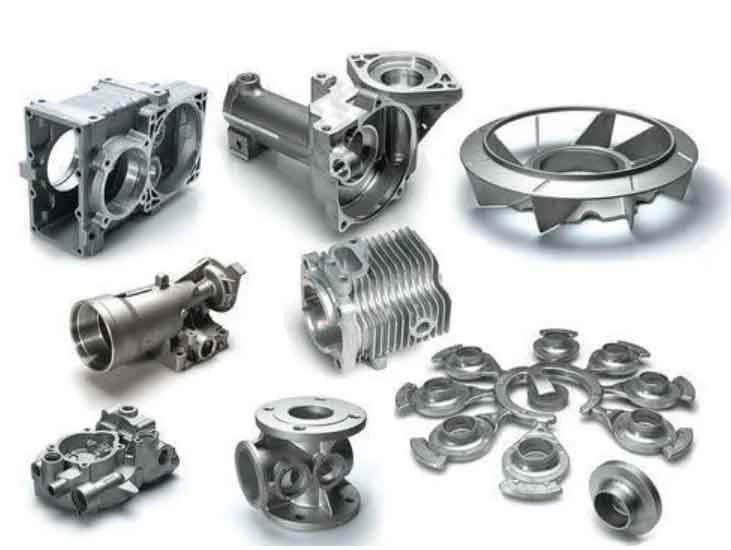
Corrosion resistance is one of the limitations of grey cast iron due to its microstructure, which includes graphite flakes that create potential pathways for corrosive agents. However, various surface coatings and treatments can be applied to improve the corrosion resistance of grey cast iron for specific applications. Here are some common methods used to enhance the corrosion resistance of grey cast iron:
1. Protective Coatings:
- Applying protective coatings, such as paints, epoxy coatings, or polymer coatings, can create a barrier between the metal surface and corrosive elements. These coatings help to prevent direct contact between the corrosive agents and the grey cast iron substrate, providing an effective corrosion barrier.
2. Galvanizing:
- Galvanizing involves coating the grey cast iron with a layer of zinc through hot-dip galvanizing or electroplating. The zinc coating acts as a sacrificial anode, corroding in preference to the grey cast iron substrate, thus providing cathodic protection and extending the material’s corrosion resistance.
3. Polymer and Composite Coatings:
- Polymer and composite coatings, such as epoxy resins filled with anti-corrosive additives or fiberglass-reinforced composites, can be used to provide both mechanical strength and enhanced corrosion resistance.
4. Electroless Nickel Plating:
- Electroless nickel plating is a process that deposits a nickel-phosphorus alloy coating on the grey cast iron surface. This plating enhances corrosion resistance, wear resistance, and hardness, making it suitable for various applications.
5. Ceramic Coatings:
- Ceramic coatings can be applied to grey cast iron surfaces using thermal spray or plasma spray techniques. These coatings offer excellent corrosion resistance, wear resistance, and thermal insulation properties.
6. Corrosion Inhibitors:
- Corrosion inhibitors can be applied as coatings or incorporated into the casting process to slow down the corrosion rate of grey cast iron. These inhibitors work by forming a protective film on the metal surface, reducing the metal’s susceptibility to corrosion.
7. Phosphating and Passivation:
- Phosphating involves treating the grey cast iron surface with a phosphate solution to create a phosphate coating that improves corrosion resistance. Passivation, on the other hand, involves creating a passive oxide layer on the surface to protect against corrosion.
It’s important to note that the effectiveness of these coatings and treatments depends on the specific application and the corrosive environment the grey cast iron will be exposed to. Additionally, some of these treatments may be more suitable for specific industries or applications than others. Proper selection, preparation, and application of the corrosion-resistant coatings are critical to achieving the desired level of protection and extending the service life of grey cast iron components in corrosive environments.