In theory, the whole process can be summarized into three important stages: primary shrinkage (liquid shrinkage), volumetric expansion (graphitization expansion) and secondary shrinkage (solid shrinkage). These three important stages have different volume trends, as shown in Figure 1.
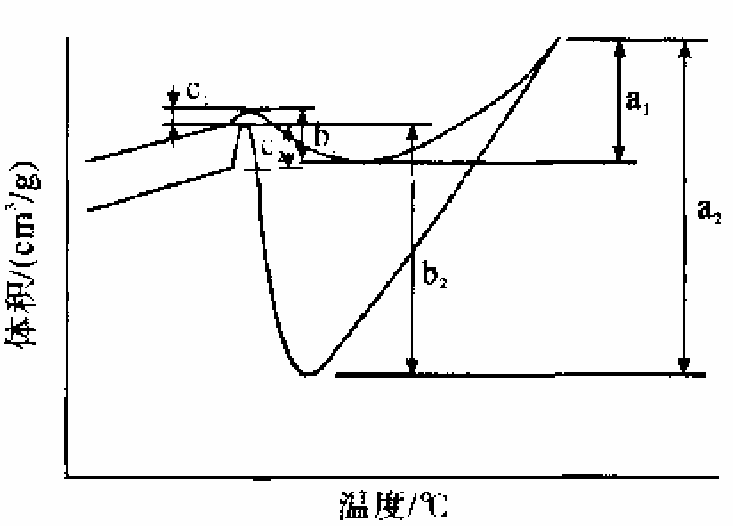
In Figure 1, A1 and A2 represent the primary contraction stage, B1 and B2 represent the volume expansion stage respectively, and C1 and C2 represent the secondary contraction stage respectively. The study also shows that the volume change curves are different according to the cooling rate of the mold and the metallurgical quality of the molten iron. The a1-b1-c1 curve in Figure 1 is the volume change curve with slow cooling rate and good metallurgical quality, and the curve a2-b2-c2 is the volume change curve with fast cooling rate and poor metallurgical quality. The results show that the metallurgical quality and cooling rate have great influence on the primary shrinkage, which is one of the important factors affecting the shrinkage and porosity tendency. In the actual production, in order to effectively reduce the influence of these objective factors in the operation, and ensure the compactness and quality stability of the casting body from the process plan, it is particularly important to realize the balanced solidification through the process measures.
The volume shrinkage of nodular cast iron is larger when it is cooled in the mold. At the same time, the volume expansion is caused by the precipitation of eutectoid transformation graphite, so the partial expansion and shrinkage cancel each other theoretically. In the actual production research, according to the actual structure and service conditions of castings, some positions can be set as relatively limited sequence solidification, making full use of the solidification characteristics of dynamic superposition of shrinkage and expansion to realize the solidification technology scheme of dense casting structure. The key point of balanced solidification technology is to realize the solidification of shrinkage and shrinkage, shrinkage and expansion in a preset sequence and proportion through effective technological measures.
The study of proportional solidification technology is of universal significance for eliminating the shrinkage cavity and porosity of complex hot spot ductile iron castings and producing high quality castings.