Parting surface refers to the contact surface of each casting mold which is divided into several segments. In practical production, due to the limitation of casting structure and equipment capacity, mold modeling is often carried out in sections, and then a complete mold is formed through mold assembly, and each contact surface forms a parting surface. In process design and actual production, parting surface and pouring position are considered and determined at the same time. The determination of parting surface and pouring position have the same influence on the final casting, which not only directly determines the overall quality and dimensional accuracy of the casting, but also is one of the important factors that determine the difficulty of molding operation and production efficiency. In general, the determination of parting surface needs to consider the important size requirements of castings, mold draft angle, operation method and key structure with high casting difficulty. When determining the parting surface of intake cylinder, the following principles should be considered comprehensively
(1) It is convenient for core making, core setting, forming and dimension checking.
The complex cavity structure of the inlet cylinder casting determines that most of the casting surface and chamber structure must be formed by core assembly. Preliminary analysis shows that the number of sand cores is close to 20, and the casting size is basically achieved by the relative positioning size control between sand cores and sand cores. Although the positioning core head can be set in the lower mold, there is a gap between the core heads and the sand core precision of manual core making is not high. In the process of core setting and mold closing, the size of each part should be checked and the position of sand core should be adjusted to ensure that the size of each part can meet the requirements of casting wall thickness.
(2) All castings are preferred to be placed in the same mold.
One of the main purposes of determining the parting surface is to facilitate the mold demoulding smoothly after molding. If the mold is not fully considered or set improperly, the displacement or position deviation between the two molds in the mold closing process will have a significant impact on the casting accuracy. The thickness of parting surface will increase the size deviation of casting after mold closing, which requires the minimum thickness of parting surface. In order to avoid the influence of parting surface on the dimensional accuracy of the important position of the intake cylinder casting, the whole assembly accuracy requirement is high, the processing datum plane and the important mold line surface are placed in the same medium-sized mold, and are not crossed by the parting surface. The parting surface is placed on the upper and lower end faces of the casting, which is divided into upper, middle and lower mold. The lower mold is mainly the core head positioning and gating system for core assembly. Almost all sand cores rely on the positioning core head in the lower mold for dimensional positioning. The medium-sized mold mainly forms the outer contour of the casting, and the casting riser is placed in the upper mold.
(3) Select straight parting surface and minimize the number of parting surface.
The flat parting surface can be molded on the molding plate or template, which is suitable for batch molding with high production efficiency. At the same time, it can also ensure that the parting surface of the two types is smooth and the two sides are closely matched when forming. It is estimated that the hydraulic head of the inlet cylinder is as high as 2500 mm, and the weight of the molten iron is 13500 kg. During pouring, the lifting force of the molten iron on the upper mold and the pressure on the lower mold are very large. At the same time, due to the good fluidity of the ductile iron, the high temperature molten iron will flow out along the gap of the parting surface, resulting in serious fire accident. Choosing straight parting surface and close fitting can effectively prevent fire accident during pouring and simplify the difficulty of manual modeling, which is the optimal scheme for the parting surface selection of inlet cylinder.
(4) It does not weaken the structural strength of castings.
The parting surface determined according to (2) above does not weaken the casting structure.
(5) It is convenient for the cleaning operation of castings with complex chamber structure in the process of sand dropping and tail treatment.
After solidification, a thick layer of fins and fins will be formed on the parting surface, the parting surface and the gap between the core head. For nodular cast iron, it is not allowed to use gas cutting to remove the fleshy. The structure of the inner cavity of the cylinder is relatively complex, and there are many small threading holes. If the flash of parting surface is not convenient for the operation of mechanical cutting tools and grinding tools, it is difficult to remove and clean them. The parting surface of the intake cylinder is selected at the upper end and the air inlet side of the intake side, so as to facilitate the mechanical cutting of the excess flash, and to avoid the inner cavity molding sand and core bone unable to be cleaned due to the formation of closed space after the core head is covered by molten iron.
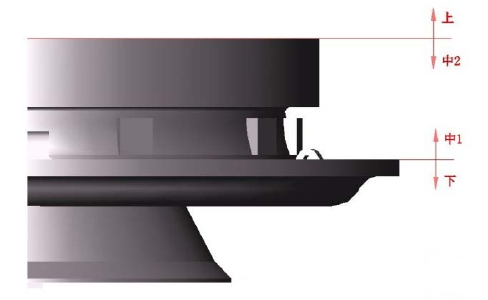
Considering the above factors (1) ~ (5) and combining with relevant practical production experience, the parting surface as shown in the figure is finally selected and determined. Selecting the parting surface is simple and easy to operate in the molding aspect and can ensure the mold quality; in terms of core setting and size guarantee, it is convenient to check and adjust the core setting, core assembly and important size template in the mold; in the aspect of mold closing, it is convenient for cavity cleaning and parting surface anti fire control. The parting scheme can not only facilitate the operation and inspection of molding, core setting, mold closing and casting cleaning, but also effectively avoid the quality problems such as casting size deviation and pouring fire, and fully ensure the physical quality of castings.