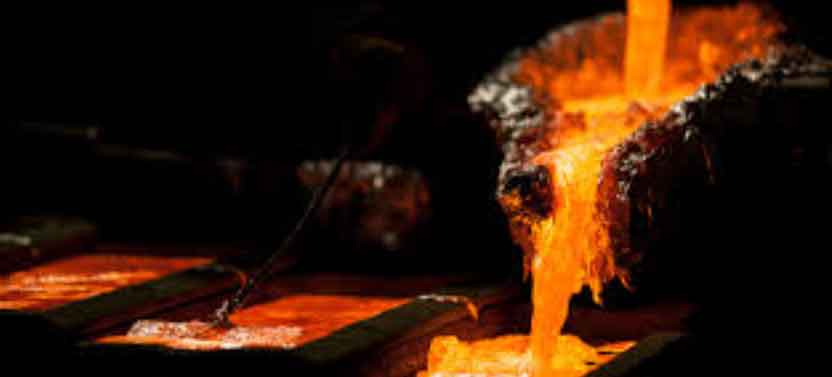
Let’s delve into the steps of the sand casting process in more detail:
1.Pattern Making:
The process begins with the creation of a pattern, which is a replica of the desired object. Skilled pattern makers use various materials such as wood, plastic, or metal to shape the pattern according to the specifications of the final product.
2.Pattern Assembly:
For complex objects, the pattern may consist of multiple pieces that are assembled together. This allows for easy removal from the mold later in the process.
3.Mold Preparation:
A flask, which is a box or frame, is used to contain the sand and mold the pattern. The flask is typically divided into two halves, known as the cope (top) and drag (bottom). The drag is placed on a flat surface, and the pattern is positioned inside it.
4.Sand Mixture:
The sand used in sand casting is a mixture of sand grains and a binder material, such as clay or resin. This mixture, known as green sand, should have good flowability to fill the mold and retain its shape.
5.Sand Ramming:
The cope is placed over the pattern, and the sand mixture is packed or rammed around the pattern and inside the flask. The ramming process ensures that the sand is tightly packed and properly fills the mold cavity.
6.Pattern Removal:
After the sand has been compacted, the cope is lifted, and the pattern is carefully removed from the drag. This leaves behind a negative impression of the pattern in the sand, which will form the mold cavity.
7.Core Placement (if necessary):
If the desired object has internal cavities or complex shapes, sand cores are made separately and positioned in the mold to form the internal features. Cores are typically made of a sand mixture with a binder and are supported by cores prints or other reinforcing structures.
8.Mold Assembly:
The cope and drag are reassembled, aligning the two halves of the mold and ensuring proper registration of the core, if present. The mold is securely closed, often using clamps or other fastening mechanisms.
9.Gating and Venting:
Channels called gates and vents are created in the mold to allow for the flow of molten metal and the escape of gases during the casting process. Gates control the flow of metal into the mold, while vents enable the escape of air and gases.
10.Melting and Pouring:
The mold is prepared for pouring by heating it to remove any residual moisture and improve its refractory properties. Meanwhile, the chosen metal or alloy is melted in a furnace at appropriate temperatures. Once molten, the metal is poured into the mold through the gating system.
11.Solidification:
The molten metal fills the mold cavity and begins to cool and solidify. The cooling rate and solidification time depend on factors such as the type of metal, mold material, and size of the casting. Proper cooling and solidification are essential to achieve a sound casting.
12.Shakeout and Cleaning:
After the metal has solidified and cooled, the mold is broken apart. Mechanical means like vibration, sandblasting, or even water jets are used to remove the sand from the casting. The casting is then separated from the gating and riser systems.
13.Finishing:
The casting may require additional finishing processes to remove any remaining burrs, excess material, or imperfections. These processes can include grinding, sanding, machining, or shot blasting to achieve the desired surface finish and dimensional accuracy.
14.Inspection and Quality Control:
The finished casting is thoroughly inspected to ensure it meets the required specifications and quality standards. Visual inspection, dimensional measurements, and non-destructive testing techniques may be used to identify any defects or deviations.
15.Post-treatment and Assembly:
Depending on the application and requirements, the casting may undergo further treatments such as heat treatment, surface coating, or painting. If multiple castings are needed for the final product, they may be assembled through welding, bolting, or other joining methods.
Each step in the sand casting process requires skill and attention to detail to ensure the production of high-quality castings that meet the desired specifications. It is a versatile and widely used method for shaping metal objects, offering flexibility in design and material selection.