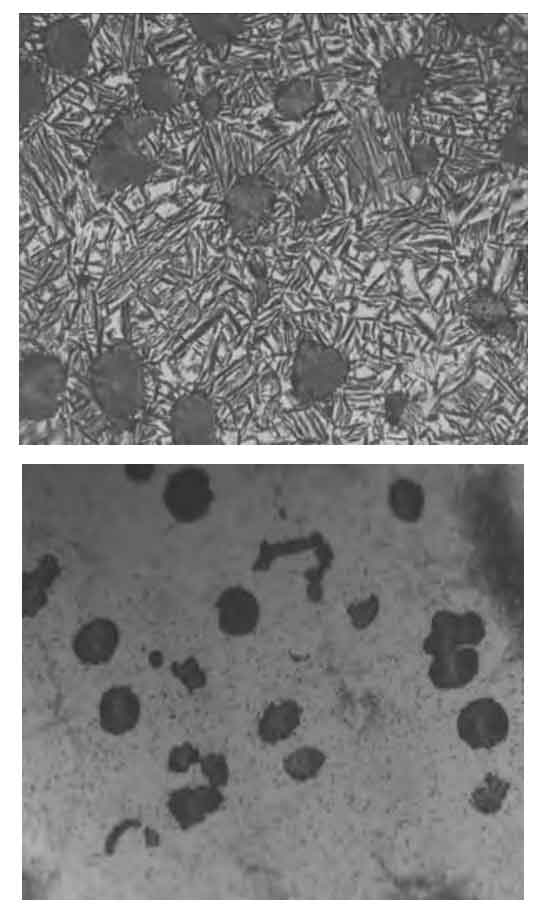
After friction welding of existing 38MnVS6Ti non quenched and tempered steel and 42CrMo4 quenched and tempered steel pistons, if only stress relief annealing treatment is carried out, the hardness of the heat affected zone of the weld seam after annealing will be higher, that is, the hardness of the heat affected zone of the weld seam is 430-500HV1, while the hardness of the non welding area is 250-300HV1, which will lead to the removal of welding flash by semi finishing Intermittent cutting occurs in the finishing flash area, which causes rapid tool cutting or tool wear, and further increases the machining cost. Therefore, the Company further increases the quenching+tempering or isothermal quenching processes after the friction welding annealing treatment, thus eliminating the hardness difference between the welding heat affected zone (weld area) and the non weld area, keeping the hardness of the weld area and the non weld area consistent, and effectively reducing the processing and production costs.
Isothermal quenching parameters | Austenitizing parameters | Isothermal quenching parameters |
Temperature/Time | 890°Cx60min | 450°Cx25min |
Isothermal quenching treatment is preferred. After isothermal quenching, the structure is uniform and the strength is higher. Isothermal quenching molten salt can be austenitized in a high temperature salt bath furnace with the composition of 60% BaCl+40% NaCl, and then rapidly quenched into a low temperature salt bath furnace with the composition of 50% NaNO2+50% KNO3 for isothermal quenching. See Table 1 for specific heat treatment scheme, The structure of nodular cast iron piston after isothermal quenching is shown on the left; Or oil quenching at 920 ℃ for 60 minutes and tempering at 450 ℃ for 3 hours. The structure after quenching and tempering is as shown on the right. For nodular cast iron piston, the oil inlet and outlet holes shall be processed after isothermal quenching or quenching+tempering, otherwise, residual impurities in the cooling oil passage of the nodular cast iron piston and oxidation of the oil passage will be caused;
38MnVS6Ti non modulating steel piston | New Type of Isothermally Quenched Ductile Iron Piston | New type quenched+tempered ductile iron piston | |
Brinell hardness/HBW | 250-300 | 250-300 | 250-300 |
Yield strength/MPa | ≥520 | ≥550 | ≥550 |
Tensile strength/MPa | ≥850 | ≥850 | ≥800 |
Elongation after fracture/% | ≥10 | ≥8 | ≥10 |
Machinability | Difference | Very nice | Very nice |
Material price/yuan/kg | 17 | 10 | 9 |
QT600-7 nodular cast iron, as the material for manufacturing split piston, can reduce the material cost and machining cost of nodular cast iron piston. If the quenching+tempering or isothermal quenching process is added, although a small amount of heat treatment cost will be increased, the strength and cutting performance of nodular cast iron can be further improved, which can greatly reduce the material cost, It can also greatly reduce the machining cost. Table 2 shows the specific comparison between 38MnVS6Ti non quenched and tempered steel piston and QT600-7 isothermal quenched, quenched and tempered nodular cast iron piston in terms of mechanical properties, machinability and price.