The surface of high nickel ductile iron samples during corrosion process was observed. The results are similar to that of high silicon molybdenum ductile iron. No obvious bubbles were found on the surface of the samples. After testing, the surface basically maintains the original metallic gloss. No point corrosion and corrosion cracks were observed, and the corrosion was relatively uniform. It shows that high nickel ductile iron also has good corrosion resistance.
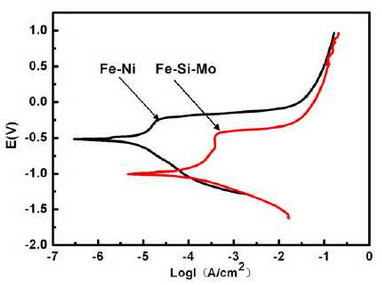
Figure 1 shows the polarization curves of high nickel ductile iron and high silicon molybdenum ductile iron in 3.5% NaC solution.The calculated corrosion potential (Ecorr) and corrosion current (Icorr) of high nickel ductile iron are -0.523V and 0.36 x 10-4A/cm2 respectively according to the polarization curve.Although there is no obvious passivation zone in the corrosion process of high nickel ductile iron, compared with high silicon-molybdenum ductile iron, the corrosion potential of high nickel ductile iron deflects more in the positive direction. The corrosion current of high nickel ductile iron is 0.479V higher than that of high silicon-molybdenum ductile iron and 2.37 A/cm2 lower, which indicates that the corrosion resistance of high nickel ductile iron is better than that of high silicon-molybdenum ductile iron.
The main reason is that the addition of more elements to improve corrosion resistance in high nickel ductile iron is higher than that in silicon-molybdenum ductile iron, and the addition of elements such as Cr and Mn will form carbides with carbon, which will greatly reduce the graphite content.It also promotes and stabilizes austenitizing elements; on the other hand, the ductility of high nickel ductile iron is lower than that of high silicon molybdenum ductile iron, which results in little difference in internal potential of such cast iron, resulting in that the corrosion resistance of high nickel ductile iron is better than that of high silicon molybdenum ductile iron.