1. Sand core mold design
As shown in Figure 1, the center of the spiral case of sand core I is a circular hollow structure, and the parting surface is a highly gradual spatial complex curved surface. The sand core is formed by a sand blasting machine. Combined with the structure and equipment characteristics of sand core I, the lower mold core 5 of sand core I is designed as a mechanism that can be pried and may return automatically to realize the forming and demoulding of sand core I.
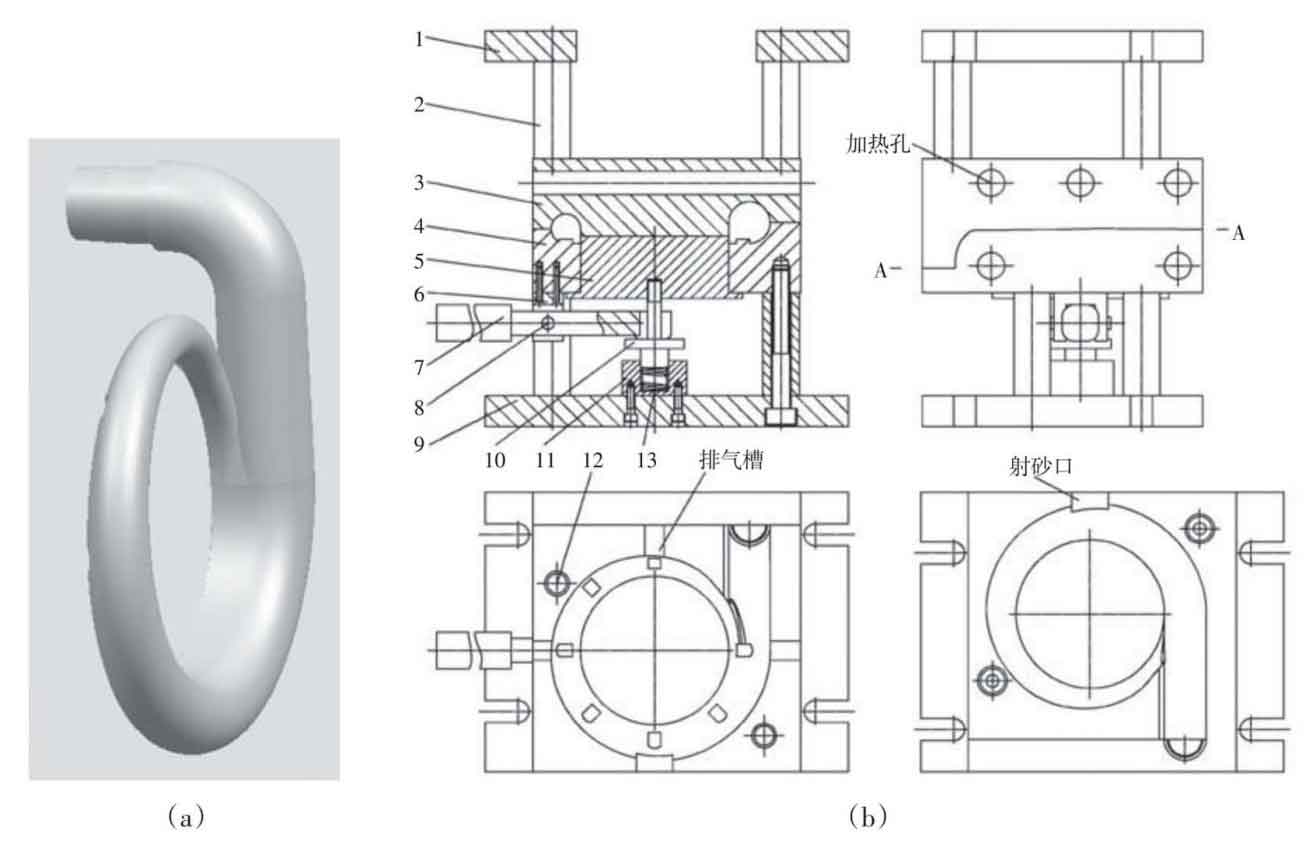
1.Upper base 2. Strut 3. Upper mold 4. Lower mold 5. Lower mold core 6. Mounting base 7. Crowbar
Pin 9. Lower base 10. Ejector rod 1 1. Support 12. Guide post 13. Spring
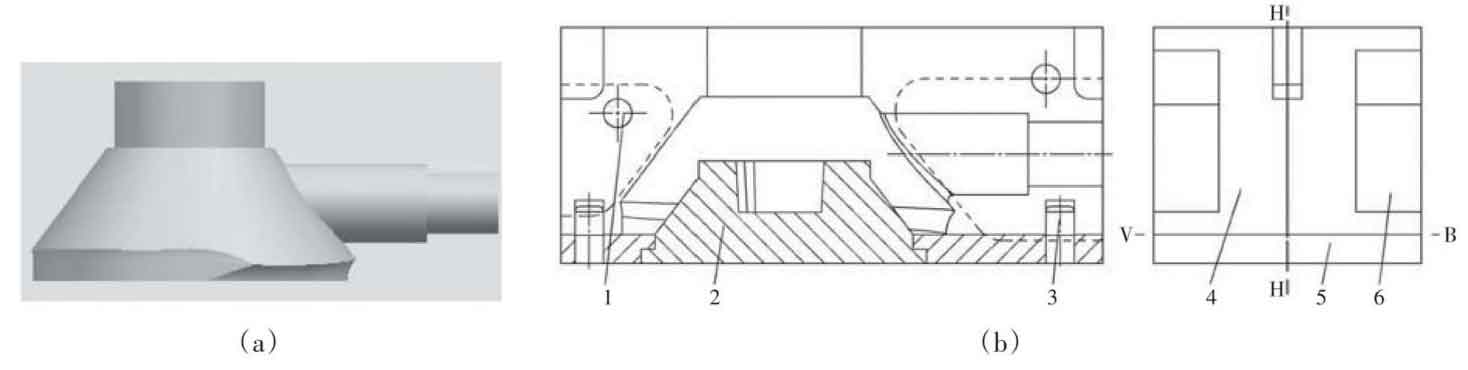
1.Guide post 2. Lower core 3. Guide pin 4. Left die 5. Lower die 6. Right die
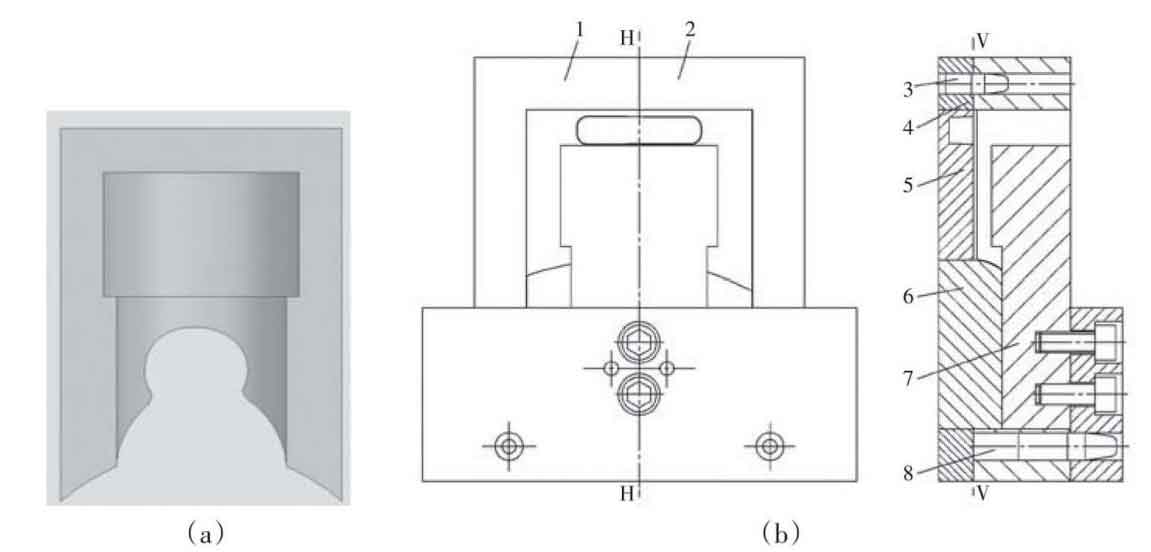
1. Left mold 2. Right mold 3. Guide post 4. Lower mold 5. Mold core 6. Lower mold core 7. Upper mold core
Guide pin
As shown in Figure 2, sand core II is composed of left mold 4, lower mold 5, right mold 6 and lower mold core 2; As shown in Figure 3, sand core III is composed of left mold 1, right mold 2, lower mold 4, lower mold core 5, lower mold core 6 and upper mold core 7. Sand core II and sand core III are formed by manual mold. In order to facilitate mold opening, the molds are divided in both horizontal and vertical directions.
2. Working process of sand core mold
As shown in Figure 1, the sand core I is formed on the sand blasting machine with a mold. Firstly, a heating rod is inserted into the heating hole. After the mold is preheated, furan resin sand is injected into the mold cavity from the sand injection hole in the mold closing state. During the molding process, the gas in the mold cavity and the gas generated in the hardening process are discharged from the exhaust slot. After the furan resin sand is thermally hardened, the hydraulic system of the sand ejector separates the upper mold 3 from the lower mold 4, and the sand core I remains in the lower mold, Pull the crowbar 7 to make the lower mold core 5 retreat. After loosening the sand core I wrapped in the lower mold core 5, take out the sand core I. then, under the action of the rebound force of the spring 13, the lower mold core 5 automatically returns and clings to the limit surface of the lower mold 4. When the upper mold 3 and the lower mold 4 are closed, a sand core forming cavity is formed.
As shown in Fig. 2 and Fig. 3, the sand core II and sand core III are small. They are prepared and formed by manual molding. The upper / lower and left / right structures of the mold are accurately positioned under the guidance of the guide column and guide pin. After closing the mold, furan resin sand is injected from the upper opening. After pressing and filling, the mold is put into the oven for baking. After the furan resin sand is heated and hardened, take out the mold and separate the upper / lower and left / right molds, Remove the sand core.
The casting of turbine cover adopts sand casting, and its forming process mainly includes modeling, core making, drying, mold closing, pouring, sand dropping, cleaning and inspection. Firstly, according to a certain proportion of molding materials, the molding sand conforming to the molding and the core sand conforming to the core making are obtained respectively; Using molding sand, pattern, false box and other process equipment, the box molding is carried out manually to obtain the sand mold with pouring and riser system and casting shape cavity; Core sand and sand mold are used for core making and drying by machine and hand; Place the external cooling iron, metal core, sand core III, sand core II and sand core I in sequence, and close the sand mold layer by layer to form a mold cavity between the sand mold, sand core and metal core. The liquid metal fills the mold cavity of the whole mold by gravity through the gating system in the mold, and feeds the hot joint of the casting through riser, external cooling iron and metal core to eliminate casting defects, After cooling and forming, carry out sand dropping, clean the casting, remove the pouring riser, obtain the casting blank of turbine cover and conduct inspection.