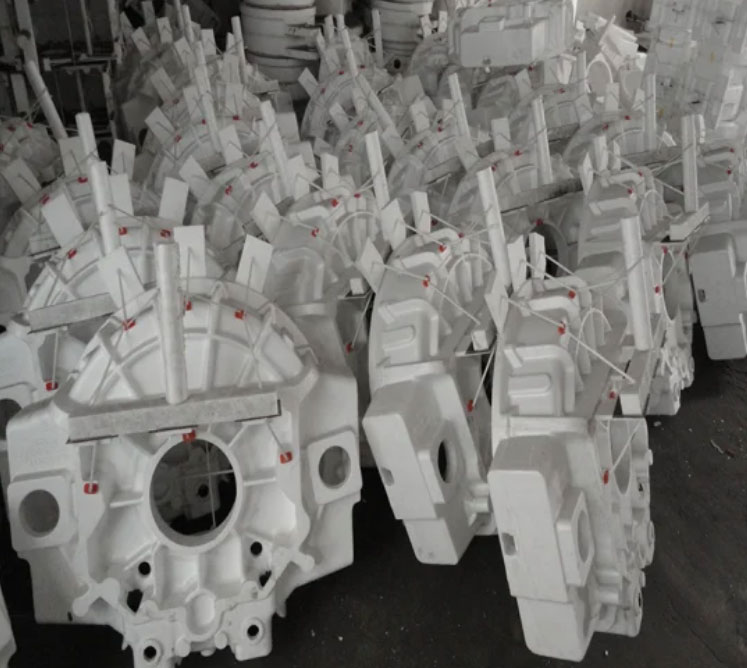
Lost foam casting offers unparalleled design freedom, making it an ideal choice for creating complex shapes and intricate geometries with ease. This innovative casting process allows engineers and designers to push the boundaries of traditional casting limitations and unlock a world of new design possibilities. Here are some ways in which lost foam casting unleashes design potential:
1. Intricate and Complex Designs:
- Lost foam casting enables the production of parts with intricate and complex designs that would be difficult or impossible to achieve with conventional casting methods. The foam patterns used in lost foam casting can be easily shaped and carved into almost any form, giving designers the flexibility to create components with intricate details and unconventional geometries.
2. Near Net Shape Castings:
- Lost foam casting produces near net shape castings, meaning that the final product closely resembles the desired shape with minimal post-casting machining or finishing required. This significantly reduces material waste and machining costs associated with removing excess material from the castings.
3. Consolidation of Parts:
- With lost foam casting, multiple components can be integrated into a single casting, consolidating parts and reducing the need for assembly and fastening. This not only streamlines the manufacturing process but also enhances the structural integrity and reliability of the final product.
4. Hollow and Cored Structures:
- Lost foam casting is well-suited for creating hollow and cored structures within castings. By using foam patterns with cavities, designers can produce castings with complex internal passages, cooling channels, or even intricate artistic patterns.
5. Weight Reduction:
- The ability to create complex and lightweight designs is particularly valuable in industries such as automotive and aerospace, where weight reduction is a key factor in improving fuel efficiency, performance, and payload capacity.
6. Reduced Tooling Costs:
- Lost foam casting requires relatively simple and cost-effective tools, as foam patterns are easy to create and shape. This can lead to significant cost savings compared to conventional casting methods that require complex dies or patterns.
7. Rapid Prototyping:
- The ease of creating foam patterns allows for rapid prototyping and iteration of designs. Design changes can be quickly incorporated into the foam pattern, enabling faster development cycles and reducing time-to-market for new products.
8. Artistic and Sculptural Applications:
- Lost foam casting is also embraced in artistic and sculptural applications, where the process allows artists and designers to translate their creative visions into intricate metal artworks.
Lost foam casting’s ability to create complex shapes with ease makes it a favored choice in various industries, including automotive, aerospace, art, and architecture. It enables manufacturers and designers to achieve innovative designs and intricate components that were previously challenging or costly to produce using traditional casting methods.