Production conditions, structure and technical requirements of fixture
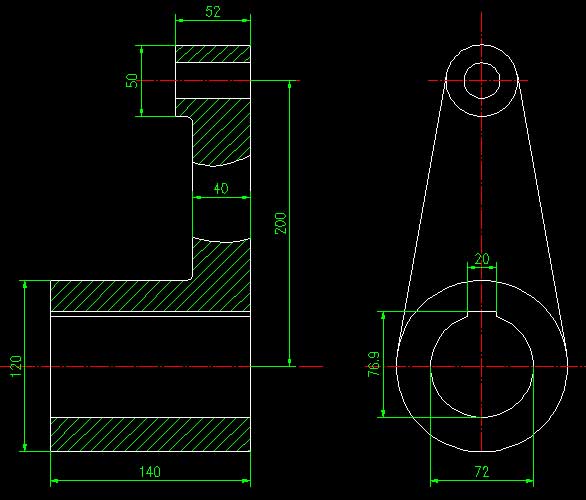
Product production nature – mass production
Part material – 35Cr
The part drawing of the fixture is shown in Figure 2.2. The overall outline dimension of the fixture is 285mm * 120mm * 140mm, and the main wall thickness is 40mm, which is a small casting. The casting meets the requirements of geometric dimension accuracy and material quality, but there are no other special technical requirements.
Casting technology of fixture structure
The casting process of part structure means that the structure of the part should meet the requirements of casting production, which is easy to ensure the quality of the casting, simplify the casting process and reduce the cost. The review and analysis shall consider the following aspects:
1.The casting shall have appropriate wall thickness. In order to avoid defects such as pouring failure and cold insulation, the casting shall not be too thin.
2.The casting structure shall not cause serious shrinkage obstruction. Attention shall be paid to the connection of thin-wall transition and thin thick wall of fillet casting. The form of gradual transition and transformation shall be adopted for the connection of wall and wall with thickness such as turning. Larger fillet shall be used for connection to avoid crack defects caused by stress concentration.
3.The inner wall of the casting shall be thinner than the inner wall and rib of the outer wall casting. The heat dissipation condition is poor, and the inner wall shall be thinner than the outer wall so that the inner wall and the outer wall can be cooled evenly, the internal stress can be reduced and the crack can be prevented.
4.The wall thickness shall be uniform as far as possible, and the fat part shall be reduced to prevent the formation of hot spots.
5.It is conducive to feeding and sequential solidification.
6.Prevent the casting from warping and deformation.
7.Avoid horizontal large plane structure at the pouring position.
Selection of molding and core making methods
The outline size of the support is 285mm * 140mm * 120mm, and the casting size is small. It belongs to small and medium-sized parts and needs large-scale production. It is easy to organize flow production, realize mechanization and automation, reduce material cost, save drying equipment, fuel, power, etc., and extend the service life of sand box. Therefore, it is reasonable to adopt the wet clay sand machine modeling and the metal mold for the pattern.
In the selection of materials and methods for core making, for example, the cost of making sand core with clay sand is low, but it is easy to crack and deform after drying. Under the condition of mass production, because of the need to improve the core making efficiency and the high dimensional accuracy of the core, the core required by this process is produced by the hot box method to increase its strength and ensure the casting quality. The core shooting process is selected to produce sand core.
Determination of pouring position
The pouring position of casting refers to the state and position of casting in the mold during pouring. Determining the pouring position is an important link in the casting process design, which is related to the internal quality of the casting, the dimensional accuracy of the casting and the difficulty of the molding process.
Attention shall be paid to the following principles when determining the pouring position:
1.The important part of the casting shall be placed at the bottom as far as possible
2.The important machining surface shall be downward or upright
3.Make the answer plane of the casting face down to avoid internal defects caused by sand inclusion and scarring
4.The casting shall be fully filled
5.It should be conducive to the feeding of castings
6.Avoid hanging sand, hanging core or cantilever sand core, which is convenient for core lowering, box closing and inspection.
Determination of parting surface
Parting surface refers to the surface on which two half molds contact each other. The quality of parting surface affects the dimensional accuracy, cost and productivity of castings to a great extent.
The following principles should be paid attention to when selecting parting surface:
1.All or most of the castings shall be placed in the same half mold
2.The number of parting surfaces shall be minimized
3.The parting surface shall be plane as far as possible
4.Easy to lower core, close box and test
5.Do not make the sand box too high
6.The selection of parting surface of stressed parts shall not weaken the structural strength of castings
7.Pay attention to reduce the amount of casting cleaning and machining