The main function of the squeeze casting die in the forming process is to complete the liquid metal forming, to ensure the forming accuracy and part performance index. Due to the technical details involved, there are few related documents abroad. However, the design of squeeze casting die has been improved continuously in China, and the references that have reference value for the design of large-scale part squeeze casting die are mainly reflected in the following aspects: the floating structure of die, the improvement of quantitative filling accuracy through die and the enhancement of extrusion effect and the improvement of part performance through die structure [.
The floating die structure can realize up and down pressure at the same time or from the radial pressure to increase the extrusion effect. Yan Desheng and others use the floating structure (as shown in the figure) As shown in the figure), the bearing cover casting can be pressurized up and down at the same time to improve the performance of the product; Han Zhiqiang, etc. can generate radial pressure on the inner ring of the cylinder liner through the mandrel with cone surface by using the floating lower die (as shown in the figure). The characteristics of these two patents are that two or more springs are used to support the floating structure. However, in actual production, due to the stiffness error of the spring itself and the change of the elastic coefficient under different temperatures, the elastic support force is uneven, which leads to higher requirements for the guiding accuracy of the floating structure. When the casting is large, it is difficult to ensure the smooth movement. Therefore, in the design of large-scale die, we can use floating structure for reference to improve the elastic support.
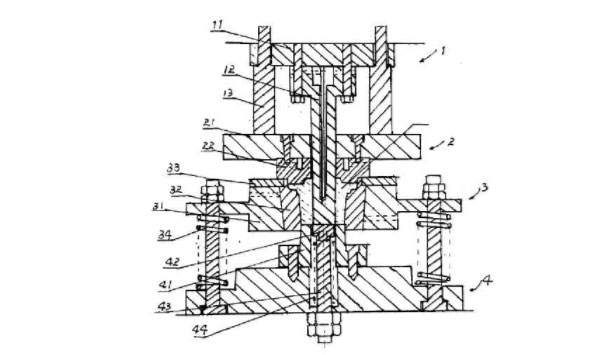
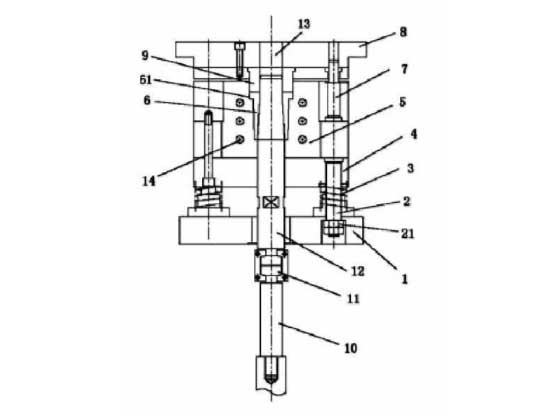
The hydraulic floating mold adopts the form of lower hydraulic cylinder to support the floating structure, as shown in the figure. The demoulding process of the structure and the design of the oil circuit of the lower hydraulic cylinder are more complex. In the process of extrusion, it is necessary to accurately ensure the action coordination of the upper die, the floating structure and the lower hydraulic cylinder.
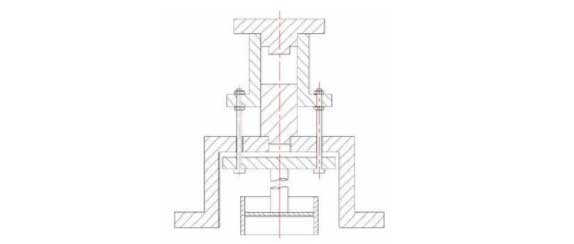
In terms of improving the precision of quantitative filling, Gaoming lamp, etc. invented an extrusion die structure (as shown in the figure) with overflow channel and overflow cavity. The die is provided with overflow channel and overflow cavity at the position corresponding to the highest position of the part. Because the overflow scheme is adopted, by determining the distance between the overflow channel and the highest point of the part, the excess metal liquid can flow into the overflow cavity to realize the quantitative filling and forming of the metal liquid of the part, so as to achieve the near net forming of the part. The mold can relax the operator’s control of the filling amount of liquid metal. It has the effects of reducing human factors, saving equipment investment, improving production efficiency, reducing physical labor and reducing manufacturing cost. It is suitable for small batch production and trial production.
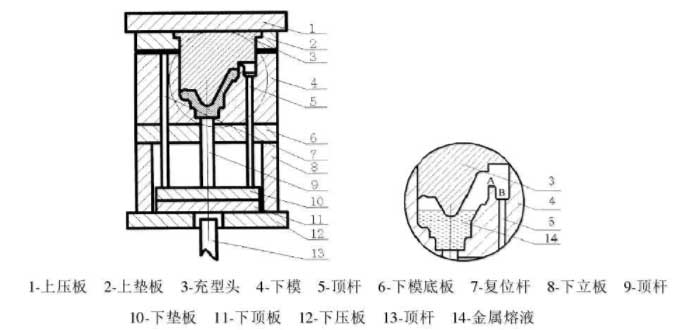
A kind of squeeze casting die structure (as shown in the figure) with local pressurization is invented. A pressurization system consisting of a pressurization channel, a pressurization punch and a pressurization cylinder is arranged at the thick wall hot spot of the casting on one side of the casting cavity. The pressurization system and the extruding piston are controlled in real time through the circuit system. By controlling the cross-sectional area, the pressurization distance and the pressurization starting time of the pressurization punch, pressurization is realized The liquid metal in the channel is fed into the hot spot of the thick wall of the casting to avoid the casting problem of loose shrinkage cavity in the thick wall, improve the density of the structure in the whole casting, so as to improve the quality of the casting and reduce the rejection rate.
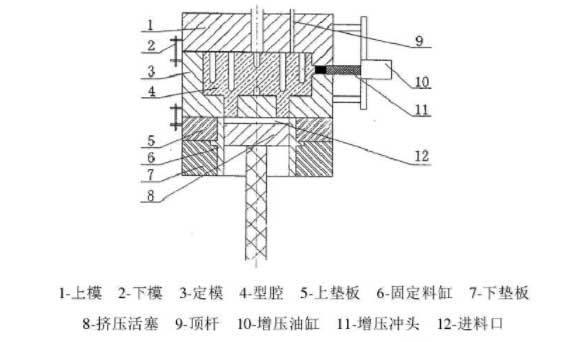
A die structure (as shown in the figure) which can realize multiple extrusion is invented. A sliding fit of δ gap is formed between each extrusion punch and a moving die or a fixed die, and the extrusion punch is connected with a die locking mechanism. Under the die locking state, each extrusion punch has a forging amount of H distance, which can realize multiple directions, multiple extrusion, and double extrusion at the same time. Because the molten metal solidifies quickly in the mold cavity, the second extrusion process is equivalent to forging, so a large pressure is needed.

The design and manufacture of the die for the composite squeeze casting of large parts is also a very important research content of this paper. In this paper, a large hub with a single weight of about 60kg is selected as the forming test piece, and the design and manufacture of a mold that meets the forming requirements is an important prerequisite to achieve the research goal of this paper.