The characteristics of compound squeeze casting die for large parts are as follows: only one cavity is set in one set of die, that is, only one casting is produced at a time; No gating system; Set the shunting cone to make the large volume molten liquid flow smoothly during mold filling. According to the design basis and the characteristics of the forming die, the design steps of the composite squeeze casting forming die are determined as follows: (1) process analysis is carried out according to the product drawings, material requirements and technical conditions of large parts to judge whether it is suitable for the composite squeeze casting process; (2) Determine the placement mode of the casting in the mold cavity and set the parting surface; (3) Design splitter cone and exhaust overflow system; (4) Ejection mechanism design; (5) The mold base, heating system and cooling system are designed according to the specifications of the compound squeeze casting equipment; (6) Check the relevant dimensions of the connection between the die and the compound squeeze casting equipment, and draw the general assembly drawing and part drawing of the die.
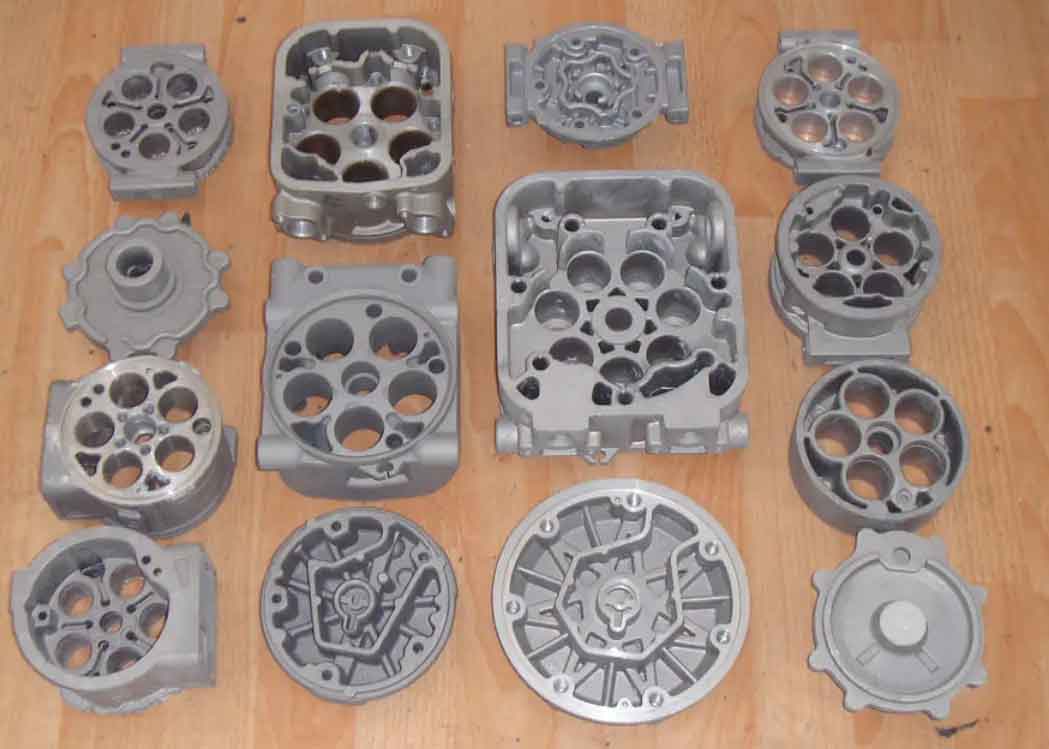
The method to realize the pre closing of the floating rigid support die is to use the side hydraulic cylinder to apply thrust to the moving coil cushion block, so that the spiral surface of the moving coil cushion block is in close contact with the spiral surface of the moving coil, so as to support the moving coil and the upper die by the moving coil cushion block. At the same time, by adjusting the stroke of the piston of the side hydraulic cylinder, the floating height of the moving coil can be realized, and the goal of accurately adjusting the pre closing amount can be achieved. After the mold filling is completed, as long as the pressure of the side hydraulic cylinder is relieved, the quick unlocking can be realized, and the upper die can immediately drive the moving coil to press down stably to squeeze the molten metal. After the metal melt solidifies, the upper die goes up, and the side hydraulic cylinder again applies thrust to the moving coil cushion block to push the moving coil to float to the set height.
In the process that the upper die drives the moving ring to press down, the moving ring will generate certain friction to the molten metal. At the same time, because the moving ring has a draft angle, it will also have a certain extrusion effect on the molten metal. In addition, in the process of moving ring downward, it is equivalent to that the lower die also extrudes the molten metal, which is conducive to increasing the extrusion effect and refining the casting grains.
The compound squeeze casting system is a quantitative problem of metal melt transportation by means of air pressure transportation. However, due to certain errors in the air pressure control device, it is necessary to further fine tune the melt volume through the simultaneous action of the passive pressing function of the filling head in the filling cavity and the overflow function of the floating die, so as to indirectly realize the quantitative filling of the melt. The specific method is as follows: during the extrusion of the upper die and the moving ring driven by the main hydraulic cylinder, when the pressure on the filling head in the filling cavity does not exceed the pressure on its projected area in the extrusion direction of the die cavity, the filling head is in a static state. At this time, if there is a small amount of excess metal melt, it can flow out through the overflow groove set between the upper die and the moving ring of the floating die; When the pressure on the filling head exceeds the specific pressure of its projected area in the extrusion direction of the mold cavity, the filling head in the filling cavity will automatically retreat, so as to squeeze the excess metal melt into the filling cavity. As long as the volume of molten metal in each mold filling is slightly more than that required by the casting, and at the same time, the pressing amount of the upper mold each time is a fixed value, the quantitative mold filling of molten metal can be realized, so as to give full play to the advantages of direct squeeze casting and indirect squeeze casting.