According to the existing production conditions and selected materials of the author’s company, large ladle leakage ladle casting is used ϕ 50 mm sprue ceramic refractory gate pipe open gating system. Due to the small production volume in the development stage, it is arranged according to one type and one piece, and the upper and lower boxes are used for molding. The shrinkage rate of sand casting for the main size of the mold is 2%.
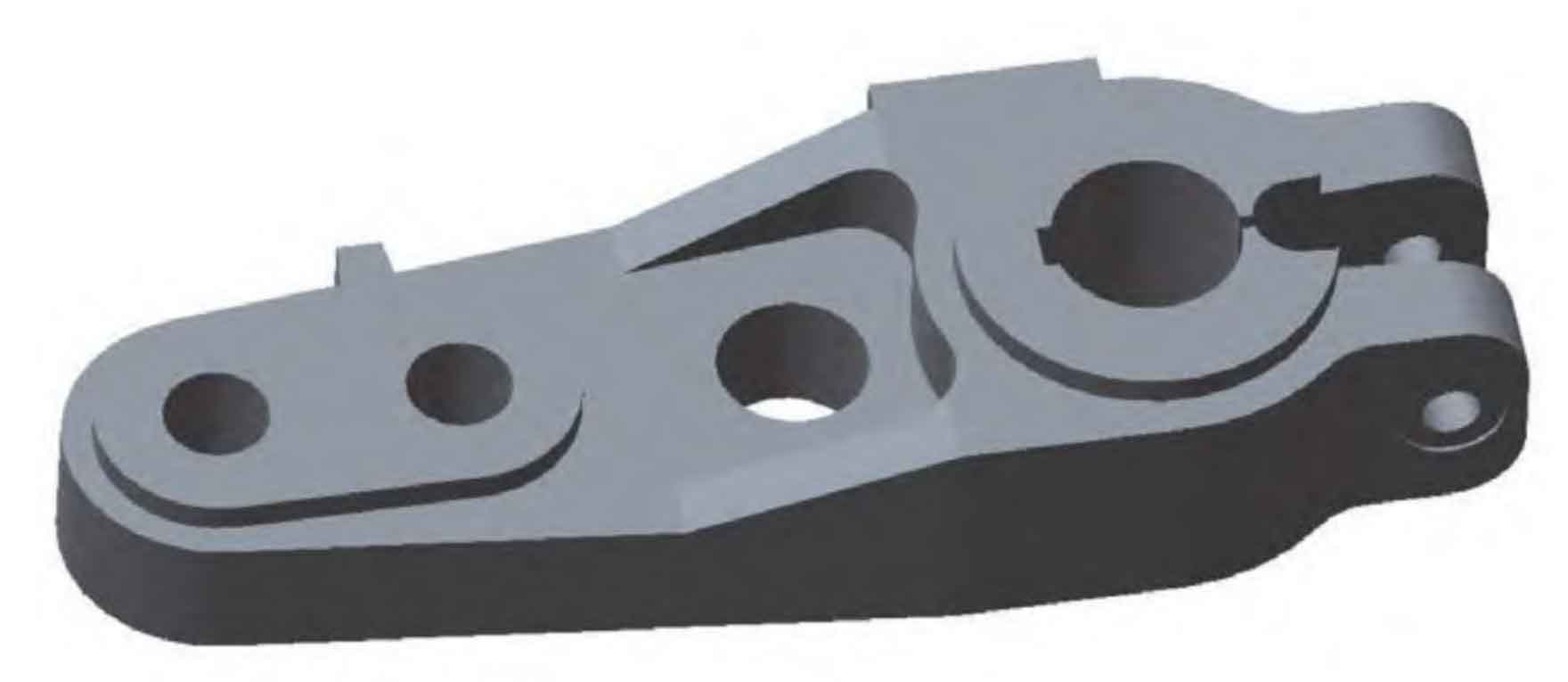
The side with small plane height difference is used as the upper mold. In order to facilitate mold lifting, R50 mm is used as the parting surface. Most sand castings are located in the lower mold. The mold is formed by using water glass organic ester self-hardening sand machine, ϕ The 100 mm relief hole is brought out by the external mold, and the rest holes are cast by sand core. because ϕ There are two 90 mm machining holes. After setting the same machining allowance, one core box can be made, and one core box can be made for key slot hole. Then, there are two core boxes for the whole pumping unit crank. Among them, ϕ The working height of the core is 139 mm after the processing allowance is set for the 90 mm processing hole, and the thickness is consistent. The upper core is not set with the core head due to the riser arrangement. If the lower core head is unstable, it is easy to cause the sand casting defect of eccentric core. Therefore, the lower core head of the core should be made deep (80 mm) and large to avoid top-heavy, so as to increase the stability of the core.