Grey cast iron has been a cornerstone material in the construction of heavy machinery due to its unique properties such as excellent castability, machinability, and vibration damping characteristics. This article presents a comprehensive analysis of grey cast iron’s application in heavy machinery through various case studies, highlighting its performance, benefits, and challenges.
Introduction to Grey Cast Iron
Grey cast iron, named for the grey color of its fractured surface, is distinguished by its graphite flake microstructure. This structure provides grey cast iron with excellent thermal conductivity, good wear resistance, and superior vibration damping properties, making it ideal for use in heavy machinery.
Properties of Grey Cast Iron
- Composition: Typically consists of 2.5-4.0% carbon, 1.0-3.0% silicon, 0.2-1.0% manganese, with trace amounts of sulfur and phosphorus.
- Mechanical Properties:
- Tensile Strength: 150-400 MPa
- Compressive Strength: 600-1200 MPa
- Hardness: 150-300 HB
- Density: 6.8-7.4 g/cm³
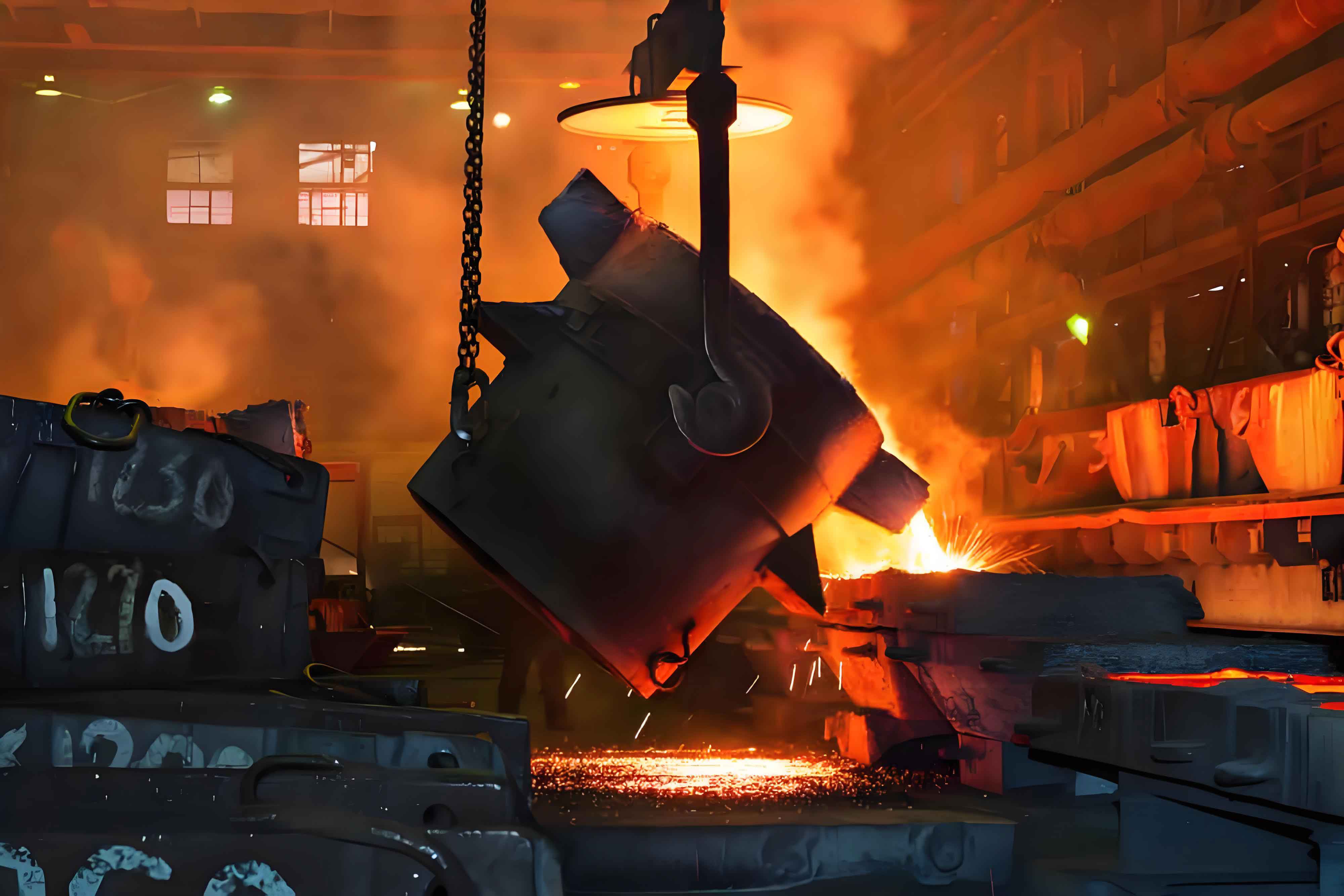
Case Studies in Heavy Machinery
Case Study 1: Engine Blocks in Construction Equipment
Application Overview
Engine blocks in construction equipment are critical components that house the cylinders, pistons, and other vital parts of an engine. They require materials that can withstand high temperatures, pressure, and mechanical stress.
Use of Grey Cast Iron
Grey cast iron is extensively used for engine blocks due to its excellent thermal conductivity and vibration damping properties. These attributes help in managing the heat generated during engine operation and in reducing noise and vibration.
Performance Analysis
- Durability: Engine blocks made from grey cast iron exhibit high durability under operational stresses.
- Thermal Management: The thermal conductivity of grey cast iron helps in efficient heat dissipation, preventing overheating.
- Cost-Effectiveness: Grey cast iron is more cost-effective compared to other materials like aluminum or steel, making it a preferred choice for large-scale manufacturing.
Performance Metric | Grey Cast Iron Engine Blocks |
---|---|
Durability | High |
Thermal Management | Excellent |
Cost-Effectiveness | High |
Case Study 2: Gear Housings in Mining Equipment
Application Overview
Gear housings in mining equipment protect gears and other components from harsh environmental conditions, such as dust, moisture, and mechanical impact.
Use of Grey Cast Iron
Grey cast iron is chosen for gear housings due to its excellent castability, which allows for complex shapes, and its inherent damping properties, which reduce noise and vibration in heavy-duty machinery.
Performance Analysis
- Wear Resistance: Grey cast iron’s wear resistance ensures long service life in abrasive mining environments.
- Machinability: The material’s machinability allows for precise manufacturing of gear housings, ensuring proper fit and function.
- Structural Integrity: The compressive strength of grey cast iron provides robust structural integrity to gear housings.
Performance Metric | Grey Cast Iron Gear Housings |
---|---|
Wear Resistance | High |
Machinability | Excellent |
Structural Integrity | High |
Case Study 3: Brake Discs in Heavy Trucks
Application Overview
Brake discs in heavy trucks are critical for ensuring the safety and control of the vehicle. They must withstand high temperatures and mechanical stress during braking.
Use of Grey Cast Iron
Grey cast iron is widely used for brake discs due to its excellent thermal conductivity and ability to handle high frictional forces without significant wear.
Performance Analysis
- Heat Resistance: Grey cast iron brake discs effectively dissipate heat generated during braking, preventing brake fade.
- Frictional Performance: The material provides consistent frictional performance, ensuring reliable braking.
- Cost Efficiency: The cost efficiency of grey cast iron makes it a practical choice for manufacturing brake discs for heavy trucks.
Performance Metric | Grey Cast Iron Brake Discs |
---|---|
Heat Resistance | Excellent |
Frictional Performance | Consistent |
Cost Efficiency | High |
Benefits of Grey Cast Iron in Heavy Machinery
Vibration Damping
One of the most significant advantages of grey cast iron in heavy machinery is its vibration damping capability. This property is crucial in reducing noise and enhancing the comfort and safety of operators.
Castability
The excellent castability of grey cast iron allows for the production of complex shapes and designs, which is particularly beneficial in manufacturing intricate components for heavy machinery.
Wear Resistance
Grey cast iron’s wear resistance ensures that components have a long service life, even in harsh operating conditions. This property is particularly valuable in applications like mining and construction where equipment is subjected to abrasive materials.
Thermal Conductivity
The high thermal conductivity of grey cast iron helps in efficient heat management, which is critical in applications such as engine blocks and brake discs. This property prevents overheating and ensures consistent performance.
Challenges in Using Grey Cast Iron
Brittleness
One of the primary challenges of using grey cast iron is its brittleness. The presence of graphite flakes, while beneficial for damping and thermal conductivity, makes the material more prone to cracking under impact.
Weight
Grey cast iron is heavier compared to other materials like aluminum, which can be a disadvantage in applications where weight reduction is crucial.
Corrosion Resistance
Grey cast iron has limited corrosion resistance, which can be a concern in certain environments. Protective coatings and treatments are often required to enhance its durability in such conditions.
Advanced Technologies for Enhancing Grey Cast Iron Performance
Heat Treatment
Heat treatment processes such as annealing, normalizing, and tempering can significantly improve the mechanical properties of grey cast iron, enhancing its durability and performance in heavy machinery.
Surface Coating
Applying surface coatings can enhance the wear and corrosion resistance of grey cast iron components, extending their service life and reliability in harsh environments.
Alloying
Adding alloying elements such as nickel, chromium, and molybdenum can improve the strength, hardness, and corrosion resistance of grey cast iron, making it more suitable for demanding applications.
Conclusion
Grey cast iron remains a vital material in the manufacturing of heavy machinery due to its unique properties and cost-effectiveness. Through various case studies, it is evident that grey cast iron provides excellent performance in applications such as engine blocks, gear housings, and brake discs. While there are challenges associated with its use, advanced technologies and methods can mitigate these issues, further enhancing the material’s capabilities. By leveraging the benefits of grey cast iron and addressing its limitations, manufacturers can continue to produce high-quality, durable, and reliable components for heavy machinery.
Benefit | Description |
---|---|
Vibration Damping | Reduces noise and enhances operator comfort and safety |
Castability | Allows for the production of complex shapes and designs |
Wear Resistance | Ensures long service life in harsh operating conditions |
Thermal Conductivity | Efficient heat management prevents overheating |
Challenge | Description |
---|---|
Brittleness | Prone to cracking under impact |
Weight | Heavier compared to other materials |
Corrosion Resistance | Limited resistance, requires protective coatings |
By understanding the role of grey cast iron in heavy machinery and employing advanced methods and technologies, manufacturers can optimize the performance and reliability of their products, meeting the demanding requirements of modern engineering and manufacturing.