Casting Name: 105 type cable head; material: ZG310-570; geometric dimension: 620 mm × 290 mm × 210 mm; single piece weight 107 kg; wall thickness uniform 50 mm, bridge cable suspension device, security parts; material must meet the requirements of the drawing, mechanical properties must meet the standard, no casting defects are allowed in NDT.
1. Foam model making
The molding of polystyrene bead can increase the density of the foam to improve the surface quality of the castings. The foam density of this case is 26 g/L (Fig. 1).
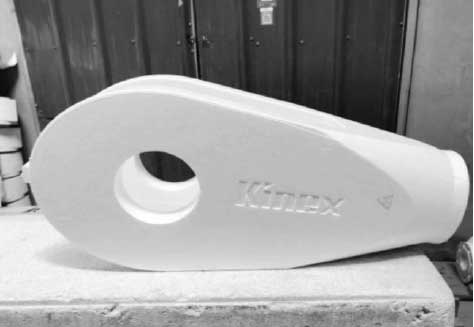
2. Design of gating and riser
After the process test is successful, the risers are molded by the mold, and the products are saved, saved and bonded. The gate size is 175 mm x 270 mm, riser size is 160 mm 110 mm x 130 mm, and the foam Flaping seam is carefully repaired before the gating system is assembled. The position of poor bead integration is repaired with repair paste (Fig. 2).
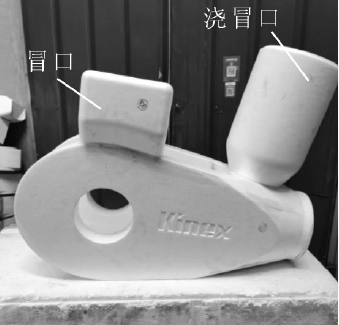
3. Coating hanging
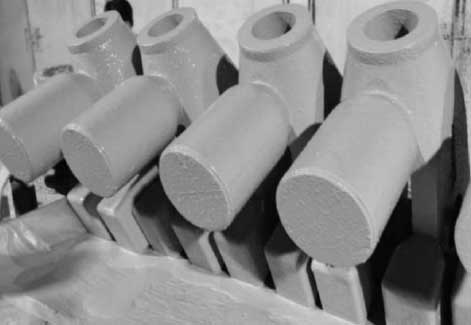
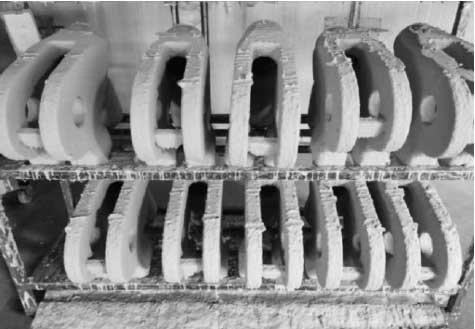
The coating in contact with liquid steel is called “process layer”. It needs fine and high-grade aggregate (Fig. 3) and its thickness is 2.0-3.0 mm. In order to improve the coating strength, the coating layer needs to be wrapped outside the process layer, and low-grade refractory aggregate can be used to prepare, which can reduce the cost of some coatings. The coating thickness is controlled according to the casting size. The fundamental difference between the coating of hollow shell casting process and ordinary EPC is that it is not necessary to apply the next layer of coating after the coating is completely dry, and the next layer of coating can be applied after it is dried (Fig 4) For example, the hot melt adhesive will melt and lose the bond strength when baking in the kiln. When the pouring riser and the casting body are connected, even if the hot melt glue is melted and the refractory cloth is connected, the enough strength can be ensured (Fig. 5).
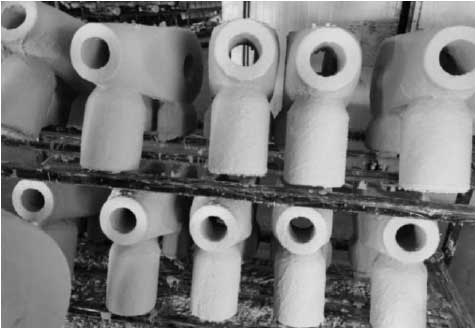