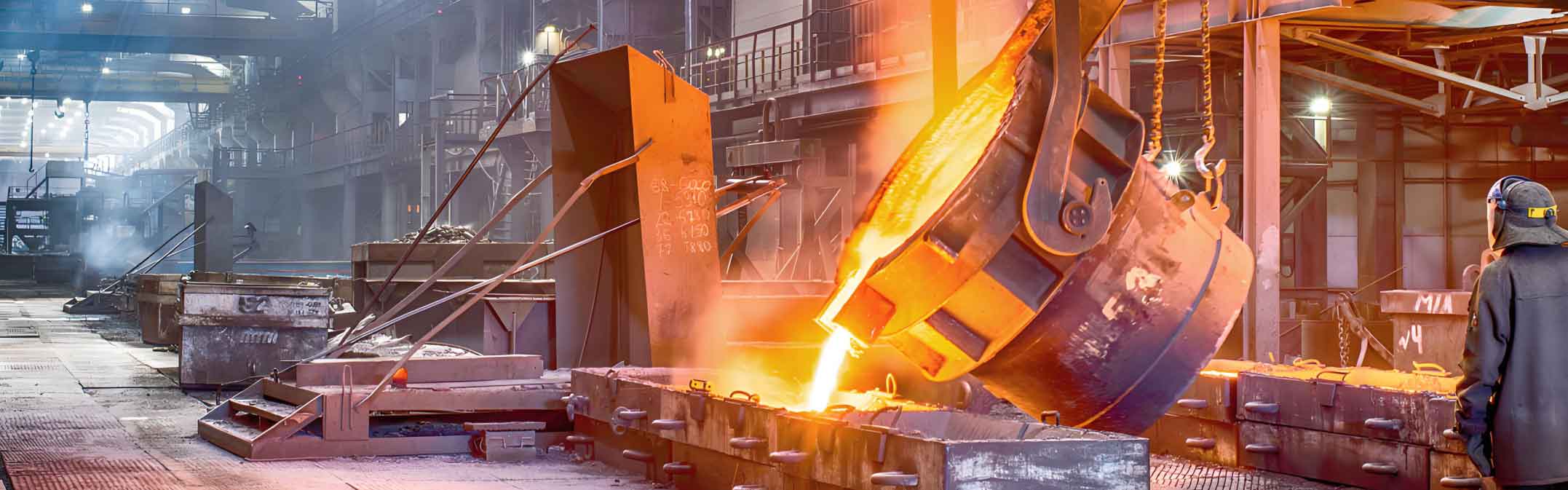
Investment casting is renowned for producing high-precision components with intricate details and excellent surface finishes. However, the costs associated with investment casting can be a barrier, particularly for small to medium enterprises. This article explores cost-effective solutions that can make investment casting more accessible and economical for small to medium enterprises, ensuring they can leverage its advantages without compromising on quality.
Understanding Investment Casting
Investment casting involves creating a wax pattern, coating it with a refractory ceramic material to form a mold, and then melting out the wax to leave a cavity into which molten metal is poured. The process results in parts with exceptional detail and accuracy, making it suitable for applications requiring high precision and complex geometries.
Key Benefits of Investment Casting
- High Precision and Accuracy
- Investment casting produces components with tight tolerances and intricate details.
- Superior Surface Finish
- The parts have a smooth surface finish, reducing the need for secondary machining.
- Design Flexibility
- The process allows for complex and thin-walled designs that are difficult to achieve with other methods.
- Material Versatility
- Investment casting can be used with a wide range of metals and alloys.
Cost-Effective Solutions for Investment Casting
While investment casting can be cost-intensive, several strategies can help small to medium enterprises manage and reduce costs effectively. These strategies include optimizing the casting process, using cost-effective materials, leveraging advanced technologies, and adopting efficient production practices.
1. Process Optimization
Process optimization is critical in reducing costs in investment casting. By streamlining the casting process, enterprises can minimize waste, improve efficiency, and reduce production times.
Key Strategies:
- Simulation Software:
- Utilize casting simulation software to predict potential defects and optimize mold design. This reduces trial-and-error iterations and saves material and time.
- Lean Manufacturing:
- Implement lean manufacturing principles to eliminate waste and improve workflow. This includes just-in-time production and continuous improvement practices.
- Standardization:
- Standardize components and processes where possible to reduce variability and improve efficiency. This can lead to cost savings in both production and quality control.
2. Cost-Effective Materials
Selecting the right materials can significantly impact the cost-effectiveness of investment casting. While high-performance alloys are often necessary, there are ways to optimize material usage without compromising quality.
Key Strategies:
- Material Substitution:
- Where appropriate, substitute expensive materials with more cost-effective alternatives that meet the required specifications.
- Material Recycling:
- Implement material recycling practices to reuse excess or scrap metal, reducing material costs and environmental impact.
- Alloy Optimization:
- Use optimized alloys that provide the necessary properties at a lower cost. Work with suppliers to identify cost-effective alloy compositions.
3. Advanced Technologies
Leveraging advanced technologies can enhance the efficiency and cost-effectiveness of the investment casting process. These technologies include automation, additive manufacturing, and advanced quality control systems.
Key Technologies:
- Automation:
- Use automation in repetitive tasks such as wax pattern production and mold assembly. Automation improves consistency and reduces labor costs.
- Additive Manufacturing:
- Incorporate additive manufacturing for rapid prototyping and creating complex wax patterns. This can reduce lead times and costs associated with traditional pattern making.
- Quality Control Systems:
- Implement advanced quality control systems, including non-destructive testing and real-time monitoring, to detect defects early and reduce rework costs.
4. Efficient Production Practices
Adopting efficient production practices can help small to medium enterprises achieve cost savings while maintaining high-quality standards in investment casting.
Key Practices:
- Batch Processing:
- Group similar parts into batches to maximize furnace usage and reduce energy costs.
- Supplier Partnerships:
- Develop strong partnerships with suppliers to negotiate better prices for raw materials and services. Collaborative relationships can also lead to innovations and cost savings.
- Training and Workforce Development:
- Invest in training and developing the workforce to enhance skills and efficiency. A skilled workforce can identify cost-saving opportunities and improve overall productivity.
Table 1: Cost-Effective Strategies in Investment Casting
Strategy | Description | Benefits |
---|---|---|
Process Optimization | Use of simulation software, lean principles | Reduced waste, improved efficiency |
Cost-Effective Materials | Material substitution, recycling, optimization | Lower material costs, sustainability |
Advanced Technologies | Automation, additive manufacturing, quality control | Enhanced efficiency, reduced labor costs |
Efficient Production | Batch processing, supplier partnerships, training | Cost savings, improved productivity |
Case Studies and Real-World Examples
Case Study 1: Automotive Component Manufacturer
Challenge:
- High production costs for complex engine components.
Solution:
- Implemented casting simulation software to optimize mold design, reducing material waste and improving yield.
- Substituted high-cost alloys with optimized alloy compositions that met performance requirements.
Results:
- Achieved a 15% reduction in material costs and a 10% improvement in production efficiency.
Case Study 2: Aerospace Parts Supplier
Challenge:
- Long lead times and high costs for producing precision aerospace parts.
Solution:
- Leveraged additive manufacturing to produce complex wax patterns, reducing pattern production time.
- Adopted automation in mold assembly and quality control processes.
Results:
- Reduced lead times by 20% and labor costs by 25%, while maintaining high precision and quality standards.
Table 2: Summary of Case Studies
Case Study | Industry | Key Strategies | Results |
---|---|---|---|
Automotive Components | Automotive | Simulation software, alloy optimization | 15% material cost reduction, 10% efficiency improvement |
Aerospace Parts | Aerospace | Additive manufacturing, automation | 20% reduction in lead times, 25% labor cost reduction |
Conclusion
Investment casting offers numerous benefits, including high precision, excellent surface finish, and the ability to produce complex designs. For small to medium enterprises, managing the costs associated with investment casting is crucial for maintaining competitiveness and profitability. By optimizing the casting process, using cost-effective materials, leveraging advanced technologies, and adopting efficient production practices, these enterprises can achieve significant cost savings without compromising on quality.
The strategies and solutions outlined in this article provide a roadmap for small to medium enterprises to make investment casting a viable and cost-effective manufacturing method. With careful planning and implementation, investment casting can deliver high-quality components that meet the demanding requirements of modern industries while ensuring economic sustainability.