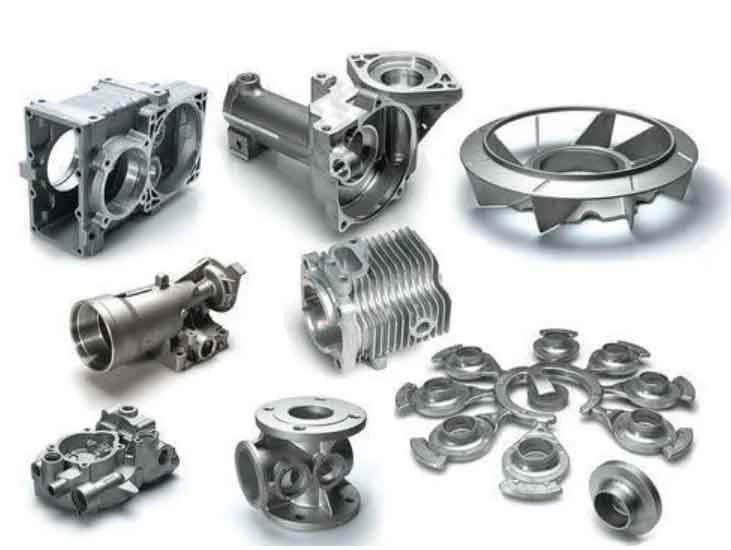
Advancements in casting technologies have led to significant improvements in producing high-quality and complex grey cast iron components. These technologies aim to enhance casting efficiency, reduce defects, and optimize material properties. Here are some key advancements in casting technologies for improved grey cast iron components:
1. Computer-Aided Design and Simulation:
- Computer-aided design (CAD) and simulation software enable engineers to design and optimize casting geometries more accurately. Casting simulation tools predict solidification patterns, identify potential defects, and optimize gating and riser designs, leading to improved casting quality and reduced trial-and-error iterations.
2. 3D Printing for Molds and Cores:
- Additive manufacturing or 3D printing is increasingly used to create sand molds and cores for casting. 3D-printed molds offer more design flexibility and can produce intricate and lightweight structures, resulting in resource and material savings.
3. Green Sand Reclamation:
- Foundries are investing in green sand reclamation technologies to recycle and reuse sand. By reclaiming sand, foundries reduce the need for new sand and minimize waste, contributing to sustainable and cost-effective production.
4. Automated Casting Cells:
- Automation and robotics are being integrated into casting processes, leading to more consistent and precise pouring and reduced labor-intensive tasks. Automated casting cells improve production efficiency, reduce the risk of human errors, and enhance overall quality control.
5. Vacuum Assisted Sand Casting (V-Process):
- Vacuum-assisted sand casting is a variation of sand casting where the pattern is held in a vacuum-sealed flask. This process reduces gas and vapor-related defects, leading to higher-quality castings.
6. Continuous Casting:
- Continuous casting techniques are used to produce long continuous bars or profiles of grey cast iron. This process improves casting efficiency and provides a consistent and uniform material.
7. Advanced Mold Coatings:
- Advanced mold coatings, such as zircon and ceramic coatings, are applied to molds to enhance mold durability and reduce defects like sand adhesion and metal penetration.
8. In-Mold Coating and Pre-Heating:
- In-mold coating and pre-heating of molds can help prevent surface defects and improve surface finish on castings.
9. Advanced Alloys and Chemical Composition Control:
- Advanced metallurgical practices and precise chemical composition control improve the mechanical properties of grey cast iron, tailoring the material to specific applications.
10. Real-Time Process Monitoring:
- Implementing real-time monitoring systems allows foundries to detect process deviations promptly, enabling timely adjustments and ensuring consistent casting quality.
These advancements in casting technologies have enabled foundries to produce grey cast iron components with improved mechanical properties, reduced defects, and enhanced dimensional accuracy. As casting technologies continue to evolve, the capabilities of grey cast iron will be further expanded, making it a more competitive and attractive material for various industries.