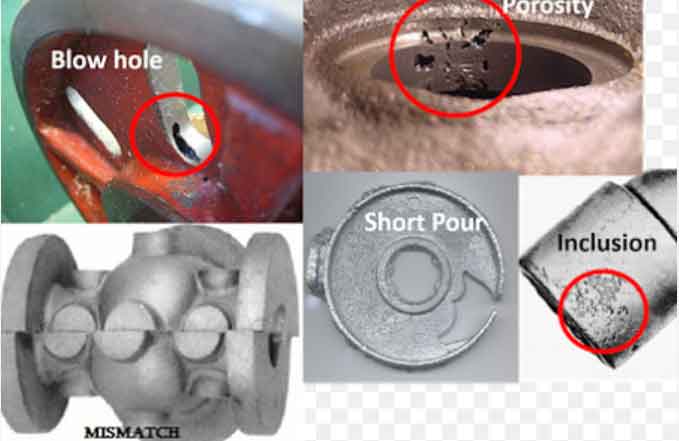
Defect analysis is a crucial step in improving the quality of metal castings. By employing a systematic approach, manufacturers can identify the root causes of defects, develop effective solutions, and prevent their recurrence. This article presents a systematic approach to defect analysis in metal castings, guiding manufacturers through the problem-solving process.
- Defect Identification:
- Visual Inspection: Conduct a thorough visual inspection of the casting to identify visible defects such as porosity, cracks, surface roughness, or dimensional variations.
- Non-Destructive Testing (NDT): Utilize NDT techniques, including radiography, ultrasonic testing, magnetic particle inspection, or dye penetrant testing, to detect internal defects like inclusions, voids, or discontinuities without damaging the casting.
- Historical Data: Review past defect records to identify recurring issues or trends that may indicate common causes.
- Defect Classification:
- Categorize defects based on their type, location, severity, and frequency. This classification helps prioritize the analysis and allocate resources effectively.
- Common defect categories include porosity, shrinkage, gas defects, dimensional variations, surface defects, and internal discontinuities.
- Root Cause Analysis:
- Gather Data: Collect data on process parameters, material properties, mold design, gating system, environmental conditions, and any other relevant factors.
- Fishbone Diagram: Use a fishbone diagram (Ishikawa diagram) to visually map out potential causes of defects across categories such as manpower, machine, material, method, measurement, and environment.
- 5 Whys: Apply the “5 Whys” technique to dig deeper into the causes by repeatedly asking “why” until the root cause is identified.
- Statistical Analysis: Utilize statistical methods such as Pareto analysis, hypothesis testing, or design of experiments (DOE) to analyze data and identify significant factors contributing to the defects.
- Solution Development:
- Brainstorming: Engage cross-functional teams to generate ideas and potential solutions to address the identified root causes.
- Prioritization: Evaluate and prioritize potential solutions based on their feasibility, effectiveness, and impact on defect prevention.
- Process Optimization: Implement changes to process parameters, gating systems, mold design, or material control to eliminate or minimize the root causes of defects.
- Design Modifications: Make necessary modifications to the casting design, including the shape, thickness, or section transitions, to mitigate casting defects.
- Training and Standardization: Provide training programs to improve skills and knowledge, establish standard operating procedures, and ensure consistent and reliable production practices.
- Verification and Continuous Improvement:
- Implement the proposed solutions and monitor their effectiveness.
- Conduct testing, inspection, and analysis to verify the impact of the implemented changes.
- Continuously review and analyze defect data to identify any new trends or emerging issues, facilitating continuous improvement.
Defect analysis in metal castings requires a systematic approach that encompasses defect identification, classification, root cause analysis, solution development, and verification. By following this structured problem-solving process, manufacturers can identify the root causes of defects, implement effective solutions, and prevent their recurrence. Continuous improvement and a proactive approach to defect analysis are essential for enhancing casting quality, reducing costs, and ensuring customer satisfaction.