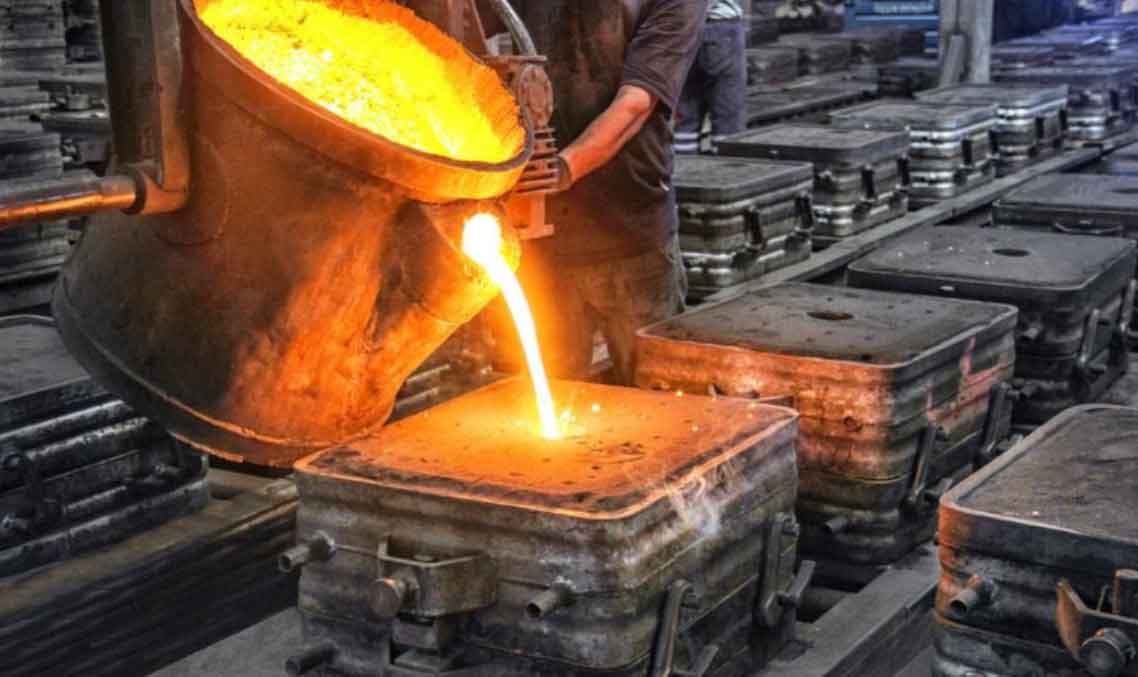
Choosing between sand casting and other casting methods depends on various factors, including the specific requirements of your project, the complexity of the part, the material used, production volume, and budget constraints. Here’s a comparison of sand casting with other common casting methods to help you determine when to choose a sand casting manufacturer:
- Sand Casting:
- Suitable for both simple and complex geometries.
- Versatile and can handle various metals and alloys.
- Cost-effective for low to medium production volumes.
- Ideal for large and heavy parts.
- Can accommodate intricate designs and patterns.
- Longer lead times compared to some other casting methods.
- Good surface finish but may require post-processing for higher precision.
- Generally, higher tooling costs for pattern making.
- Investment Casting (Lost Wax Casting):
- Excellent surface finish and high dimensional accuracy.
- Suitable for intricate and complex parts with fine details.
- Wide range of materials can be used, including ferrous and non-ferrous alloys.
- Lower material wastage due to the disposable nature of ceramic molds.
- Ideal for low to medium production volumes.
- Higher initial tooling costs due to the creation of wax patterns and ceramic molds.
- Die Casting:
- High production rates, making it suitable for large quantities.
- Excellent dimensional accuracy and surface finish.
- Suitable for thin-walled and lightweight parts.
- Ideal for mass production of complex parts.
- Limited to non-ferrous materials like aluminum, zinc, and magnesium.
- High initial tooling costs due to the creation of metal dies.
- Continuous Casting:
- Used primarily for producing long lengths of metal sections or shapes.
- Highly efficient for producing metal bars, rods, and continuous sheets.
- Limited in terms of complexity and design options compared to other methods.
- Typically used for high-volume production.
When to Choose a Sand Casting Manufacturer:
- Sand casting is a favorable choice when you need to produce large, complex parts in relatively low to medium quantities.
- If your project requires the use of a specific material or alloy that is well-suited for sand casting.
- Sand casting is a viable option when cost-effectiveness and versatility are priorities.
- For parts with intricate designs and complex geometries that are not easily achievable through other casting methods.
- Sand casting is a preferred method when you need the flexibility to produce various part sizes and shapes without significant tooling costs.
The choice between sand casting and other casting methods depends on your project’s unique requirements, production volume, material, and budget considerations. Consulting with a reputable sand casting manufacturer and understanding the capabilities of different casting methods can help you make an informed decision.