Steel casting is a versatile manufacturing process used to produce components with complex geometries and high dimensional accuracy. Among the various techniques available, investment casting and sand casting stand out due to their unique benefits and applications. This article provides a comparative analysis of these two prominent steel casting techniques, highlighting their processes, advantages, disadvantages, and typical applications.
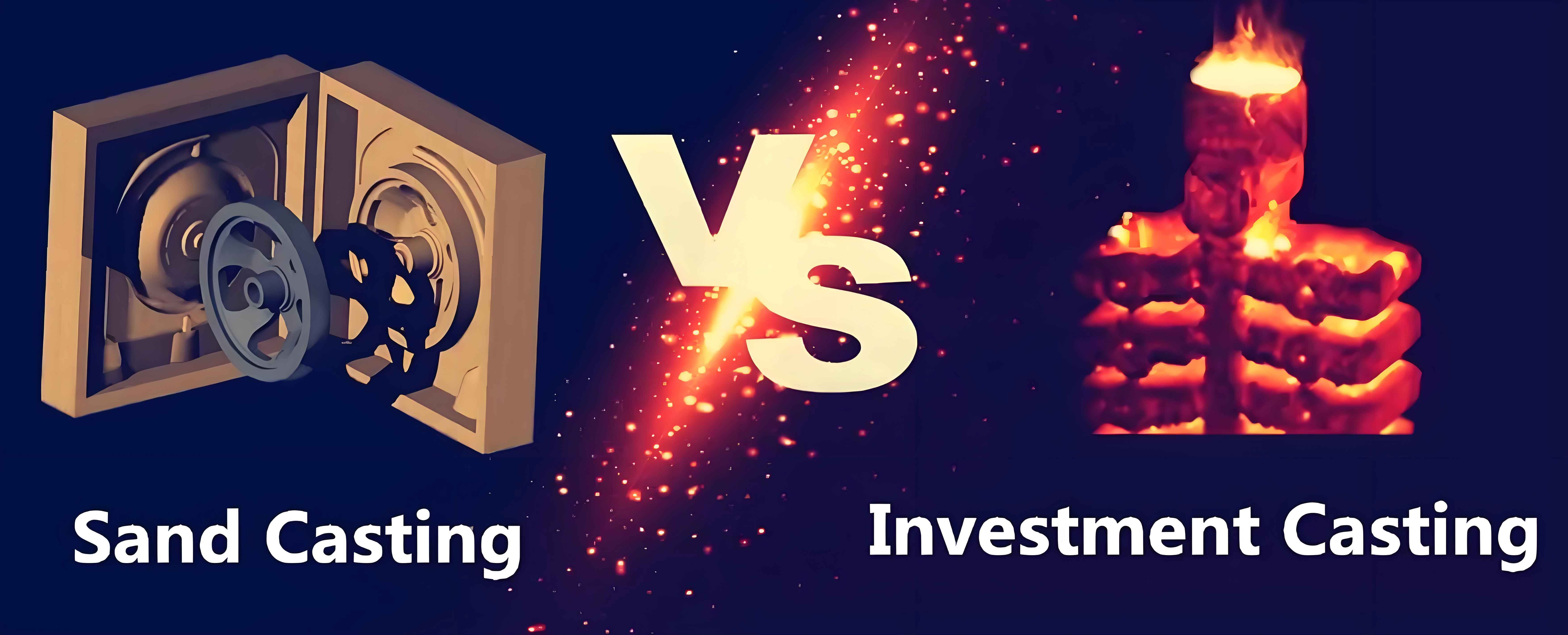
1. Overview of Steel Casting Techniques
Investment Casting: Investment casting, also known as precision casting or lost-wax casting, involves creating a wax pattern, which is a replica of the final product. This pattern is coated with a refractory ceramic material to form a mold. Once the ceramic material hardens, the wax is melted out, leaving a cavity in the shape of the component. Molten steel is then poured into this cavity. After the steel solidifies, the ceramic shell is broken away, revealing the final casting.
Sand Casting: Sand casting involves forming a mold from a sand mixture and pouring molten steel into this mold. The sand provides a mold that can withstand the high temperatures of molten steel. After the steel cools and solidifies, the sand mold is broken apart to remove the casting. This process is highly adaptable and can be used to cast large parts.
2. Process Comparison
Feature | Investment Casting | Sand Casting |
---|---|---|
Mold Creation | Uses a wax model covered with ceramic material. | Uses sand mixed with a binder to form the mold around a pattern. |
Material Wastage | Lower due to the precision of the wax model. | Higher due to the sand mold’s coarser nature. |
Surface Finish | Excellent surface finish, reducing the need for post-processing. | Rougher surface finish, often requiring additional finishing. |
Dimensional Accuracy | High dimensional accuracy and tight tolerances. | Generally good, but less precise than investment casting. |
Production Rate | Slower due to the complexity of mold preparation. | Faster, suitable for large batch production. |
Cost | Higher due to labor-intensive processes and materials used. | Lower, making it cost-effective for larger parts. |
Scalability | Best suited for small to medium-sized parts. | Can accommodate very large parts. |
3. Advantages and Disadvantages
Investment Casting Advantages:
- Produces parts with complex geometries and intricate details.
- High dimensional accuracy and excellent surface finish.
- Allows for the casting of high melting point metals without significant surface defects.
Investment Casting Disadvantages:
- Higher cost due to materials and process complexity.
- Longer production cycles.
- Limitations on part size due to mold handling.
Sand Casting Advantages:
- Economical for large parts and small production runs.
- Flexible mold and core making, adapting easily to complex shapes.
- High melting temperatures are not a limitation for the mold materials.
Sand Casting Disadvantages:
- Rough surface finish that may require extensive finishing work.
- Lower dimensional accuracy compared to investment casting.
- Potential for defects such as sand inclusion or gas porosity.
4. Applications
Investment Casting Applications:
- Aerospace components where precision and weight are critical.
- Medical implants requiring biocompatibility and complex shapes.
- Automotive parts for specific applications where tight tolerances are necessary.
Sand Casting Applications:
- Large industrial machinery components like housings and large gears.
- Automotive engine blocks and manifolds.
- Artistic sculptures and historical restorations where size and cost are considerations.
5. Conclusion
Choosing between investment casting and sand casting depends on several factors, including the complexity of the design, the required precision, production volume, and cost considerations. Investment casting is ideal for parts requiring high accuracy and a smooth surface, while sand casting is more suitable for larger, less complex components. By understanding the distinct characteristics of each method, manufacturers can select the most appropriate steel casting technique for their specific needs, optimizing both production efficiency and product quality.