Cracks and fractures in heat treatment can have severe implications for the integrity and performance of treated components. Understanding the types, causes, and preventive measures related to cracking is essential. Here’s an exploration of cracks and fractures in heat treatment:
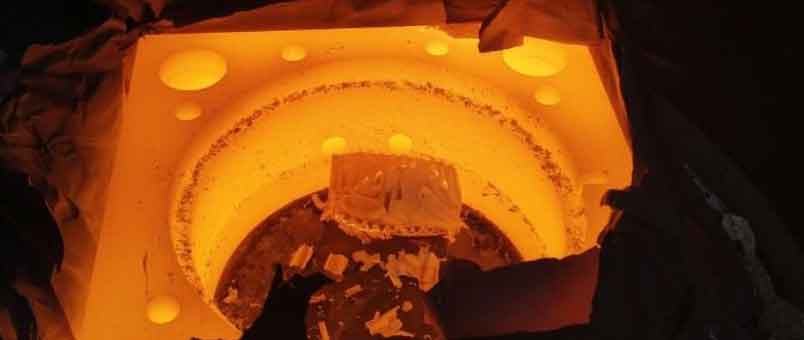
- Quench Cracks: Quench cracks are among the most common types of cracks encountered in heat treatment. They occur due to thermal stresses induced during rapid cooling (quenching) of the material. Quench cracks typically appear as straight or jagged lines on the surface or within the material.Causes:
- High thermal gradients during quenching.Non-uniform cooling rates due to variations in section thickness or geometry.Improper quenching media selection or agitation methods.Presence of internal stresses or pre-existing defects.
- Optimize quenching parameters, including selection of appropriate quenching media.
- Ensure uniform and controlled cooling rates.
- Preheat the material to reduce thermal gradients.
- Use fixtures or jigs to control component movement during quenching.
- Employ stress-relieving techniques like tempering after quenching.
- Stress Corrosion Cracking (SCC): Stress corrosion cracking is a type of cracking that occurs in the presence of a corrosive environment, combined with tensile stress. The combination of stress and corrosion causes cracks to initiate and propagate, compromising the material’s integrity.Causes:
- Presence of corrosive substances (e.g., chemicals, moisture) in the environment.Tensile stress acting on the material, which can be residual or applied.Material susceptibility to stress corrosion cracking.
- Select materials resistant to stress corrosion cracking.
- Minimize exposure to corrosive environments.
- Apply surface treatments or coatings to protect against corrosion.
- Reduce residual stresses through appropriate heat treatment or stress relief methods.
- Design components to minimize stress concentrations.
- Intergranular Cracking: Intergranular cracking refers to cracking that occurs along grain boundaries in the material. It can be caused by various factors, such as improper heat treatment, material contamination, or alloy sensitization.Causes:
- Carbide precipitation along grain boundaries during heat treatment.Material contamination, leading to embrittlement or reduced grain boundary cohesion.Alloy sensitization, especially in stainless steels.
- Employ suitable heat treatment processes to prevent carbide precipitation.
- Minimize material contamination during processing.
- Select appropriate materials with improved resistance to intergranular cracking.
- Control heat treatment parameters to prevent sensitization in stainless steels.
- Conduct proper post-weld heat treatment to address sensitization in welded components.
- Fatigue Cracking: Fatigue cracking occurs due to cyclic loading and repeated stress cycles on the material, leading to crack initiation and propagation. Heat-treated components subjected to cyclic loading can be susceptible to fatigue cracking.Causes:
- Cyclic loading or repeated stress cycles.Insufficient strength or toughness of the material.Presence of stress concentrations.Improper heat treatment, leading to reduced fatigue strength.
- Select materials with improved fatigue resistance.
- Avoid or minimize stress concentrations through proper design and component geometry.
- Implement appropriate heat treatment processes to enhance fatigue strength.
- Conduct fatigue testing to determine the fatigue life of the material.
- Apply surface treatments or coatings to enhance fatigue resistance.
- Hydrogen Embrittlement: Hydrogen embrittlement is a phenomenon where absorbed hydrogen in the material causes loss of ductility and promotes crack propagation. It can occur during heat treatment or subsequent processing steps involving exposure to hydrogen.Causes:
- Absorption of hydrogen during heat treatment or exposure to hydrogen-rich environments.High-strength steels and certain alloys are more susceptible to hydrogen embrittlement.Presence of tensile stress or stress concentrations.
- Control hydrogen exposure during heat treatment and subsequent processing.
- Implement proper heat treatment procedures to minimize hydrogen absorption.
- Conduct hydrogen embrittlement testing to evaluate material susceptibility.
- Select materials with improved resistance to hydrogen embrittlement.
- Apply protective coatings or treatments to reduce hydrogen ingress.
It’s crucial to consider multiple factors when addressing cracking in heat treatment, including material selection, process optimization, design considerations, and post-treatment measures. Collaboration between heat treatment experts, metallurgists, and material engineers can help develop effective strategies to prevent and mitigate cracking issues.