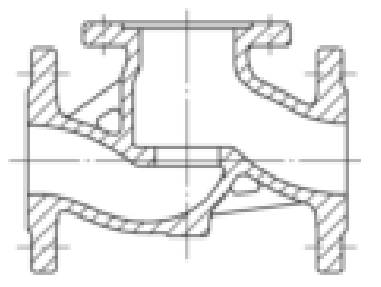
According to the current standard API 623-2013 “steel globe valves – Flanged and butt welded ends, bolted bonnet”, bs1873-1975 “steel globe valves and stop check valves with flanged and butt welded ends for petroleum, petrochemical and related industries”, and GB / T In the standard 12235-2007 “steel globe valves and lift check valves for petroleum, petrochemical and related industries”, the typical structure of the valve body in the stop valve diagram is waist drum shape. The valve body (see Figure) is very rare. If there is no special requirement, waist drum body should be used in the new design of globe valve.
On the one hand, casting dimensional tolerance can be used as the basis of material cost control, on the other hand, it can be used as design basis to accurately calculate product weight and cost budget. The tolerance control capability of a foundry can be determined by comparing several groups of precision machined drawing dimensions with the actual casting blank surveying and mapping dimensions, and then comparing these groups of contrast dimensions to the tolerance level of GB / T 6414-2017 “casting dimensional tolerances, geometric tolerances and machining allowance”, so as to determine the tolerance control ability of the foundry.
After adding some local features, a set of basic die can meet the needs of various valve structures, such as different flange end sealing surface, different valve relief boss, independent valve seat and body valve seat. Multi configuration mold can effectively save the cost of enterprise management.