The coating raw material lost foam casting coating is composed of refractory, binder, carrier, suspending agent and special additives such as surfactant, defoamer, preservative, etc. Although the paint formula is ever-changing, it needs good process performance, working performance, quality stability and application reproducibility.
Refractory: it has the functions of heat insulation, sand resistance and reducing the surface roughness of lost foam castings. It should have the characteristics of high fire resistance, fine particles and no reaction with high-temperature molten alloy. The selection of refractory materials is mainly based on the type of alloy, the structural shape and wall thickness of lost foam castings. The commonly used refractory materials include corundum powder, zircon powder, quartz powder, bauxite, etc.
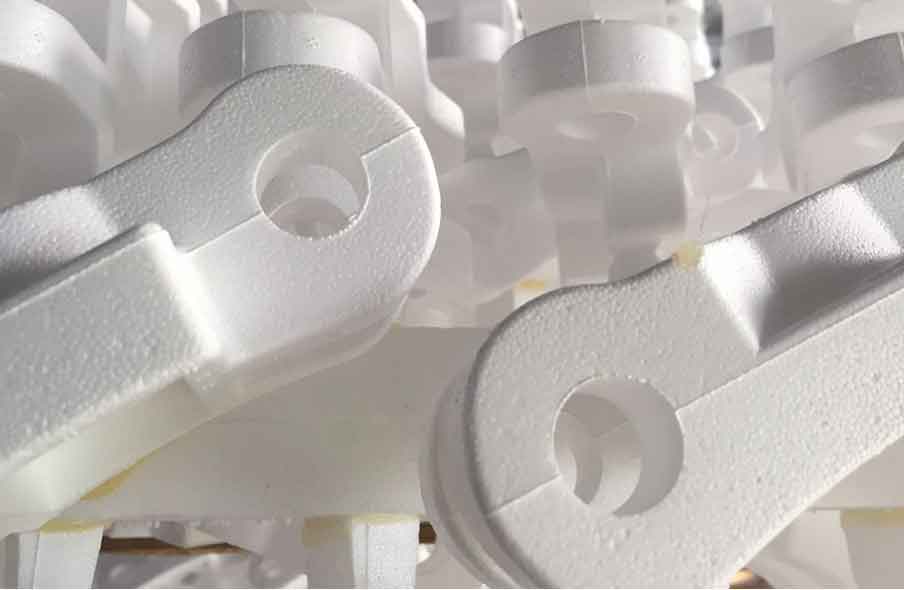
Binder: in addition to giving the coating layer strength and coating performance, and improving the suspension, the binder should enable the lost foam casting coating to overcome the hydrophobic effect of the pattern surface, so that the los coating layer can firmly adhere to the pattern surface without falling off, is not easy to oxidize in the air, and does not react with the pattern. It can be divided into low-temperature and high-temperature binders. Commonly used low-temperature binders include syrup, dextrin, pulp, phenolic resin, polyvinyl alcohol, polyvinyl acetate, light methyl cellulose, polyvinyl butyral, etc. High temperature binders mainly include silica sol, clay, water glass, phosphate, bentonite, etc. In order to make lost foam casting coating have good bonding performance, a certain proportion of binder should be used together.
Carrier: the commonly used carriers are water and ethanol. Compared with ethanol, water is low-cost, non-toxic, rich in sources, and the water-based coating has good suspension and thixotropy, which is also easy to adjust. It is often widely used as the carrier of lost foam casting coating, but the water-based coating dries slowly, has poor wettability to the pattern, and the coating is not easy to hang.
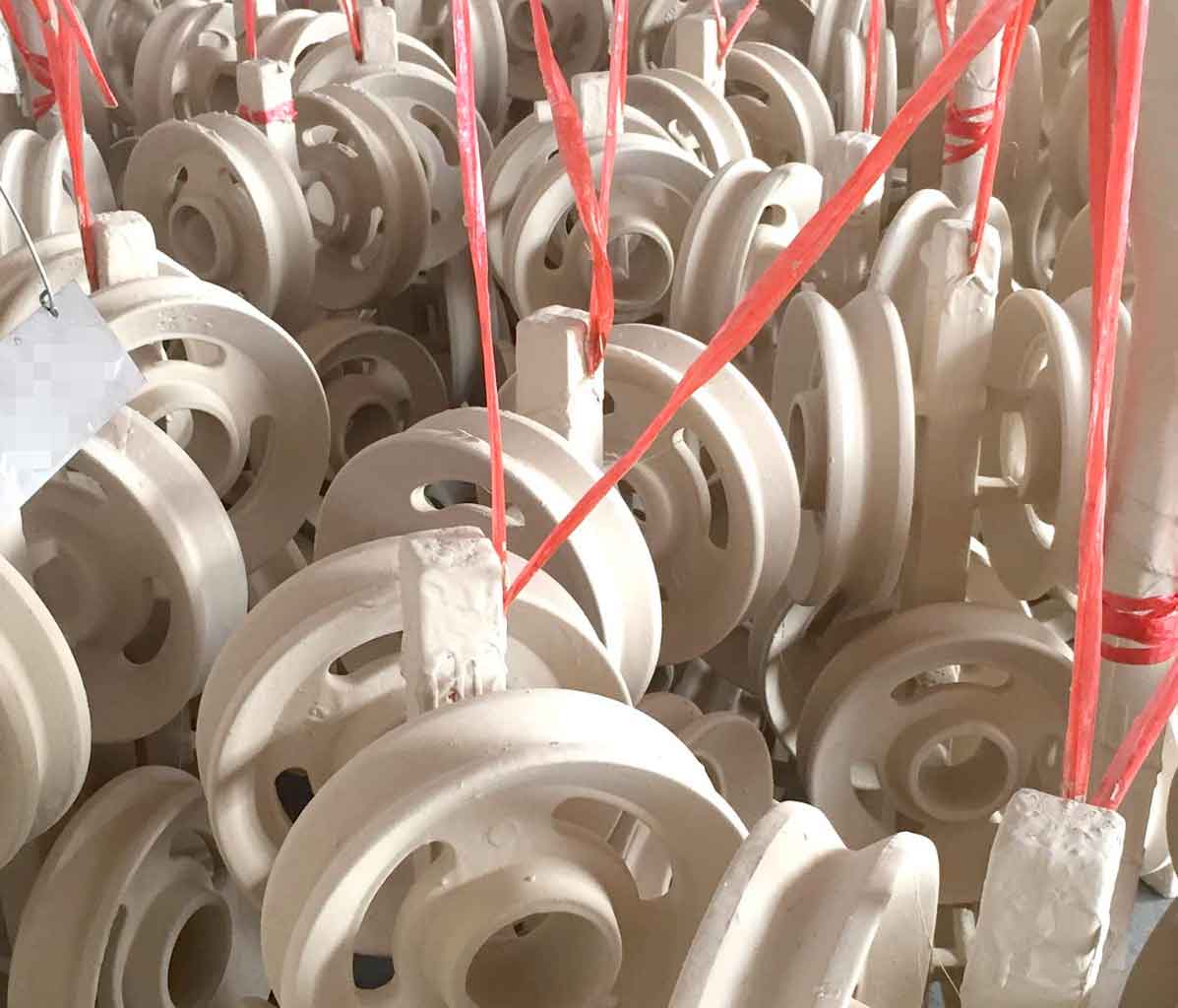
Suspending agent: improve the coating performance of lost foam casting coating, so that lost foam casting coating has good thixotropy, and an appropriate coating can be obtained by one dip coating. Commonly used suspension agents include bentonite, methyl cellulose, polyvinyl acetal, etc.
Additives: additives added to improve the performance of lost foam casting coatings in some aspects, commonly used surfactants, defoamers, preservatives, rheological accelerators, etc. Adding surfactant into lost foam casting coating can reduce the interfacial tension between lost foam casting coating and pattern, overcome the hydrophobicity of pattern, and make it easy to coat. Commonly used are. Defoamer is used to eliminate tiny bubbles in lost foam casting coating, make the coating surface in contact with the pattern bright and clean, and improve the surface roughness of castings.