts | Superior wear resistance | Extremely abrasive applications | Extended lifespan | Higher cost, potential for breakage |
Design Considerations for Blow Bar
The design of blow bar affects their performance and suitability for various crusher applications. Key design aspects include:
Shape and Profile:
- Straight Blow Bar:
- Description: Flat and straight design.
- Advantages: Simple to manufacture and easy to replace.
- Disadvantages: Less effective at distributing impact forces, leading to uneven wear.
- Curved Blow Bar:
- Description: Curved profile to improve impact distribution.
- Advantages: Better distribution of impact forces, reducing uneven wear.
- Disadvantages: More complex to manufacture and replace.
- Wing-Tip Blow Bar:
- Description: Extended tips to enhance material penetration.
- Advantages: Improved material penetration and crushing efficiency.
- Disadvantages: Higher wear at the tips, requiring more frequent replacement.
Reinforcement:
- Solid Blow Bar:
- Description: Solid construction for maximum strength.
- Advantages: High durability and resistance to breakage.
- Disadvantages: Heavier and may cause increased stress on the crusher.
- Composite Blow Bar:
- Description: Combination of materials for enhanced performance.
- Advantages: Optimized wear resistance and impact strength.
- Disadvantages: Higher manufacturing cost and complexity.
Design Aspect | Description | Advantages | Disadvantages |
---|---|---|---|
Straight Blow Bar | Flat and straight design | Simple to manufacture, easy to replace | Less effective at distributing impact forces, uneven wear |
Curved Blow Bar | Curved profile | Better impact force distribution | Complex to manufacture and replace |
Wing-Tip Blow Bar | Extended tips | Improved material penetration, efficiency | Higher wear at tips, more frequent replacement |
Solid Blow Bar | Solid construction | High durability, resistance to breakage | Heavier, increased stress on crusher |
Composite Blow Bar | Combination of materials | Optimized wear resistance, impact strength | Higher cost, manufacturing complexity |
Application Suitability
The suitability of a blow bar for a specific application depends on various factors, including the type of material being crushed, the desired product size, and the operational conditions of the crusher.
Application Examples:
- Granite Crushing:
- Recommended Material: High Manganese Steel.
- Design Consideration: Curved or wing-tip blow bar to enhance impact distribution and penetration.
- Limestone Crushing:
- Recommended Material: Martensitic Steel.
- Design Consideration: Straight blow bar for easy replacement and moderate wear resistance.
- Asphalt and Concrete Recycling:
- Recommended Material: Ceramic Inserts.
- Design Consideration: Composite blow bar for superior wear resistance and extended lifespan.
- Demolition Debris:
- Recommended Material: Chrome Steel.
- Design Consideration: Reinforced or solid blow bar to withstand high-impact forces.
Application | Recommended Material | Design Consideration |
---|---|---|
Granite Crushing | High Manganese Steel | Curved or wing-tip blow bar for impact distribution |
Limestone Crushing | Martensitic Steel | Straight blow bar for easy replacement |
Asphalt and Concrete Recycling | Ceramic Inserts | Composite blow bar for superior wear resistance |
Demolition Debris | Chrome Steel | Reinforced or solid blow bar for high-impact resistance |
Conclusion
Blow bar is essential components in impact crushers, and their material composition and design significantly influence their performance and durability. By understanding the characteristics of different materials such as high manganese steel, martensitic steel, chrome steel, and ceramic inserts, and considering design aspects like shape, profile, and reinforcement, operators can select the most suitable blow bar for their specific crusher applications. This ensures optimal crusher performance, extended lifespan of the blow bar, and efficient material processing, ultimately enhancing productivity and reducing operational costs.