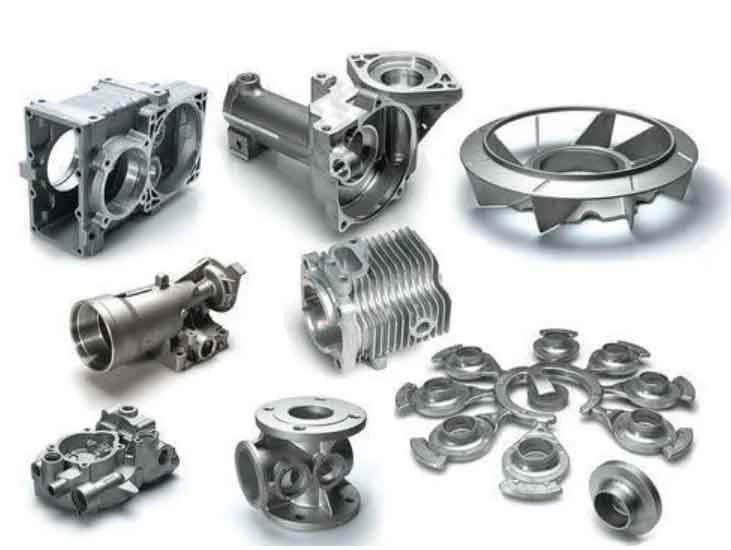
Grey cast iron has limited inherent corrosion resistance due to its high carbon content and the presence of graphite flakes, which create galvanic cells that promote corrosion. Additionally, the iron matrix in grey cast iron is prone to oxidation, further contributing to its susceptibility to corrosion. Addressing the challenges and finding suitable solutions are essential to improve the corrosion resistance of grey cast iron in various applications. Here are some challenges and possible solutions:
Challenges:
- Galvanic Corrosion: The presence of graphite flakes and the iron matrix creates galvanic cells, leading to galvanic corrosion when the iron is in contact with other metals or corrosive environments.
- Oxidation: The iron matrix in grey cast iron can oxidize in the presence of oxygen and moisture, leading to surface rust and accelerated corrosion.
- Porous Structure: The presence of pores and voids in the microstructure can trap corrosive agents, exacerbating localized corrosion.
Solutions:
- Protective Coatings: Applying protective coatings, such as paints, epoxy, or polymer coatings, can create a barrier between the grey cast iron surface and the corrosive environment, preventing direct contact and minimizing galvanic corrosion.
- Galvanic Protection: Implement galvanic protection techniques, such as sacrificial anodes or impressed current systems, to direct the corrosion away from the grey cast iron to a sacrificial metal.
- Surface Treatments: Surface treatments like shot blasting or mechanical polishing can help reduce the porosity of the grey cast iron surface, making it less susceptible to trapping corrosive agents.
- Corrosion Inhibitors: The use of corrosion inhibitors, either as surface treatments or incorporated into coatings, can help reduce the rate of corrosion and protect the grey cast iron from degradation.
- Alloying Elements: Select specific alloying elements, such as chromium or nickel, to improve the corrosion resistance of grey cast iron. These elements can form corrosion-resistant compounds, enhancing the material’s performance.
- Cathodic Protection: For submerged or buried grey cast iron components, cathodic protection systems can be employed to control corrosion by making the cast iron a cathode and protecting it from oxidation.
- Regular Maintenance: Regular inspection and maintenance can help identify and address corrosion issues promptly, prolonging the life of grey cast iron components.
- Environment Control: Limit exposure to corrosive environments or use protective measures when possible. For example, in the case of underground pipes, consider using protective coatings or cathodic protection systems.
It’s important to note that the effectiveness of these solutions depends on the specific application, the severity of the corrosive environment, and the required level of corrosion resistance. Consulting with corrosion engineers or materials experts can help determine the most suitable solutions for your specific grey cast iron application.