The control system of vacuum differential pressure casting is one of the key factors to ensure the quality of castings, especially thin-walled castings. The early control system is mostly manual control, the control operation is not stable, and the casting quality is difficult to guarantee. In the past 20 years, some automatic pressure regulating control systems have been developed. Dong Xiuqi et al. [7] used the double valve push-pull type P regulation to control the liquid surface pressurization process of differential pressure casting, which solved the problems of large inertia and serious lag of the system in this control. This method can not only simplify the regulating process and reduce the cost, but also greatly improve the control accuracy. Yao Xifan et al. [8] simulated the self-adjusting control of differential pressure casting parameters. The results show that compared with the conventional PID control, the self-adjusting control of parameters has faster response and smaller overshoot.
Although the research of self-adjusting control system has made great progress, with the improvement of preparation requirements, it is expected to get faster response speed and improve control accuracy. It is expected that PID control and fuzzy control are combined. For example, Hao Qitang et al. [9] adopt the combination of fuzzy control and PID control, and use digital combination valve to effectively improve the pressure control accuracy. The pressure control error is less than 0.3kpa, The large complex thin-walled castings were successfully fabricated by this technology. In recent years, with the accumulation of researchers’ research experience and data on the control system of vacuum differential pressure casting equipment, the artificial intelligence control system has been effectively developed. The artificial intelligence control system mainly uses the operation experience and data, professional theory and reasoning ability, as well as the performance and state of the control system and other related information to control, so as to minimize the impact of the mathematical model of the controlled object.
Yu Huan et al. Developed a set of intelligent control system of vacuum differential pressure casting, with a single-chip microcomputer as the core. The control scheme adopts a parameter self-tuning fuzzy control algorithm, i.e. proportional factor self-tuning fuzzy control. The structure of the control system is shown in the figure. The proportional factor self-tuning fuzzy control system is composed of a fuzzy controller, a performance measurement link, a proportional factor correction link and a closed-loop system connected with the controlled object. In real-time operation, the output y of the system is sampled, and the given performance index value is calculated by deviation e = r-y. Then the scale factors K1, K2 and K3 are modified according to the optimization method, and then the given performance index is calculated according to the deviation of the system, and K1, K2 and K3 are continuously modified according to the direction of getting smaller and smaller performance index, until the performance index is small enough to meet the given threshold. At this time, the obtained proportion factor is the optimal proportion factor, which makes the fuzzy control system have good quality and characteristics.
Later, according to the existing problems of vacuum differential pressure casting thin-walled parts, a parameter adaptive intelligent control system is developed to realize the classification of filling process and the pressure change of solidification process (A and B in the figure). The system adjusts the traditional five processes of vacuumizing, filling, boosting, pressure maintaining and pressure relief into a multi-stage process to meet the needs of classification filling and classification pressurized solidification.
The grading of filling stage of vacuum differential pressure casting is carried out according to the structural characteristics of the casting, and different pressurization modes are selected under different conditions. The details can be carried out in the following three ways (see Figure):
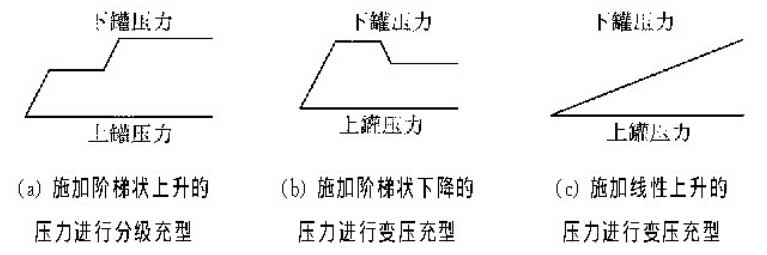
(1) First vacuumize the upper and lower tanks at the same time. When the vacuum degree reaches the preset value of 0, stop vacuumizing and keep the pressure value of the upper tank unchanged. Slowly apply the stepped up pressure to the lower tank for staged filling. See figure a for the process curve;
(2) After vacuumizing, keep the pressure value of the upper tank unchanged, and apply the step-by-step downward pressure to the lower tank for variable pressure filling. See Figure B for the process curve;
(3) After vacuumizing, keep the pressure value of the upper tank unchanged, and continuously apply the linearly rising pressure to the lower tank for variable pressure filling. See Figure C for the process curve.
It is also necessary to fully consider the structural characteristics of the castings in the process of staged solidification in vacuum differential pressure casting. As the solidification process of the casting goes on, the feeding channel reduces, the required feeding pressure increases, and the solidification pressure increases in the solidification stage of vacuum differential pressure casting. There are three ways to pressurize (see Figure):
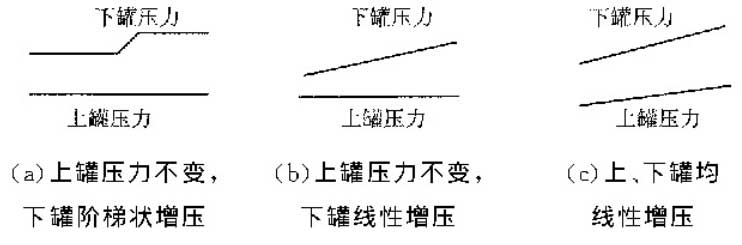
(1) The pressure of the upper tank and the lower tank shall be fixed first, and a certain pressure difference shall be maintained, then the pressure of the upper tank shall be fixed, and the pressure of the lower tank shall be increased step by step, and the pressure shall be maintained for a certain time until the casting is completely solidified, as shown in Fig. a;
(2) When the upper tank pressure is not changed, the lower tank pressure increases linearly, so that the differential pressure rises slowly until the casting is completely solidified, as shown in Figure B;
(3) The pressure uniformity of the upper tank and the lower tank increases, but the pressurization rate of the upper tank is slow, the pressurization rate of the lower tank is fast, and the pressure difference between the upper tank and the lower tank gradually increases until the casting is completely solidified, as shown in Figure C.