Custom sand casting allows manufacturers to tailor the designs of cast parts to meet specific requirements and address unique application needs. This process enables the production of components with precise geometries, materials, and performance characteristics. Here are the key aspects of custom sand casting:
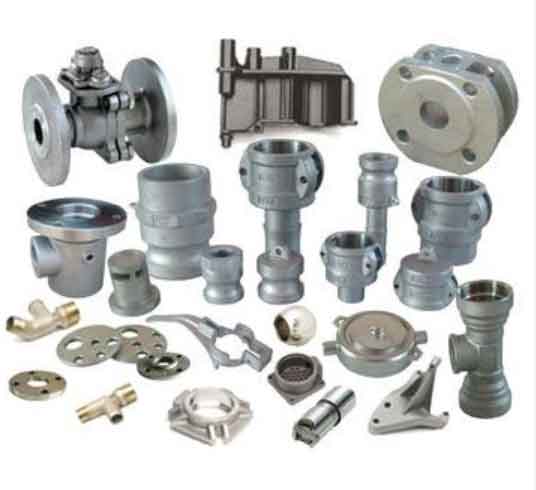
- Design Flexibility: Custom sand casting provides design flexibility, allowing engineers to create complex and intricate shapes that may be difficult or costly to achieve using other manufacturing methods.
- Material Selection: Manufacturers can choose from a wide range of materials for custom sand casting, including various alloys of aluminum, steel, bronze, brass, and more. Material selection can be optimized based on the mechanical properties, corrosion resistance, and other performance requirements of the final part.
- Tolerance Control: Custom sand casting allows for tight tolerance control, ensuring that the finished parts meet the required specifications.
- Weight Optimization: Engineers can optimize the design to reduce material usage and minimize the weight of the component while maintaining structural integrity.
- Prototyping and Iteration: Sand casting facilitates the rapid prototyping of custom parts, allowing for testing and refinement before proceeding with large-scale production.
- Volume Flexibility: Sand casting is well-suited for both small-batch and large-scale production, making it versatile for meeting various production volume requirements.
- Cost-Effectiveness: Custom sand casting can offer cost advantages, especially for low to medium-volume production, compared to other manufacturing methods like die casting or investment casting.
- Short Lead Times: The sand casting process can have relatively short lead times, making it suitable for time-sensitive projects.
- Integration of Inserts and Cores: Inserts and cores can be incorporated into the mold to create internal features, threaded holes, and intricate shapes within the casting.
- Surface Finish Options: Custom sand casting allows for different surface finish options, including shot blasting, grinding, polishing, and painting, to meet specific aesthetic and functional requirements.
- Quality Assurance: Custom sand casting includes rigorous quality control measures to ensure the final parts meet the required quality and performance standards.
- End-Use Applications: Custom sand casting is widely used in various industries, including automotive, aerospace, industrial machinery, defense, and more, to produce components for critical applications.
Custom sand casting is a versatile and effective manufacturing process that offers a wide range of possibilities for producing tailor-made components with precise specifications and performance characteristics. It empowers manufacturers to address unique application requirements and create solutions that match their specific needs.