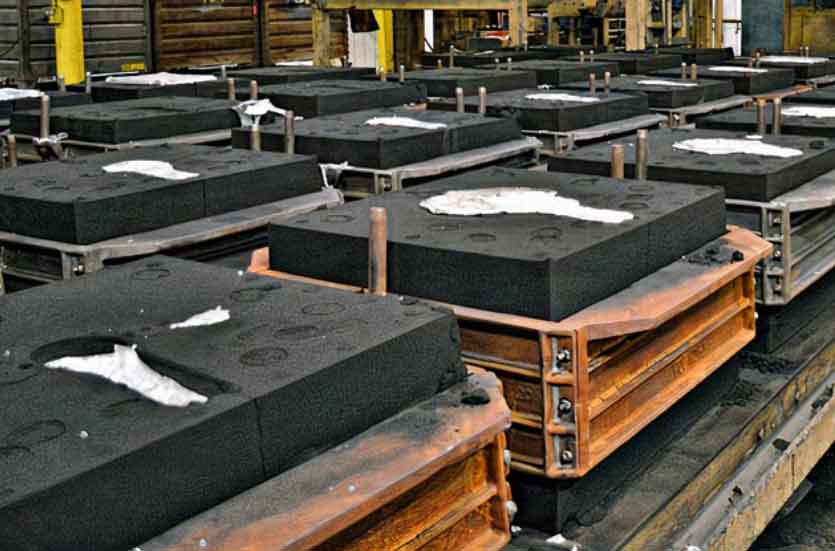
Resin sand casting offers several cost-effective solutions that contribute to maximizing efficiency in the manufacturing process. These solutions help reduce production costs, optimize resource utilization, and enhance overall productivity. Here are some ways in which resin sand casting achieves cost-efficiency:
- Reduced Tooling Costs: Resin sand casting eliminates the need for expensive and time-consuming tooling, as it uses reusable patterns or 3D-printed molds. This significantly reduces initial setup costs, making it an attractive option for small to medium-scale production runs.
- Rapid Prototyping: Resin sand casting enables rapid prototyping, allowing manufacturers to quickly test and validate designs before committing to mass production. This iterative approach helps identify and rectify design flaws early on, reducing costly mistakes in the final production stages.
- Improved Production Speed: The ability to create complex molds using 3D printing technology or patternless molding systems reduces the lead time required for traditional pattern making. Faster mold production translates to quicker turnaround times, increasing production efficiency.
- Higher Production Rates: Resin sand casting can achieve higher production rates compared to other casting methods, making it suitable for large-scale production. The continuous use of reusable molds, combined with automated processes, ensures a steady output of cast parts.
- Minimal Material Waste: Resin sand casting minimizes material waste by reusing sand and reclaiming excess sand through reclamation systems. The reduction in material waste contributes to cost savings and aligns with sustainable manufacturing practices.
- Lower Labor Costs: The automation of various steps in the casting process, such as sand mixing, mold handling, and post-processing, reduces the need for manual labor. This not only cuts labor costs but also improves consistency and quality control.
- Energy Efficiency: Resin sand casting typically requires lower melting temperatures compared to other casting methods, reducing energy consumption and associated costs.
- Scalability: Resin sand casting is highly scalable, making it cost-effective for both small and large production volumes. Manufacturers can easily adjust production levels to meet changing market demands.
- Innovative Materials: Advancements in resin formulations and sand binders have led to more cost-efficient options that still offer high-quality castings.
- Quality Control: The ability to predict and address potential defects using simulation software helps avoid costly rework and scrap, ensuring better overall production efficiency.
By leveraging the advantages of resin sand casting, manufacturers can achieve cost-effectiveness, optimize production processes, and deliver high-quality components to meet the demands of various industries. As the industry continues to evolve, ongoing innovations are expected to further enhance the cost-efficiency of resin sand casting methods.