Direct squeeze casting technology has a short pressure transmission distance because the pressure directly acts on the surface of liquid metal, but the molten liquid must be accurately and quantitatively filled. At the same time, direct squeeze casting is a process of clamping and extruding after filling. For complex shaped parts, there is a process of secondary filling, which is easy to form cold shuts and other defects. Therefore, it is only suitable for producing castings with simple shape and symmetrical structure. Indirect squeeze casting is a kind of metal melt whose pressure is transmitted to the mold cavity through the sprue. Therefore, the pressure transmission distance is long, and shrinkage porosity and other defects are easy to occur. However, indirect squeeze casting is flexible, easy to control the casting size, and does not need to configure an accurate quantitative filling system. Therefore, it is suitable for producing castings with complex shape, uneven wall thickness, high dimensional accuracy and surface roughness requirements. However, this kind of pressing method will not form plastic deformation structure inside the large castings, and the mechanical properties of the castings are slightly lower than those of the castings formed by direct squeeze casting. At the same time, because the indirect squeeze casting process adopts the mold filling system, it is difficult to maintain a high pressure during the casting solidification process, which is not conducive to the production of alloy castings with large solidification range, and the internal quality of the squeeze castings is low; The material utilization rate of indirect squeeze casting is also relatively low.
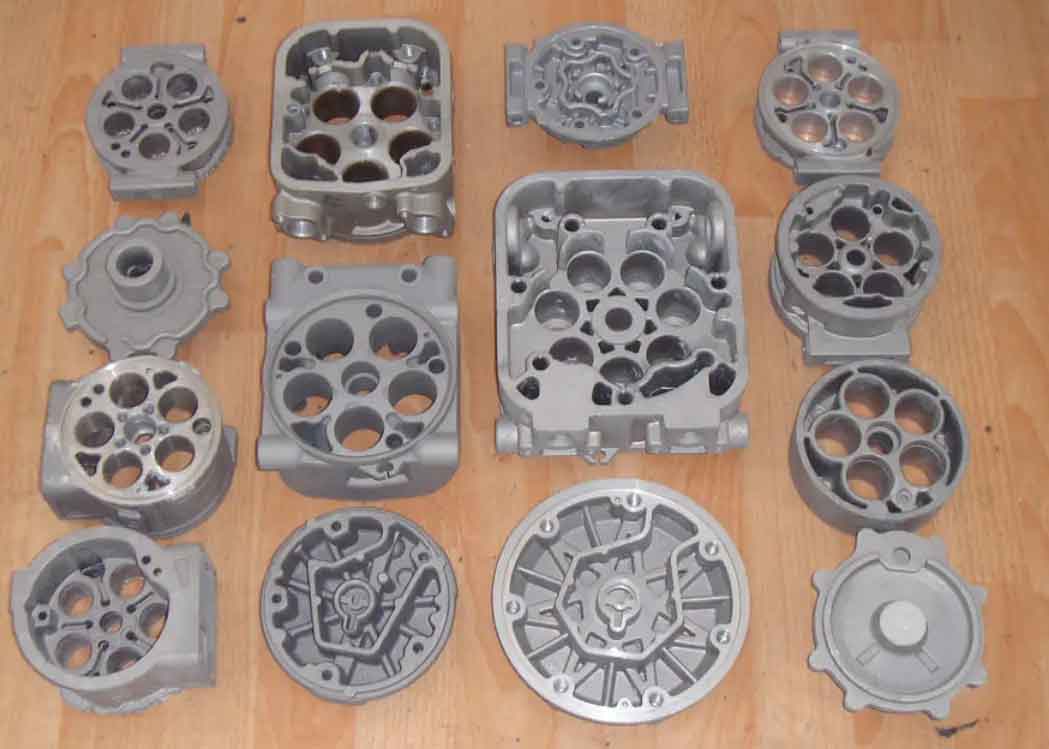
In order to solve the difficult problem of forming large and complex castings, it is necessary to combine the advantages of direct squeeze casting, which has short squeeze force transmission distance and can produce plastic deformation structure inside the castings, with the advantages of indirect squeeze casting, which is suitable for forming complex parts, and put forward a new squeeze casting method. Through the analysis and comparison of squeeze casting technology, a new squeeze casting method, compound squeeze casting, was put forward. In this method, an independent mold filling device is used to fill the mold in the pre closed state of the mold, and then the upper mold of the mold applies pressure on the molten metal until the casting solidifies. The molten metal is in a closed state in the whole process.