In recent years, the development of squeeze casting technology is still inseparable from the theme of improving product quality and expanding the application scope of squeeze casting. The more prominent innovations are as follows.
Double squeeze casting is a developing new process of squeeze casting after “direct extrusion” and “indirect extrusion”. It actually combines the two forms of “direct extrusion” and “indirect extrusion”, forms the blank by indirect extrusion, and compacts the casting by direct extrusion (closed die forging), In order to achieve the goal of compact structure, precise shape and size, and good surface finish, it has developed rapidly in recent years because of its advantages of both direct and indirect extrusion.
The figure is a schematic diagram of double squeeze casting of cup-shaped parts. It is to push the liquid metal poured into the charging cylinder 4 into the cavity composed of the upper die 2 and the middle die 3 of the pre closed locking die and the upper extrusion punch 1 with a certain amount of reduction (H) reserved by the lower extrusion punch 5, and continue to maintain the pressure (this is called the first extrusion). Then, the upper extrusion head 1 downward applies high pressure, That is to say, the second extrusion (forging) is carried out for the castings in solidification until the castings are compacted and completely solidified. At present, there are many names of this process, such as “continuous casting and continuous forging”, “casting and forging two control forming” and “secondary pressure feeding”.
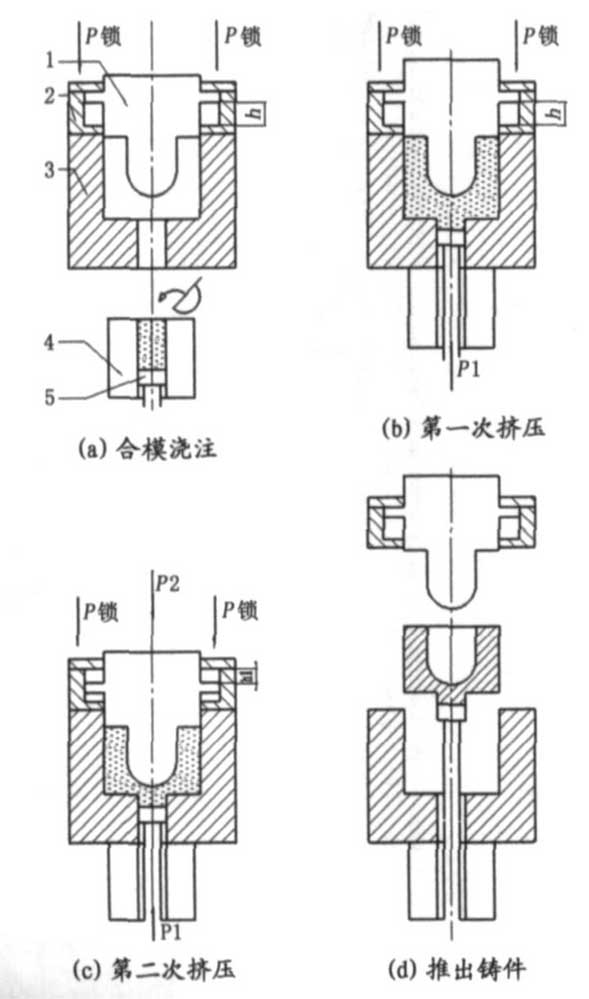
There are many kinds of process forms of double squeeze casting, such as local supplementary pressing, double extrusion with feeding system and double extrusion of magnesium alloy. Fig. 3 is a schematic diagram of the technological process of the production of automobile aluminum wheel hub by local pressure supplement. The second extrusion is mainly carried out in the thick part of the hub center. Using this technology, there are A356 Aluminum gas storage tank parts, American SPX company’s aluminum pump parts and air compressor high silicon aluminum cylinder parts developed by the author. Fig. 4 is the schematic diagram of double extrusion (continuous casting and continuous forging) filled by low-pressure casting.
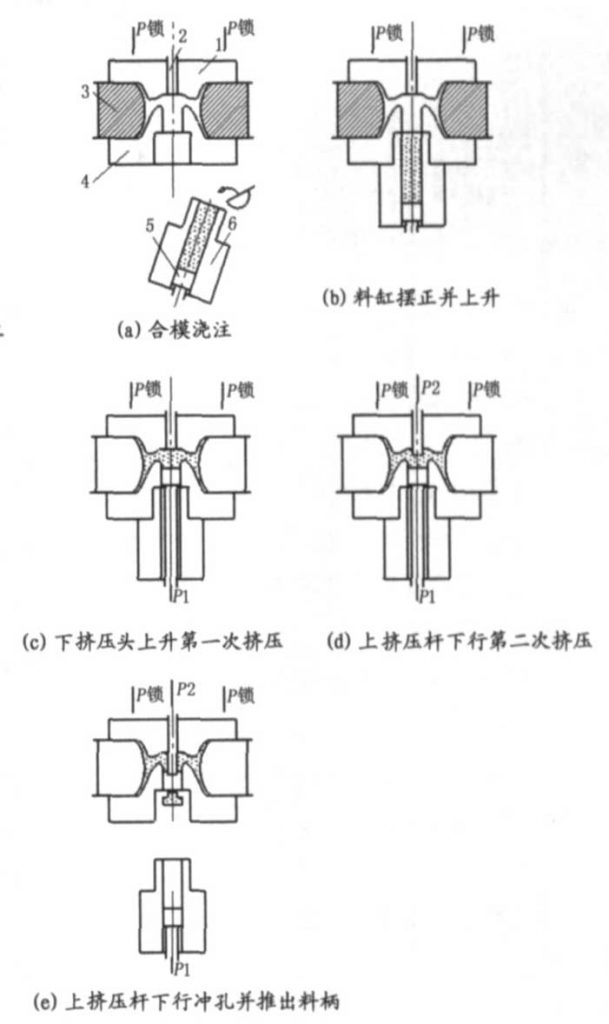
The figure shows a process diagram of double extrusion (casting forging double control forming) of magnesium alloy shell of motorcycle engine. The material used is AZ91D magnesium alloy. In order to meet the above technological requirements, the factory specially designed and manufactured the casting forging double control forming machine.
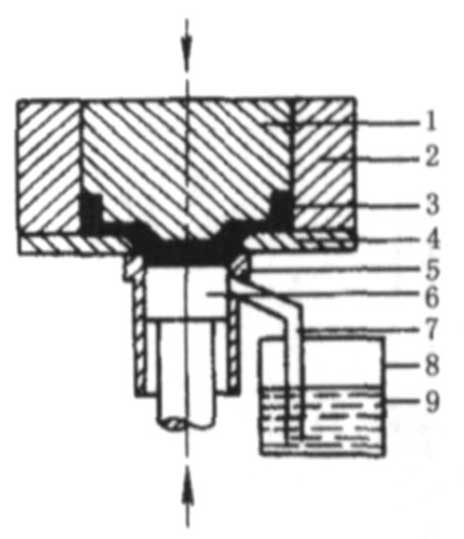
It must be pointed out that in order to carry out double extrusion, the die must be designed to have the functions of pre closing die, locking die and twice extrusion. The squeeze casting equipment must be a hydraulic press with three independently controlled oil cylinders, so that the pre closing die and locking die, the first extrusion and the second extrusion can be realized. This hydraulic press must be controlled by computer (PLC), which can accurately grasp the time interval from pouring to the first extrusion and the second extrusion.
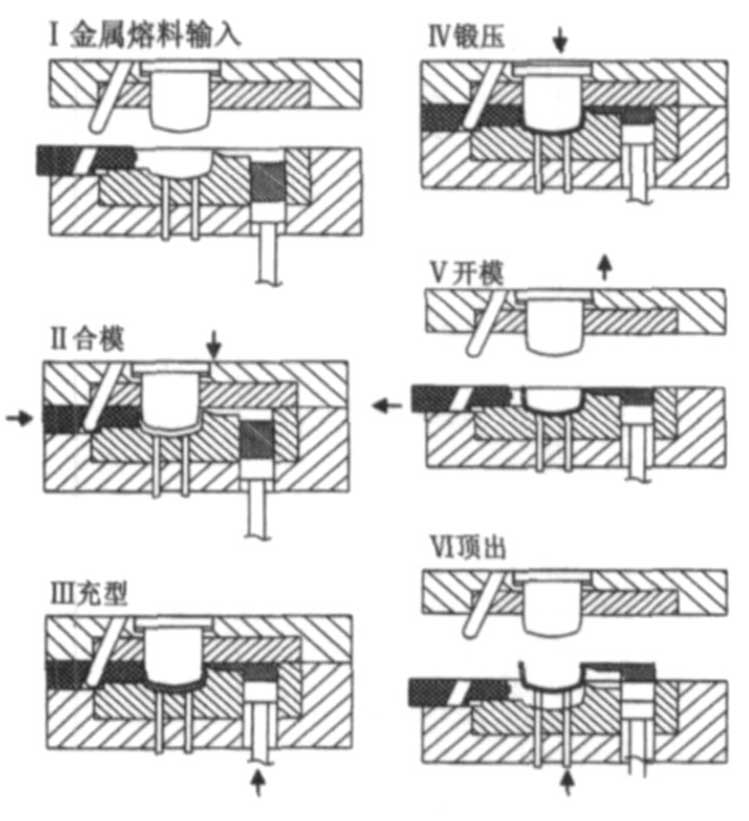
Double extrusion is a new development of squeeze casting. It provides a potential process for the production of complex and high-quality deformed alloy castings.