Corrosion protection for grey cast iron is crucial to enhance its durability and longevity. Grey cast iron is susceptible to various forms of corrosion, including general corrosion, pitting corrosion, and intergranular corrosion. Here are some strategies and methods that can be employed to protect grey cast iron from corrosion:
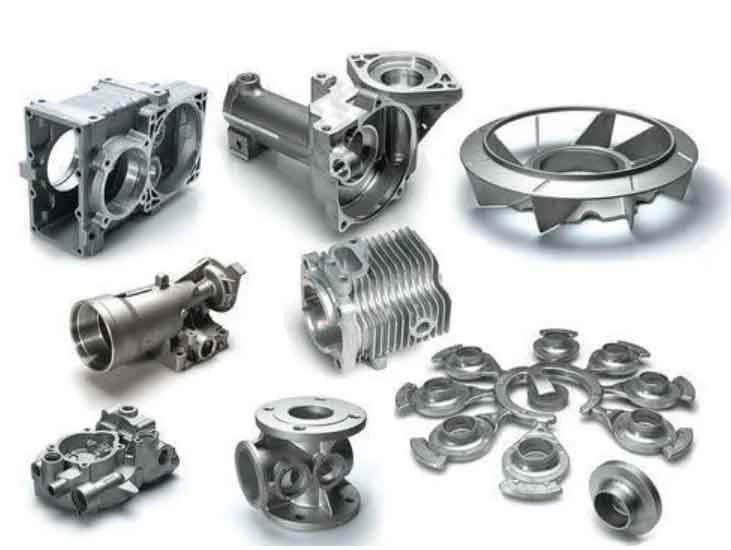
- Barrier Coatings: Applying barrier coatings such as paints, epoxy, or polymer coatings can provide a protective barrier between the cast iron surface and the corrosive environment. These coatings act as a physical barrier, preventing direct contact between the metal and corrosive agents.
- Cathodic Protection: Cathodic protection involves making the grey cast iron the cathode in a galvanic cell, which protects the iron from corrosion. This can be achieved by connecting the cast iron to a sacrificial anode, such as zinc or aluminum, or by using impressed current systems to provide a protective current.
- Alloying: Adding alloying elements to the grey cast iron can improve its corrosion resistance. For example, the addition of chromium or nickel can enhance the material’s ability to resist corrosion. Alloying elements form a protective oxide layer on the surface, which acts as a barrier against corrosive substances.
- Surface Treatment: Various surface treatment methods can be employed to improve the corrosion resistance of grey cast iron. These methods include processes such as shot peening, sandblasting, or grinding to remove surface impurities and create a clean, roughened surface that promotes better adhesion of protective coatings.
- Organic Coatings: Applying organic coatings, such as epoxy or polyurethane paints, can provide an effective barrier against corrosion. These coatings form a protective film on the surface of the cast iron, preventing direct contact with corrosive agents.
- Cathodic Protection: Cathodic protection involves making the grey cast iron the cathode in a galvanic cell, which protects the iron from corrosion. This can be achieved by connecting the cast iron to a sacrificial anode, such as zinc or aluminum, or by using impressed current systems to provide a protective current.
- Environmental Controls: Controlling the environment in which grey cast iron is exposed can also help prevent corrosion. For example, keeping the iron away from moisture, corrosive chemicals, or high humidity can significantly reduce the corrosion rate.
- Proper Maintenance: Regular inspection, cleaning, and maintenance of grey cast iron components are essential for preventing corrosion. Promptly addressing any signs of corrosion or damage, such as applying touch-up coatings or repairing protective layers, can help extend the durability and longevity of the material.
It’s important to note that the selection of a corrosion protection method for grey cast iron should consider the specific application, operating conditions, and the severity of the corrosive environment. Consulting with corrosion engineers or materials specialists can provide further guidance and expertise in selecting the most appropriate protection strategy.