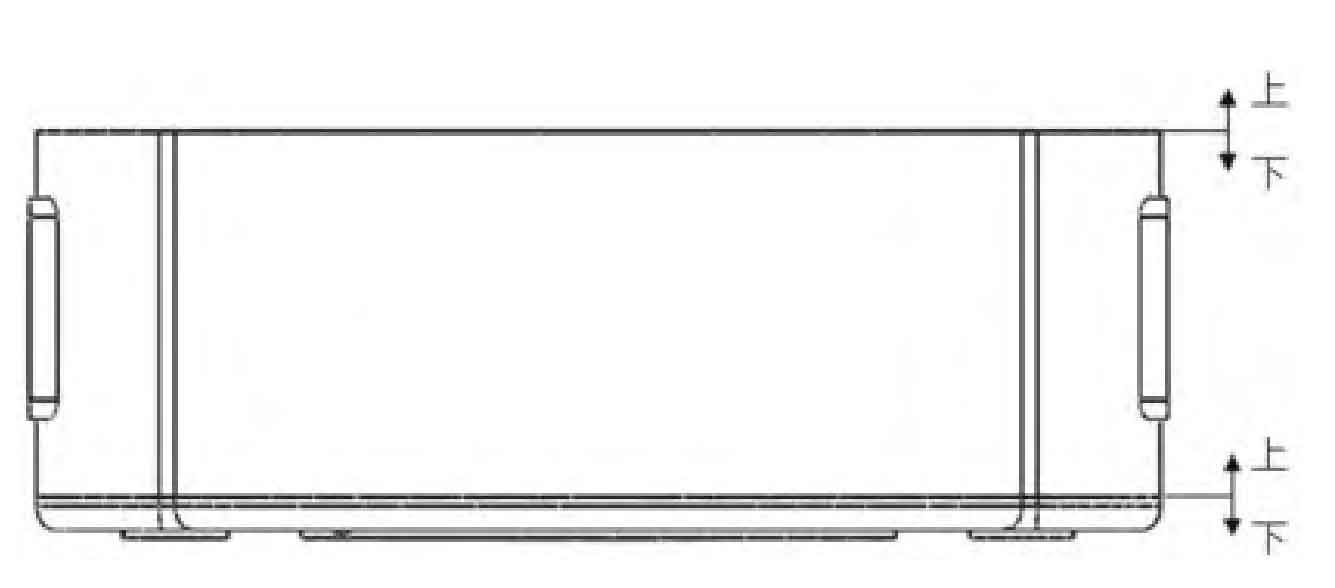
Furan resin sand is used for three box modeling, and the parting method is shown in Figure 1. See Figure 2 for the process design diagram of pouring and riser system.
1. Pouring position
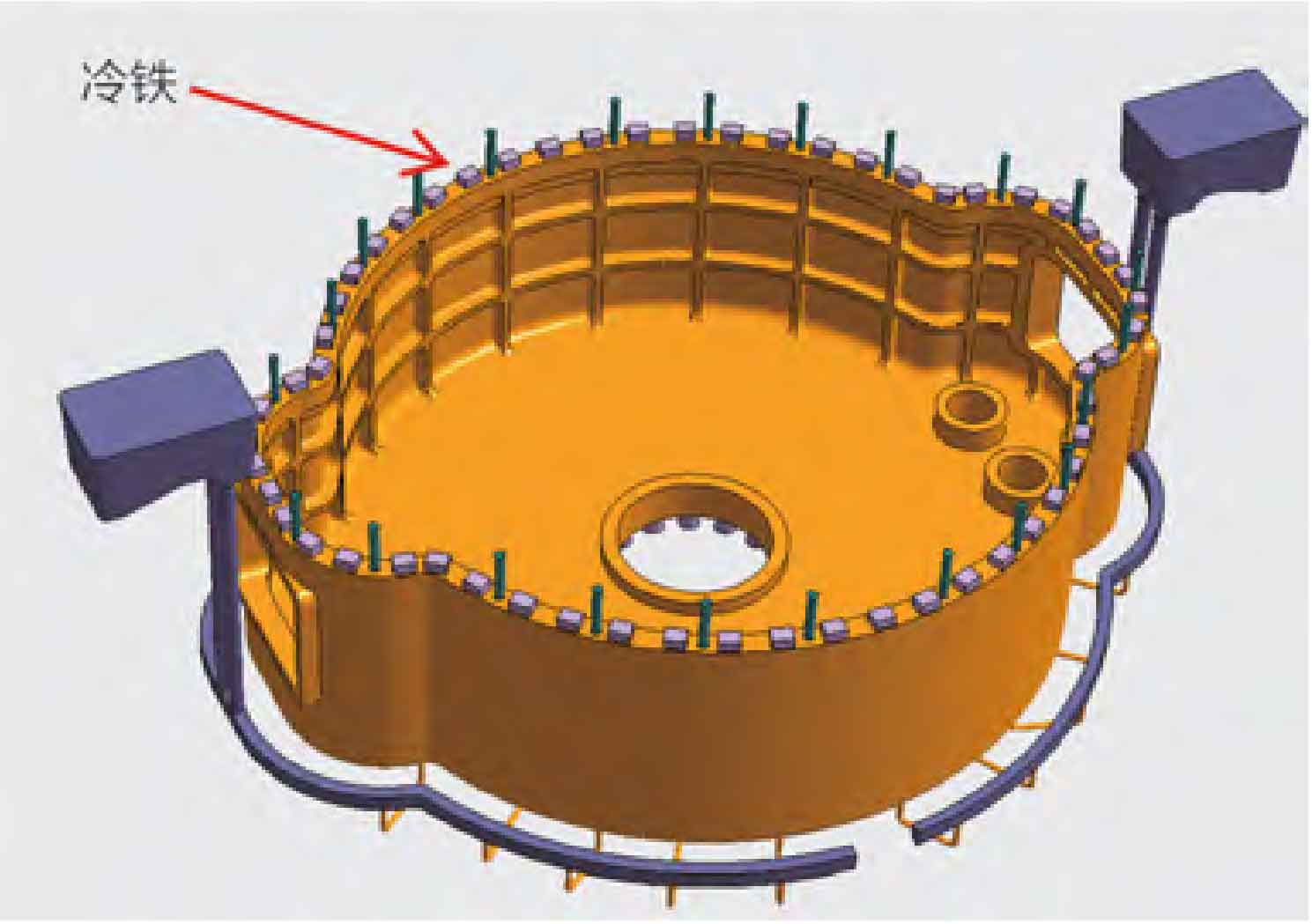
In order to ensure the material compactness of the bottom surface of the ductile iron punch disc, make the molten iron mold filling stable and reduce the risk of sand flushing, the bottom surface is placed in the lower box, and the molten metal is injected from the bottom surface of the ductile iron punch disc through the inner sprue. In order to reduce the collision between the gating system and the sand mold, the mold following runner is used.
2. Cold iron process
The long solidification time of large modulus ductile iron often reduces the spheroidization rate of graphite, or leads to defects such as graphite distortion, graphite floating, graphite coarseness, etc., so it is necessary to use chilled iron to shorten its solidification time. The hot joints of the disc of ductile iron punch are mainly concentrated at the bottom, as shown in Figure 2. Due to structural constraints, it is not suitable to place risers, so chill is mainly placed in the process design. For the casting of thick and large section ductile iron castings, the use of chill is very critical. It can not only strengthen the cooling of castings near the chill, improve the metallographic structure, and prevent graphite from fading. In addition, during mold filling, the temperature of molten iron in contact is continuously reduced, so that the liquid shrinkage of molten iron is advanced, so as to obtain the timely feeding of the gating system and minimize the shrinkage of castings after the solidification of the gating system.
3. Pouring system
Based on the process design principle of ductile iron large parts, the mass of molten iron is about 40000 kg, and the final section ratio of each unit of the gating system is about Σ S straight: Σ S horizontal: Σ S inner =1:1.2:0.8 to ensure large flow and stability of molten iron.