With the development of technology and the change of production and life style, the foundry industry must also consider the sustainable development. In the future, the development of foundry industry will show the characteristics of “variety diversity, complexity of cast-in-place structure, fast renewal”, etc. in terms of product demand. In terms of foundry production, it requires high quality, reliability, high efficiency, intelligence, green and low carbon, which requires the foundry industry to maintain advanced technology and means. 3D printing will have great potential in various new foundry processes and open up new manufacturing approaches.
Taking the casting of automobile engine block as an example, its development trend is to lighten the overall weight under the condition of output power and environmental protection. Therefore, aluminum alloy and thin-walled vermicular iron are the best choice of engine block in the future. There are two processes that deserve attention, and are where 3D printing can be used.
1) Replacing clay sand with core technology
Corepak is a core package made directly by core shooter or a complete sand package or sand mold made by auxiliary self hardening sand process, as shown in the figure.
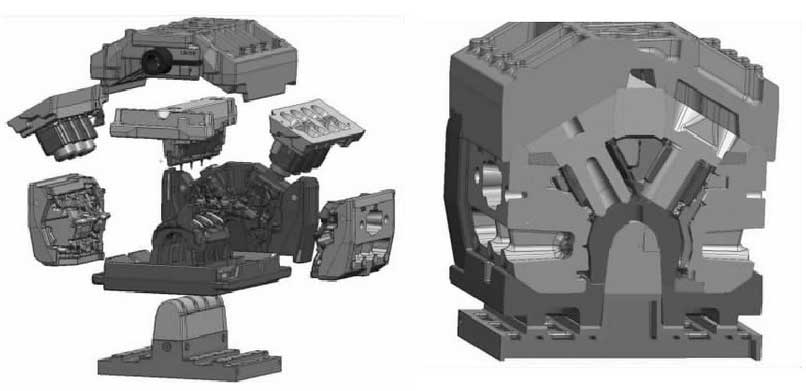
In 1986, the core technology was established in crossworth, England, casting the aluminum alloy V6 cylinder block of sports car, and in 2011, casting the engine cylinder block of vermicular iron. Nimak has the largest aluminum foundry in the world in dellingen, Germany. It produces cylinder block and cylinder head of engine with core technology. The annual output of cylinder block is more than 3 million pieces. In general use in the United States, Mazda foundry in Nanjing is also using core technology to produce aluminum cylinder block. Chongqing Electromechanical is building the world’s largest core technology production line in Chongqing, casting and start-up of cast iron cylinder block.
Compared with the tidal molding sand technology, the core technology can reduce equipment investment by 30%, material saving by 40%, energy saving by 40%, manpower saving by 10%, and product flexibility by 15%. In addition, there are important points:
It’s easy to realize automation, such as robot’s adding core and handling, and easy to realize environmental protection and friendly working environment;
Sanding, core removal and sand regeneration are completed in one flow table bed, which has outstanding energy conservation and environmental protection;
3D printing core making can be combined in a large amount and completed small batch casting economically.
2) Low pressure sand mold pouring process
Most of the above core assembly processes are gravity casting. If it is a complex casting, it can be combined with low-pressure casting, so as to overcome some difficulties of casting forming and obtain better mechanical properties, especially aluminum alloy is very easy to achieve.
In 2012, FAW Foundry Co., Ltd. non ferrous foundry built a low-pressure casting core assembly line to produce red flag series aluminum alloy V6 and I4 cylinder block (as shown in the figure). After the core package is combined, it is directly grasped by a robot to the low-pressure casting furnace for casting, and then put it on the cooling line for cooling, which can realize 4-min casting type 1.
Both core assembly and low-pressure casting are new technologies developed to meet the needs of casting development in the future. 3D printing core is very suitable for such automatic, accurate and complex casting production, and combining with it will create a more cost-effective production mode.
In the long run, according to the characteristics of the “third industrial revolution”, the foundry industry will follow this great technological trend in the future: energy saving, environmental protection and green casting; personalized consumption brings personalized design; small batch and single piece production become the mainstream; socialized production makes small foundry become a hot spot. Therefore, we can imagine the “personal foundry” brought by 3D printing technology: a 3D printer plus an electric furnace, which receives orders through the network cloud platform, the printer performs molding and core making, the electric furnace melts and pours, the molding sand is collected and recycled by socialization, and a personalized personal foundry is born! 3D printing will bring revolutionary changes to the foundry industry to be expected.
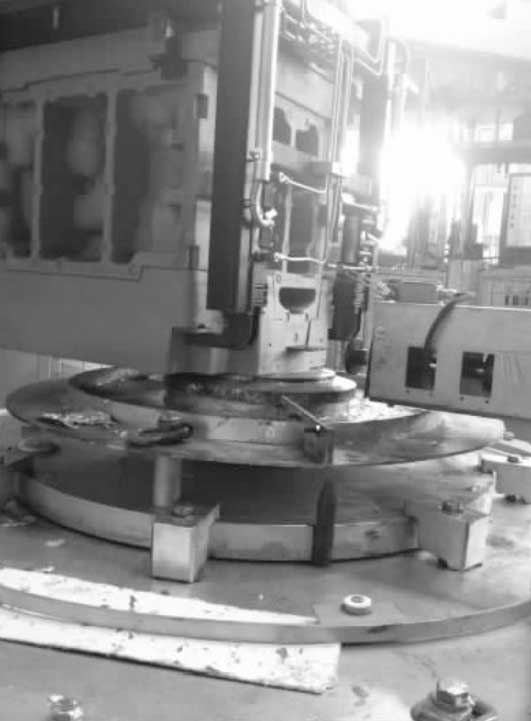