Spheroidal graphite iron castings are widely used in engineering applications due to its superior mechanical properties, including high strength, ductility, and wear resistance. The microstructure of spheroidal graphite iron castings plays crucial role in determining these properties, and it can be significantly influenced by the cooling rate during the casting process. This article provides a comprehensive comparative analysis of the microstructural evolution in spheroidal graphite iron castings under various cooling rates. Detailed tables and lists are included to enhance understanding.
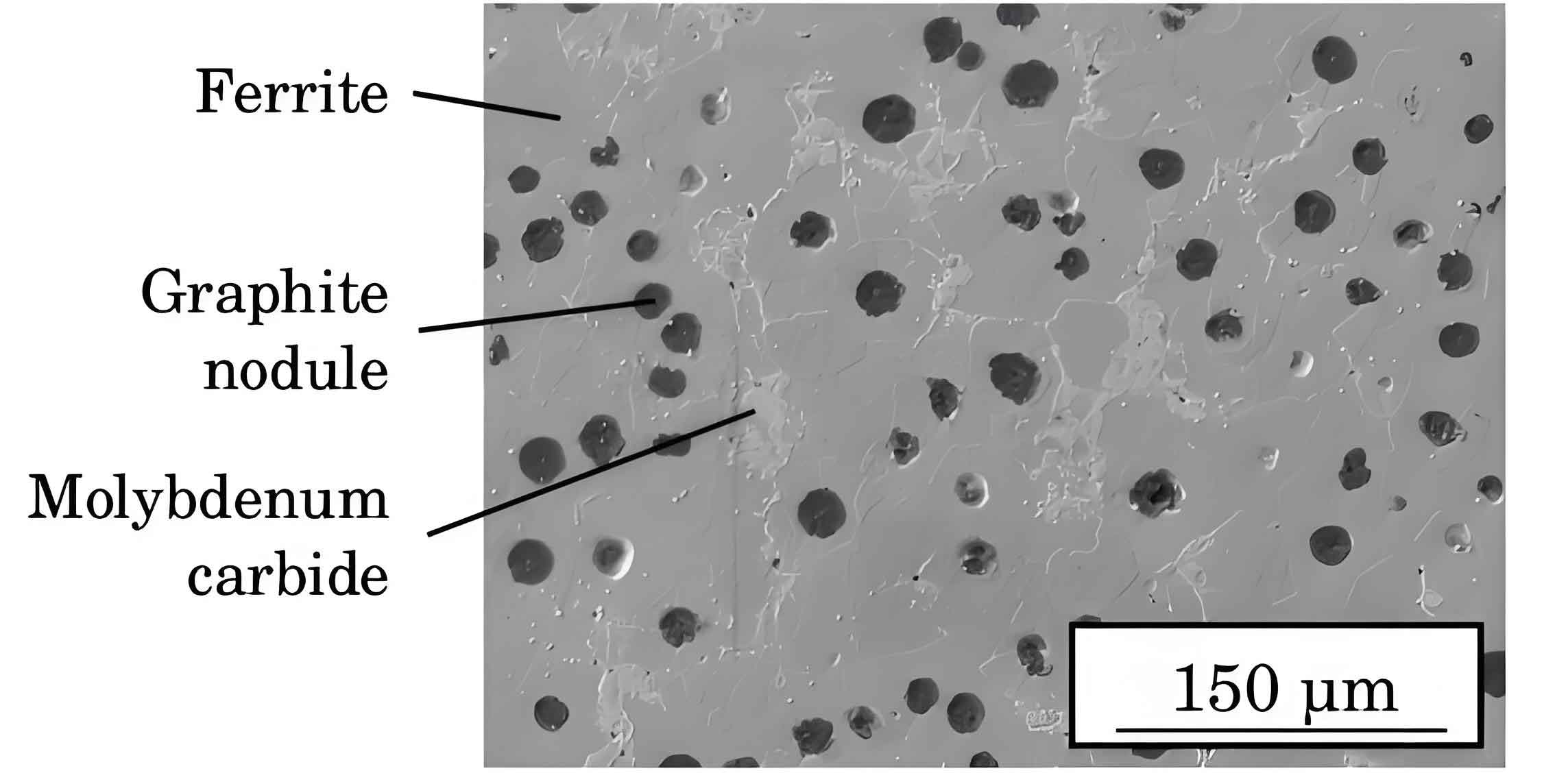
Introduction
The cooling rate during the solidification of spheroidal graphite iron castings affects the formation and distribution of graphite nodules and the matrix structure, which in turn influence the mechanical properties of the final product. Understanding these microstructural changes is essential for optimizing casting processes and achieving desired material properties. This article explores the effects of different cooling rates on the microstructure of spheroidal graphite iron castings and their implications for engineering applications.
Microstructural Components of Spheroidal Graphite Iron Castings
The microstructure of spheroidal graphite iron castings typically consists of:
- Graphite Nodules: Spheroidal graphite particles that enhance ductility and toughness.
- Ferrite: Soft, ductile matrix phase surrounding the graphite nodules.
- Pearlite: Hard, lamellar structure that provides strength and wear resistance.
- Carbides: Hard particles that can form under certain conditions, affecting hardness and wear resistance.
Effect of Cooling Rates on Microstructure
- Slow Cooling Rate:
- Graphite Nodules: Larger, well-formed nodules with fewer but larger nodules per unit area.
- Matrix: Predominantly ferritic structure with some pearlite.
- Implications: Enhanced ductility and toughness but lower strength and hardness.
- Moderate Cooling Rate:
- Graphite Nodules: Uniformly distributed nodules with moderate size.
- Matrix: Balanced mixture of ferrite and pearlite.
- Implications: Balanced mechanical properties, combining good strength, ductility, and wear resistance.
- Rapid Cooling Rate:
- Graphite Nodules: Smaller, more numerous nodules per unit area.
- Matrix: Predominantly pearlitic with possible formation of carbides.
- Implications: Increased strength and hardness but reduced ductility and toughness.
Table: Microstructural Evolution Under Various Cooling Rates
Cooling Rate | Graphite Nodules | Matrix Composition | Mechanical Implications |
---|---|---|---|
Slow | Larger, fewer nodules | Predominantly ferritic | High ductility and toughness, lower strength |
Moderate | Uniformly distributed, moderate size | Balanced ferrite and pearlite | Balanced strength, ductility, and wear resistance |
Rapid | Smaller, more numerous nodules | Predominantly pearlitic, possible carbides | High strength and hardness, reduced ductility and toughness |
Comparative Analysis of Mechanical Properties
- Strength and Hardness:
- Slow Cooling: Lower strength and hardness due to a higher proportion of ferrite.
- Moderate Cooling: Balanced strength and hardness with a mix of ferrite and pearlite.
- Rapid Cooling: High strength and hardness due to a predominantly pearlitic matrix and potential carbide formation.
- Ductility and Toughness:
- Slow Cooling: High ductility and toughness from a ferritic matrix.
- Moderate Cooling: Good balance of ductility and toughness.
- Rapid Cooling: Reduced ductility and toughness due to a higher proportion of pearlite and carbides.
Table: Mechanical Properties Under Various Cooling Rates
Cooling Rate | Strength | Hardness | Ductility | Toughness |
---|---|---|---|---|
Slow | Lower | Lower | Higher | Higher |
Moderate | Balanced | Balanced | Balanced | Balanced |
Rapid | Higher | Higher | Lower | Lower |
Practical Applications Based on Cooling Rates
- Slow Cooling:
- Applications: Components requiring high ductility and toughness, such as automotive suspension parts, pipe fittings, and machinery frames.
- Example: Suspension control arms that need to withstand significant deformation without breaking.
- Moderate Cooling:
- Applications: General-purpose components requiring balanced mechanical properties, such as engine blocks, gears, and housings.
- Example: Engine blocks that require a balance of strength, ductility, and wear resistance.
- Rapid Cooling:
- Applications: Components requiring high strength and hardness, such as cutting tools, wear-resistant parts, and high-stress mechanical components.
- Example: Gear teeth that need high hardness to resist wear in high-stress applications.
Table: Applications Based on Cooling Rates
Cooling Rate | Applications | Examples |
---|---|---|
Slow | High ductility and toughness components | Automotive suspension parts, pipe fittings, machinery frames |
Moderate | General-purpose components | Engine blocks, gears, housings |
Rapid | High strength and hardness components | Cutting tools, wear-resistant parts, high-stress components |
Future Trends in Spheroidal Graphite Iron Castings and Cooling Rate Control
- Advanced Cooling Techniques:
- Controlled Cooling: Using computer-controlled cooling systems to precisely manage cooling rates and achieve desired microstructures.
- Cryogenic Cooling: Implementing cryogenic techniques to rapidly cool castings and enhance hardness and wear resistance.
- Simulation and Modeling:
- Predictive Modeling: Using advanced simulation software to predict microstructural evolution and optimize cooling processes.
- AI and Machine Learning: Applying AI and machine learning algorithms to analyze cooling data and improve process control.
- Sustainable Practices:
- Energy Efficiency: Developing energy-efficient cooling systems to reduce environmental impact and production costs.
- Recycling and Reusability: Enhancing recycling processes to reuse castings and reduce waste.
List: Future Trends in Spheroidal Graphite Iron Castings
- Advanced Cooling Techniques:
- Controlled cooling systems
- Cryogenic cooling
- Simulation and Modeling:
- Predictive modeling
- AI and machine learning
- Sustainable Practices:
- Energy-efficient cooling
- Recycling and reusability
Conclusion
The cooling rate during the solidification of spheroidal graphite iron castings has a profound impact on the resulting microstructure and mechanical properties. By understanding and controlling cooling rates, manufacturers can tailor the properties of spheroidal graphite iron castings to meet specific application requirements. As technology advances, new cooling techniques, simulation models, and sustainable practices will further enhance the ability to produce high-performance spheroidal graphite iron castings for a wide range of engineering applications.