Cost reduction is essential for maintaining competitiveness in the manufacturing sector. ZHY Casting, by employing strategic cost reduction techniques in their sand casting operations, can enhance efficiency and profitability without compromising on quality. Here are several effective strategies to consider:
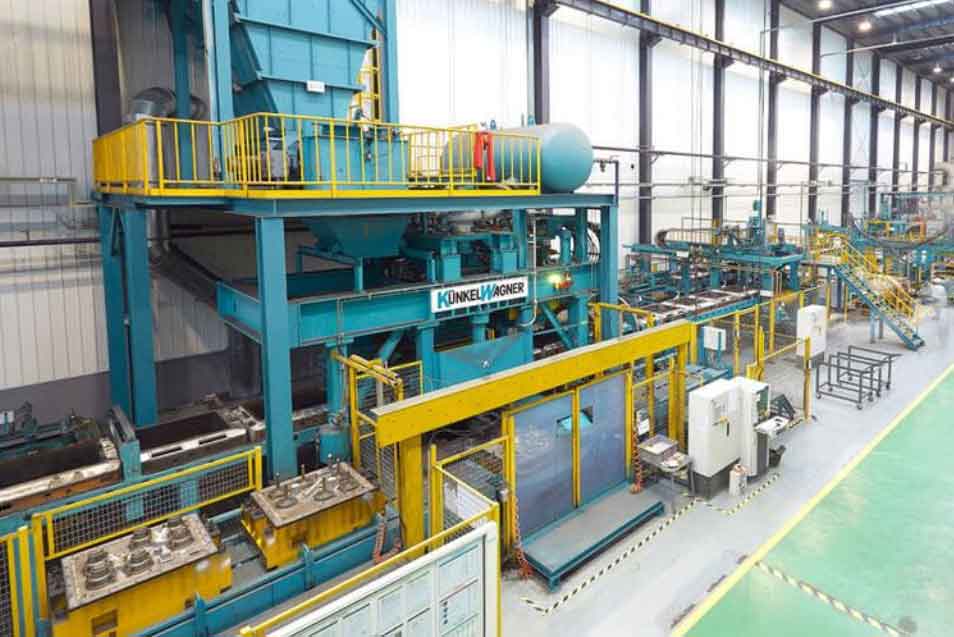
1. Optimize Material Use
- Efficient Design: Utilize computer-aided design (CAD) and simulation software to optimize sand casting designs, reducing material wastage and ensuring minimal usage of raw materials without sacrificing product integrity.
- Recycling: Implement systems for recycling sand and other materials used in sand casting process. Sand reclamation systems can significantly reduce the need for new sand, lowering material costs.
2. Improve Process Efficiency
- Lean Manufacturing: Adopt lean manufacturing principles to streamline processes, reduce waste, and minimize defects. This includes techniques like value stream mapping to identify and eliminate non-value-adding steps.
- Advanced Process Control: Use real-time monitoring and control systems to optimize sand casting parameters such as temperature and pouring rates, reducing scrap rates and energy consumption.
3. Enhance Energy Efficiency
- Energy-Efficient Equipment: Invest in modern, energy-efficient furnaces and other machinery that reduce energy consumption. High-efficiency equipment may have higher upfront costs but will save money in the long term through reduced energy bills.
- Scheduled Maintenance: Maintain equipment regularly to ensure it operates at peak efficiency, preventing energy wastage and costly breakdowns.
4. Outsource Non-Core Activities
- Specialized Services: Outsource non-core activities such as certain types of finishing or even some elements of the manufacturing process to specialized providers who can perform these tasks more cost-effectively.
- Supply Chain Optimization: Review and optimize the supply chain by collaborating with suppliers to reduce costs, such as negotiating bulk purchase discounts or more favorable delivery terms.
5. Technology and Automation
- Automation: Implement automated systems for tasks like mold making and core setting, which can reduce labor costs and increase production speed and consistency.
- 3D Printing: Use 3D printing for creating complex cores and molds, which can reduce lead times and waste associated with traditional mold-making.
6. Workforce Training and Management
- Skilled Workforce: Invest in training programs to enhance the skills of the workforce, improving productivity and reducing errors, which in turn decreases the cost of rework and scrap.
- Employee Engagement: Develop a culture of continuous improvement, encouraging employees to come up with innovative ideas to reduce costs and improve efficiency.
7. Quality Control Enhancements
- Preventive Quality Control: Strengthen the quality control processes to detect and resolve issues early in the production cycle, minimizing costly rework and scrap.
- Statistical Process Control (SPC): Implement SPC to monitor and control quality during the manufacturing process, thereby reducing variability and improving yield.
8. Review and Negotiate Contracts
- Supplier Contracts: Regularly review contracts with suppliers to ensure they are still competitive. Negotiate better terms based on loyalty and volume commitments.
- Utility Contracts: Review utility usage and costs, and negotiate contracts to take advantage of the best rates or consider alternative energy sources where feasible.
By integrating these strategies into their operations, ZHY Casting can significantly reduce costs while still maintaining or even improving the quality of their products. Such measures not only aid in short-term financial health but also support long-term sustainability and growth.