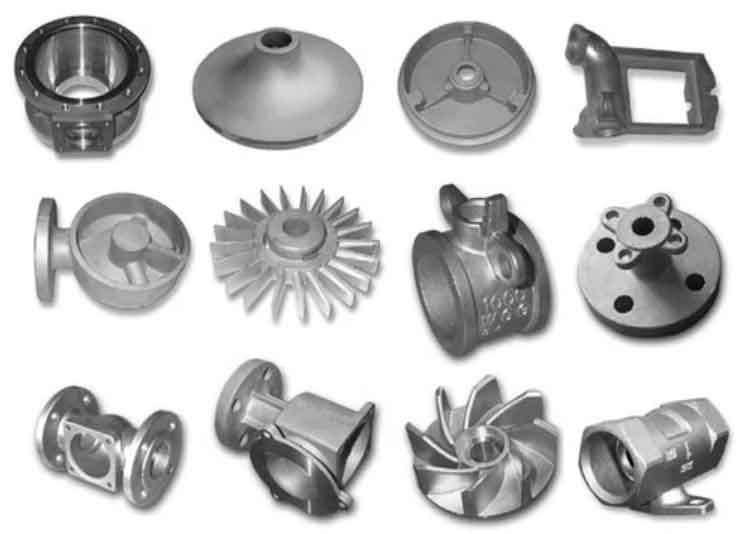
When selecting a casting method for your project, it is crucial to consider the specific requirements, design complexity, production volume, material properties, and other factors. Here’s a comparison between die casting and other common casting methods to help you make an informed decision:
- Die Casting:
- Advantages:
- High production efficiency and fast cycle times, suitable for high-volume production.
- Excellent dimensional accuracy and repeatability.
- Capability to produce complex geometries with intricate details.
- Good surface finish, reducing the need for additional machining or finishing operations.
- Ideal for lightweight components with high strength-to-weight ratios.
- Suitable for a wide range of materials, including aluminum, zinc, magnesium, and copper alloys.
- Limitations:
- Higher tooling and equipment costs compared to other casting methods.
- Limited to relatively small to medium-sized parts due to the size constraints of the die casting machines.
- Not suitable for large and heavy parts with thick sections.
- Advantages:
- Sand Casting:
- Advantages:
- Versatility to produce both small and large-sized parts.
- Lower tooling costs compared to die casting.
- Suitable for a wide range of materials, including ferrous and non-ferrous metals.
- Ideal for producing complex shapes and large components.
- Capable of accommodating design changes easily.
- Limitations:
- Lower dimensional accuracy compared to die casting.
- Slower production rates and longer lead times.
- Requires more finishing operations due to the rougher surface finish.
- Not suitable for producing components with thin walls or intricate details.
- Advantages:
- Investment Casting:
- Advantages:
- Excellent dimensional accuracy and high-quality surface finish.
- Capability to produce complex shapes and intricate details.
- Suitable for a wide range of materials, including ferrous and non-ferrous metals.
- Minimal material waste, as the mold is created using a pattern that is usually made of wax or a similar material.
- Ideal for producing components with thin walls and fine features.
- Limitations:
- Longer production cycles compared to die casting.
- Higher cost per unit compared to other casting methods.
- Limited to relatively small to medium-sized parts.
- Additional steps involved in creating and removing the investment mold.
- Advantages:
Each casting method has its own strengths and limitations, making it suitable for different applications. Die casting is well-suited for high-volume production of complex and dimensionally accurate components, particularly when lightweight and intricate designs are required. Sand casting offers more flexibility for larger parts and design changes. Investment casting is ideal for producing high-quality, intricate components with thin walls.
Consider factors such as production volume, design complexity, dimensional accuracy requirements, material properties, and cost constraints when selecting the appropriate casting method for your project. Consulting with casting experts and conducting thorough feasibility studies can help determine the best approach for your specific needs.