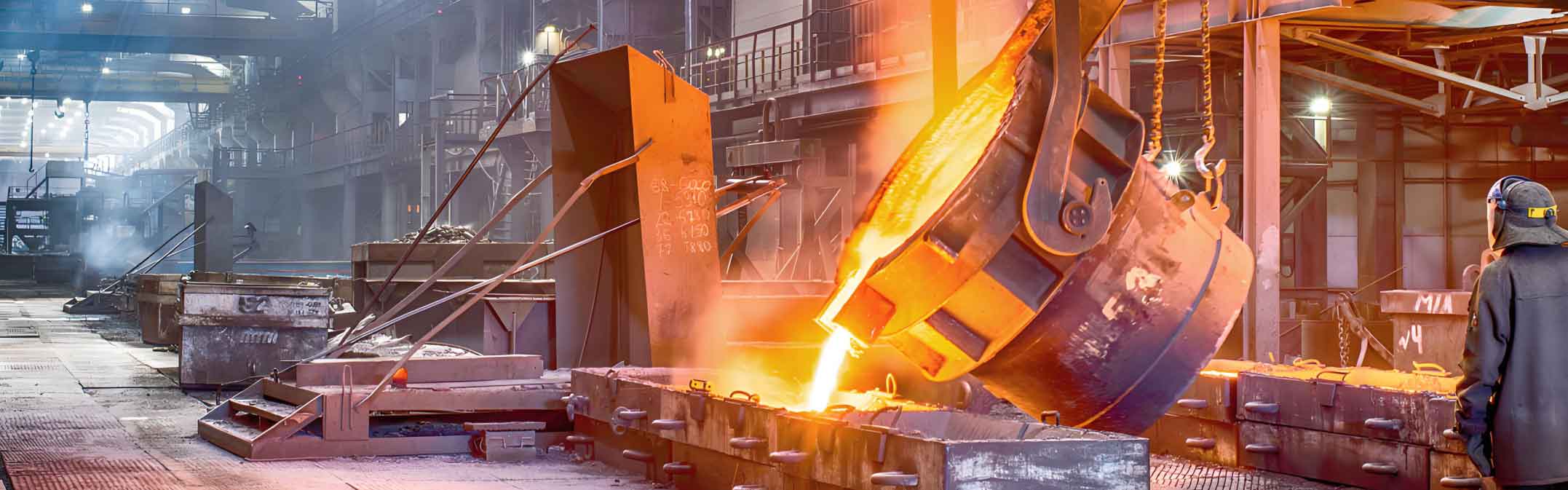
Sand casting and investment casting are two prominent metal casting processes used in the manufacturing industry. Each method has its unique advantages and disadvantages, making them suitable for different applications. This article provides a comprehensive comparative analysis of sand casting and investment casting, highlighting their pros and cons to help in selecting the most appropriate method for specific needs.
Overview of Sand Casting
Sand casting is a versatile casting process where sand is used as the mold material. It is one of the oldest and most widely used casting methods due to its simplicity and cost-effectiveness. The process involves creating a mold cavity in sand, pouring molten metal into the cavity, and allowing it to solidify.
Pros of Sand Casting
- Cost-Effectiveness
- Sand casting is generally more economical, especially for producing large and heavy components. The materials and equipment required for sand casting are relatively inexpensive.
- Flexibility in Size and Weight
- Sand casting can accommodate a wide range of sizes and weights. It is particularly suitable for producing large and heavy parts that would be challenging with other casting methods.
- Material Versatility
- Sand casting can be used with almost any metal, including ferrous and non-ferrous alloys. This versatility makes it applicable for various industries.
- Short Lead Times
- The setup and production times for sand casting are typically shorter, making it ideal for producing prototypes and short production runs.
Cons of Sand Casting
- Surface Finish
- The surface finish of sand cast components is generally rougher compared to those produced by other casting methods. Additional machining or finishing may be required.
- Dimensional Accuracy
- Sand casting has lower dimensional accuracy and consistency. This can result in the need for secondary operations to achieve precise dimensions.
- Complexity of Design
- While sand casting can produce complex shapes, it is less suited for very intricate or thin-walled designs compared to other methods.
Overview of Investment Casting
Investment casting, also known as lost-wax casting, involves creating a wax pattern, which is then coated with a refractory ceramic material to form a mold. The wax is melted out, and molten metal is poured into the cavity to create the final product. Investment casting is known for its ability to produce high-precision components with excellent surface finish.
Pros of Investment Casting
- High Precision and Accuracy
- Investment casting provides excellent dimensional accuracy and intricate detail. This makes it ideal for producing complex and finely detailed components.
- Superior Surface Finish
- The surface finish of investment cast parts is typically smooth and requires minimal post-processing. This can reduce the need for additional machining.
- Design Flexibility
- Investment casting allows for greater design flexibility, including the ability to cast thin-walled and complex geometries that are difficult to achieve with other methods.
- Material Efficiency
- The process results in minimal material waste, as precise amounts of metal are used, and the molds can be made to exact specifications.
Cons of Investment Casting
- Higher Costs
- Investment casting is generally more expensive due to the complexity of the mold-making process and the cost of materials, particularly for large production runs.
- Longer Lead Times
- The process involves multiple steps, including creating wax patterns and ceramic molds, which can result in longer lead times compared to sand casting.
- Size Limitations
- Investment casting is typically limited to smaller and medium-sized parts. Producing very large components can be challenging and cost-prohibitive.
Comparative Analysis
Table 1: Comparison of Sand Casting and Investment Casting
Aspect | Sand Casting | Investment Casting |
---|---|---|
Cost | Generally lower | Higher, especially for large runs |
Dimensional Accuracy | Moderate | High |
Surface Finish | Rough | Smooth |
Complexity of Design | Moderate complexity | High complexity |
Lead Time | Shorter | Longer |
Size and Weight Capacity | Large and heavy parts | Smaller to medium parts |
Material Versatility | Wide range of metals | Wide range of metals |
Production Volume | Suitable for low to medium volumes | Suitable for low to medium volumes |
Detailed Pros and Cons List
Sand Casting
Pros:
- Cost-Effectiveness:
- Lower material and setup costs.
- Flexibility in Size and Weight:
- Suitable for large and heavy components.
- Material Versatility:
- Applicable to various metals.
- Short Lead Times:
- Quick setup and production.
Cons:
- Surface Finish:
- Rough finish requiring post-processing.
- Dimensional Accuracy:
- Lower precision.
- Complexity of Design:
- Less suited for intricate designs.
Investment Casting
Pros:
- High Precision and Accuracy:
- Excellent detail and accuracy.
- Superior Surface Finish:
- Smooth finish, reducing post-processing.
- Design Flexibility:
- Suitable for complex and thin-walled parts.
- Material Efficiency:
- Minimal waste and precise material usage.
Cons:
- Higher Costs:
- Expensive materials and processes.
- Longer Lead Times:
- Multiple steps involved, increasing time.
- Size Limitations:
- Best for smaller to medium parts.
Conclusion
Both sand casting and investment casting offer unique advantages and face specific challenges. Sand casting stands out for its cost-effectiveness, flexibility in handling large parts, and shorter lead times, making it ideal for a variety of applications, particularly in producing large components with moderate precision requirements. Conversely, investment casting excels in providing high precision, excellent surface finish, and the ability to create complex and detailed parts, making it suitable for high-precision applications where quality and detail are paramount.
The choice between sand casting and investment casting ultimately depends on the specific requirements of the project, including the size and complexity of the parts, the desired surface finish, the required dimensional accuracy, and budget constraints. Understanding the pros and cons of each method allows manufacturers to select the most appropriate casting process to meet their needs, ensuring the production of high-quality components efficiently and cost-effectively.