After adding riser and chill to the gating system, mesh division, casting parameters setting and pouring process simulation calculation are carried out again by ProCAST simulation software, and viewer in ProCAST software is used to simulate the pouring process The module can check and analyze the casting defects, and get the schematic diagram of the solidification defects of the axle housing after optimization of the scheme I closed gating system and scheme three semi closed gating system, as shown in the figure.
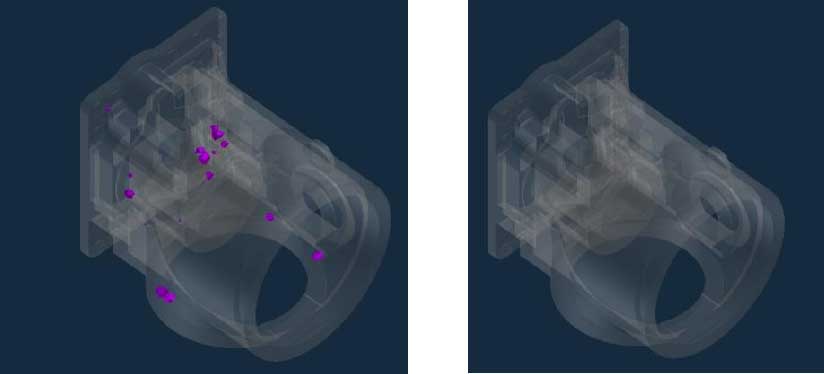
As shown in the figure, the shrinkage porosity and shrinkage cavity defects of the axle housing in the optimized scheme 1 are reduced, but they are not completely eliminated. There are large shrinkage porosity and shrinkage cavity defects in the cylinder cavity near the numerical flange. The casting defects of the third scheme axle housing have disappeared, the original shrinkage porosity and shrinkage cavity have been transferred to the riser, and the shrinkage porosity at the hot spot is almost eliminated. This shows that the riser and chill have played a good role in feeding and chilling the axle housing respectively, so as to eliminate the solidification defects of the axle housing. The casting effect of the optimized scheme three semi closed gating system can be seen from the optimization results It is better than the closed gating system of casting scheme one.