Resin sand casting is a casting process renowned for its ability to unleash complexity and create intricate metal shapes with exceptional precision. This casting method empowers designers and engineers to push the boundaries of design, offering opportunities to fabricate metal components with intricate details, complex geometries, and unique features. Let’s explore how resin sand casting achieves this complexity:
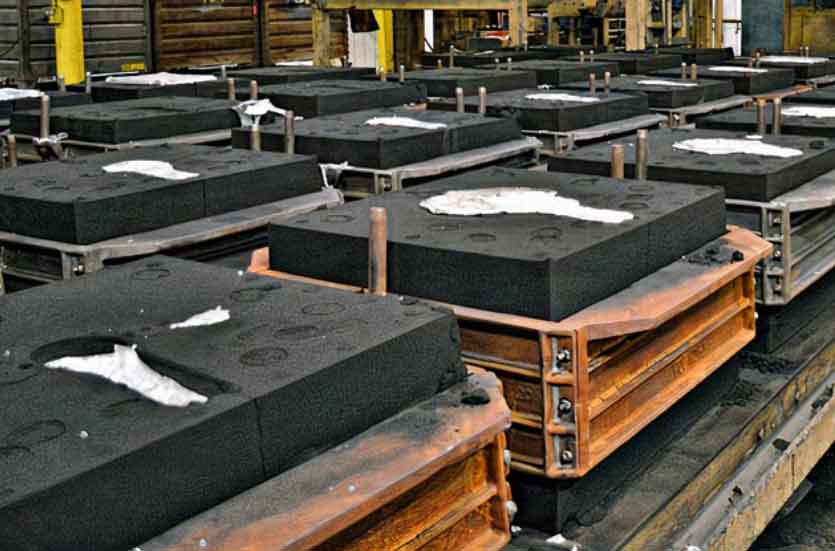
1. Intricate Patterns:
The process begins with the creation of intricate patterns, which are replicas of the desired metal components. Skilled pattern makers or advanced 3D printing technologies can produce highly detailed and complex patterns with fine features and delicate shapes.
2. Expendable Patterns:
Resin sand casting employs expendable patterns, allowing for greater design freedom. These patterns can be made from a variety of materials, including wood, plastic, or metal. This flexibility enables designers to experiment with different patterns, making it easier to optimize the final design.
3. Pattern Reproduction:
The patterns are used to create the mold cavity in the sand. The patterns are removed from the mold, leaving behind a detailed impression of their shape and features. This results in molds that can faithfully reproduce even the most intricate design elements.
4. Core-Making Capability:
Resin sand casting allows the incorporation of cores into the mold. Cores are used to create internal features of the metal component that cannot be achieved by using the pattern alone. These cores can be made of sand or other materials that withstand the heat of the molten metal.
5. Complex Gating System:
The gating system in resin sand casting is designed to control the flow of molten metal into the mold cavity. Engineers can design complex gating systems with multiple channels and sprues to ensure uniform filling of intricate geometries without causing turbulence or defects.
6. High Dimensional Accuracy:
The use of resin-coated sand and precise molding techniques contribute to high dimensional accuracy in the final metal components. This is crucial, especially for parts that require tight tolerances and perfect fitment.
7. Thin-Walled Sections and Filigree Details:
Resin sand casting’s adaptability allows for the creation of metal components with varying thicknesses, from thicker structural sections to delicate and intricate filigree details. This makes it suitable for applications where lightweight and intricate designs are required.
8. Reduced Draft Angles:
Compared to traditional sand casting, resin sand casting allows for reduced draft angles on the patterns. This means that the metal components can have near-vertical walls or even undercut features without being overly constrained by draft requirements.
9. Material Compatibility:
Resin sand casting is compatible with various metals and alloys, including ferrous and non-ferrous materials. This flexibility allows designers to choose the most suitable material for each specific application, whether it be for strength, weight, or other properties.
10. Integration with Additive Manufacturing:
The integration of additive manufacturing, such as 3D printing, with resin sand casting has expanded design possibilities. 3D-printed patterns and cores can be used, allowing for even more intricate and unique metal components.
Resin sand casting’s ability to unleash complexity and fabricate intricate metal shapes makes it a powerful tool in the hands of designers and engineers. It enables the realization of innovative and visually stunning components, driving advancements in industries such as aerospace, automotive, art, and architecture.