4.Baking of coating shell
The baking of coating shell is the key link of the process. In the process of roasting, the discharge of combustible materials should be reduced as much as possible to avoid environmental pollution, The calcination of shell is divided into two stages: low temperature glue discharging and high temperature firing. The high temperature section not only makes the residual foam in the low-temperature section completely vaporized, but also improves the strength of the coating shell.
4.1 before entering the kiln, the rubber discharging channel should be opened first
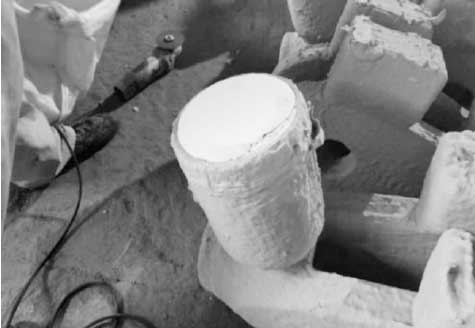
Fig. 1 the toothless saw cuts off the coating cover, and the upper frame of the model is placed with the mouth downward to make the rubber outlet; FIG. 2 drilling holes on the riser to make an auxiliary rubber drainage channel.
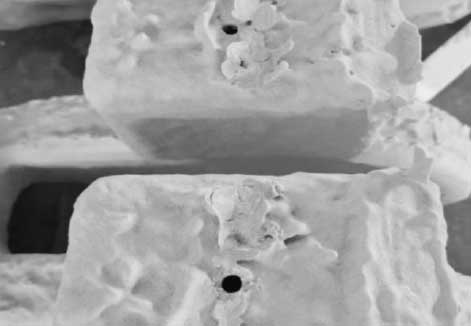
4.2 low temperature tapping
Fig. 3 the kiln rack on the model; Figure 4 put up the adhesive plate; Figure 5 kiln car enters the kiln; the temperature rises to the foam liquefaction point, causes the foam to become the liquid to exclude the cavity; Figure 6, Figure 7 opens the kiln to remove the foam gum.
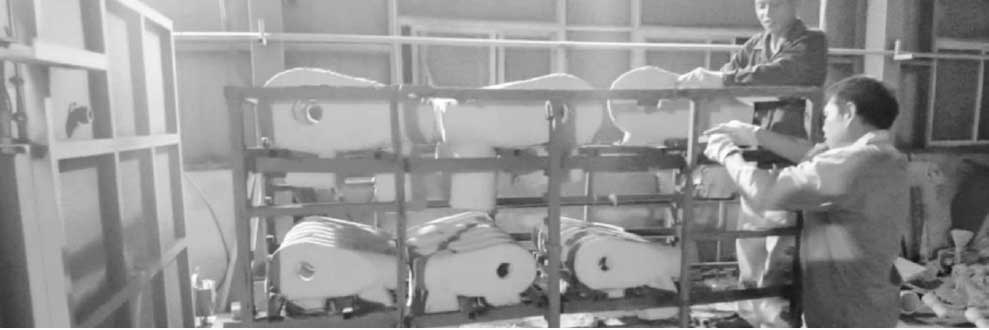
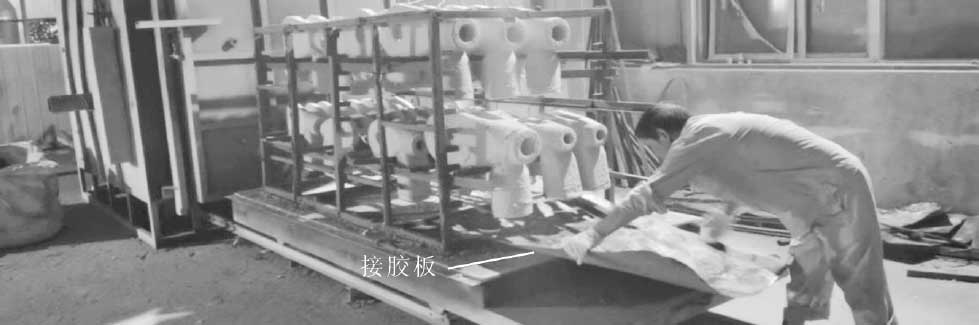
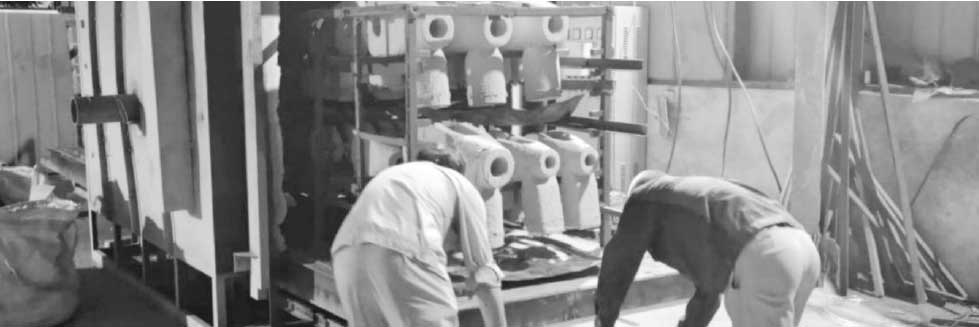
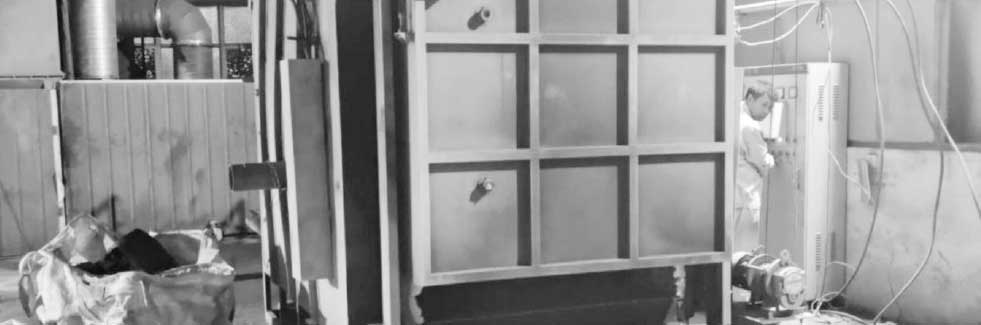
4.3 high temperature shell burning and kiln discharging
After the kiln temperature reaches the required temperature, the kiln door can be raised for a period of time to make the model shell cool down rapidly; FIG. 8 shows that the kiln car is out of the kiln after cooling down; while the kiln car continues to cool down, the next kiln car can be preheated in the kiln.
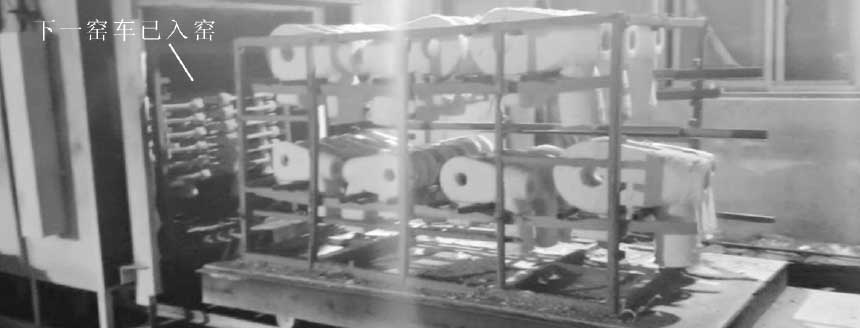
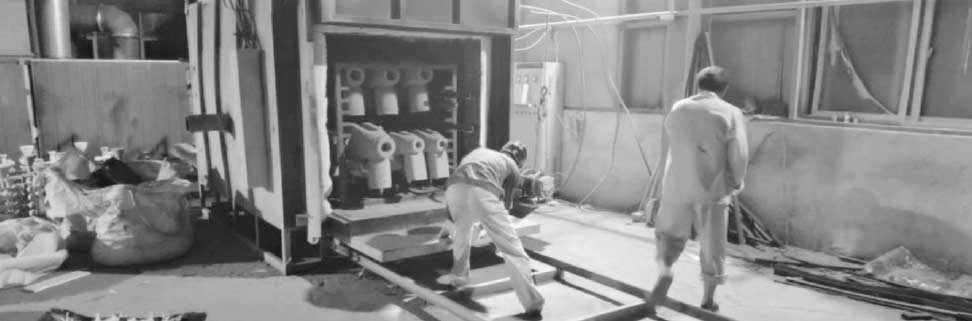
