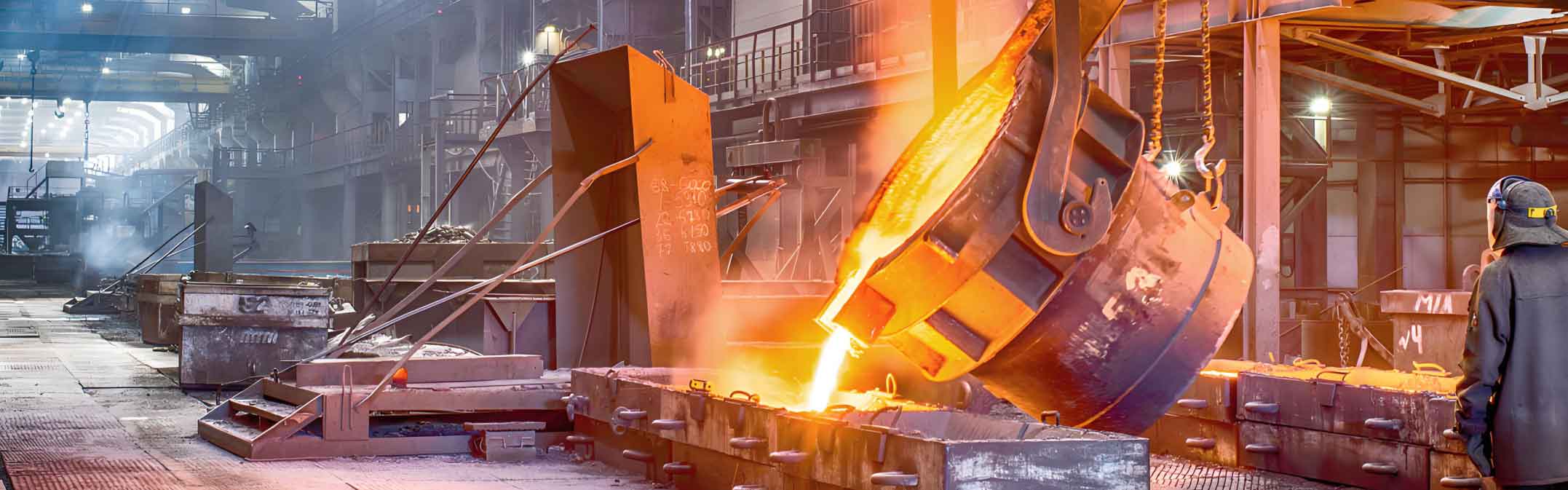
Introduction
Investment casting and sand casting are two prominent methods in industrial manufacturing, each with distinct advantages and disadvantages. This analysis compares these methods based on cost, efficiency, precision, material versatility, and application suitability.
Investment Casting
Advantages:
- Precision and Detail:
- Investment casting can produce highly detailed and intricate components with tight tolerances.
- Surface finishes are generally smoother, reducing the need for post-processing.
- Material Versatility:
- Suitable for a wide range of metals, including alloys that are difficult to cast using other methods.
- Dimensional Accuracy:
- Achieves better dimensional accuracy, making it ideal for complex geometries.
- Reduced Material Waste:
- The process allows for near-net-shape casting, minimizing material waste.
Disadvantages:
- High Initial Cost:
- The cost of creating molds and patterns is high.
- Investment casting requires significant upfront investment in tooling.
- Longer Production Cycle:
- The process involves multiple steps, leading to longer production times.
- Suitable for small to medium batch sizes.
- Limited Size:
- Generally limited to smaller components due to the constraints of the process.
Sand Casting
Advantages:
- Lower Initial Cost:
- Molds are made of sand, which is inexpensive and readily available.
- Lower cost for pattern creation and mold making.
- Flexibility in Size:
- Capable of producing large and heavy components.
- Suitable for both small and large-scale production runs.
- Quick Turnaround:
- Faster mold making and casting process.
- Ideal for short lead times.
- Simplicity:
- Simple process with fewer steps compared to investment casting.
Disadvantages:
- Surface Finish and Precision:
- Generally produces rougher surfaces, requiring additional machining.
- Less precise than investment casting, with higher tolerances.
- Material Waste:
- Typically produces more material waste due to excess material in the gating system.
- Dimensional Accuracy:
- Less accurate, leading to potential issues with tight tolerances.
Cost Comparison
- Tooling and Setup Costs:
- Investment Casting: High initial costs for tooling and patterns.
- Sand Casting: Lower initial costs, making it more economical for low-volume production.
- Material Costs:
- Investment Casting: Efficient use of material with less waste.
- Sand Casting: Higher material waste and potential for higher overall material costs.
- Labor Costs:
- Investment Casting: Higher labor costs due to the complexity of the process.
- Sand Casting: Lower labor costs due to the simplicity and automation potential.
- Post-Processing Costs:
- Investment Casting: Minimal post-processing required.
- Sand Casting: Significant post-processing needed for surface finishing and precision.
Benefit Comparison
- Production Volume:
- Investment Casting: More suitable for low to medium volumes with high precision.
- Sand Casting: Better for high-volume production and larger components.
- Application Suitability:
- Investment Casting: Aerospace, medical devices, and complex industrial parts.
- Sand Casting: Automotive parts, large machinery, and general industrial applications.
- Lead Times:
- Investment Casting: Longer lead times due to the complexity of the process.
- Sand Casting: Shorter lead times, beneficial for rapid prototyping and urgent production needs.
Conclusion
- Investment Casting is ideal for high-precision, complex parts with stringent tolerances and superior surface finish requirements. However, it involves higher initial costs and longer production cycles.
- Sand Casting is suitable for larger, less complex parts and offers cost advantages for high-volume production. It is more flexible in terms of size but may require additional post-processing.
The choice between investment casting and sand casting depends on specific project requirements, including precision, volume, size, and budget.